Aluminium Corrosion Treatment: Comprehensive Insights
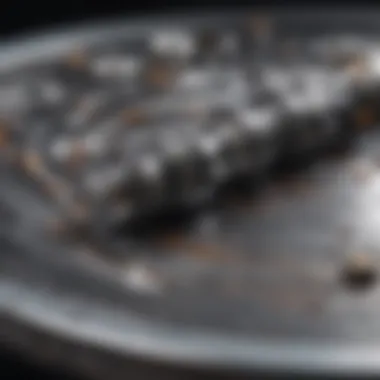
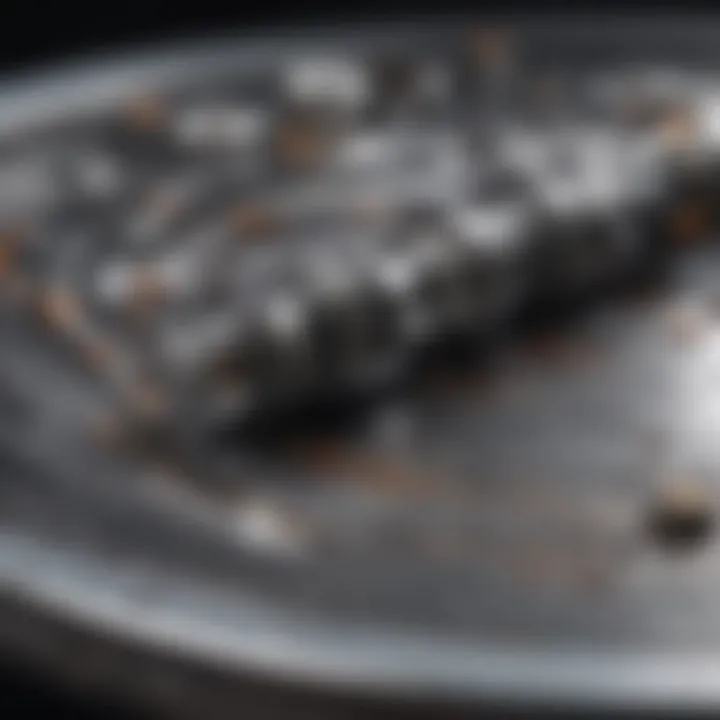
Research Overview
Aluminium corrosion treatment is a complex subject that necessitates a comprehensive understanding of both the chemistry involved and the practical applications of various treatment methods. This section outlines the methodological approaches utilized in researching aluminium corrosion and its implications for various industries. It provides insights into how researchers are tackling the challenges posed by corrosion and the significance of their findings.
Methodological Approaches
The study of aluminium corrosion treatment involves various experimental and analytical methods. Researchers often employ techniques such as:
- Electrochemical Analysis: Techniques like potentiodynamic polarization and electrochemical impedance spectroscopy help in understanding the corrosion behavior of aluminium in different environments.
- Material Characterization: Methods like scanning electron microscopy and energy-dispersive X-ray spectroscopy allow for detailed examination of aluminium surfaces before and after corrosion treatment.
- Field Studies: Long-term exposure tests in real-world environments provide valuable data on how aluminium behaves under various conditions, enhancing the validity of laboratory results.
By integrating these methodologies, researchers are able to formulate a detailed understanding of corrosion mechanisms and evaluate the effectiveness of treatment methods.
Significance and Implications
The implications of studying aluminium corrosion extend beyond mere academic interest. Understanding corrosion treatments has vital significance across multiple sectors, including:
- Aerospace: Aluminium alloys are extensively used in aircraft manufacturing. Maintaining structural integrity through efficient corrosion management is critical for safety.
- Automotive: Lightweight design is paramount in the automobile industry. Effective corrosion treatment can lead to longer vehicle life and lower maintenance costs.
- Construction: As aluminium is often used in building facades and roofing, effective protection against corrosion ensures durability and cost-efficiency in construction materials.
Thus, the ongoing research in aluminium corrosion treatments not only elucidates fundamental scientific concepts but also translates into practical benefits for industries relying on aluminium and its alloys.
Current Trends in Science
Innovations in the field of aluminium corrosion treatment emerge consistently, reflecting the dynamism of scientific research.
Innovative Techniques and Tools
Recent advances include:
- Nanotechnology Applications: Utilizing nanomaterials in coatings can enhance the durability and effectiveness of corrosion resistance.
- Self-Healing Coatings: These materials can autonomously repair damages and restore protective properties, extending the lifespan of aluminium components.
- Smart Sensors: Integration of sensors that monitor corrosion rates in real-time is reshaping predictive maintenance strategies.
The emergence of these techniques indicates a trend towards more efficient and sustainable solutions in corrosion management.
Interdisciplinary Connections
The study of aluminium corrosion treatment is not limited to materials science alone. It interacts with disciplines such as:
- Chemistry: Understanding chemical reactions that lead to corrosion is essential for developing new treatment strategies.
- Mechanical Engineering: The design of structures must consider corrosion resistance to ensure safety and longevity.
- Environmental Science: Evaluating the environmental impact of corrosion and treatment methods is crucial for sustainable development.
This interdisciplinary approach fortifies the understanding of corrosion and enhances the potential for innovative solutions to prevent it.
"Corrosion is a pervasive issue that necessitates ongoing attention in research and application across multiple sectors."
By delving into these sections, readers can achieve a well-rounded comprehension of aluminium corrosion treatment, setting the stage for further exploration of treatment methodologies and practices.
Understanding Aluminium Corrosion
Understanding aluminium corrosion is essential for various industries, from aerospace to construction. Aluminium is prized for its lightweight and corrosion-resistant properties. Nevertheless, it is not immune to degradation, which can significantly affect performance and longevity.
Definition and Types of Corrosion
Corrosion is the gradual destruction of materials due to chemical reactions, primarily with environmental elements like moisture and oxygen. There are several types of corrosion that affect aluminium:
- Uniform corrosion occurs evenly across a surface, leading to a consistent thickness reduction.
- Pitting corrosion is more localized, forming small holes or pits in the material.
- Crevice corrosion happens in confined spaces, where stagnant liquid can create a corrosive environment.
- Galvanic corrosion arises when two dissimilar metals are in contact in the presence of an electrolyte, causing one metal to corrode faster than the other.
Understanding these definitions is crucial. Each type dictates different prevention and treatment strategies, tailored to the unique environmental conditions the aluminium faces.
Electrochemical Processes Behind Corrosion
The electrochemical processes that lead to aluminium corrosion are intricate. At the molecular level, corrosion initiates with the formation of an anode and cathode. This process is often catalyzed by the presence of moisture and ions. For aluminium, the electrochemical reaction can be summarized as follows:
- Anodic reaction: Aluminium oxidizes, releasing electrons and forming aluminium ions.
- Cathodic reaction: Electrons reduce oxygen from the environment, often resulting in water formation.
The balance of these reactions determines the rate and extent of corrosion. Environmental factors, such as electrolyte concentration and temperature, can influence these processes significantly. Therefore, understanding these systems aids in developing effective protective measures.
Factors Influencing Corrosion Rates
Multiple factors contribute to the rate of aluminium corrosion, each interlinked with environmental and material properties:
- Environmental conditions: High humidity, temperature fluctuations, and exposure to saltwater can accelerate corrosion.
- Material composition: Alloys can behave differently based on their elemental makeup. Some alloys have greater resistance to corrosion than others.
- Surface condition: The cleanliness and preparation of the aluminium surface can impact its susceptibility to corrosion. Contaminants can serve as initiation points for corrosion.
- Protective coatings: The presence or absence of coatings, such as paints or anodizing layers, significantly affects corrosion resistance.
Awareness of these factors allows engineers and maintenance professionals to implement better corrosion management strategies, ensuring the structural integrity and longevity of aluminium components.
Common Causes of Aluminium Corrosion
Understanding the common causes of aluminium corrosion is vital for proper management and treatment of this metal. This section focuses on the specific elements that can lead to degradation of aluminium's integrity over time. Familiarity with these causes enables more effective prevention strategies, which can significantly extend the lifespan of aluminium products. Here we will look at three primary factors: environmental conditions, galvanic corrosion in alloys, and chemical exposure.
Environmental Conditions
Environmental conditions play a key role in aluminium corrosion. Factors such as humidity, temperature, and exposure to elements can accelerate the corrosion process. For example, high humidity levels increase the likelihood of moisture accumulation on aluminium surfaces, which can lead to the formation of corrosive agents. Additionally, coastal environments with salt levels can cause pitting and localized corrosion.
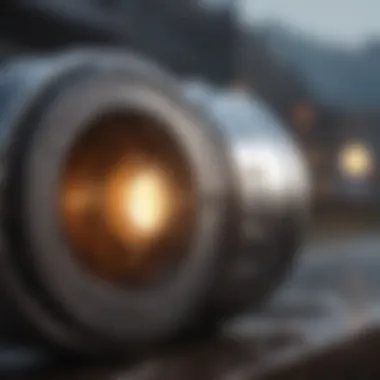
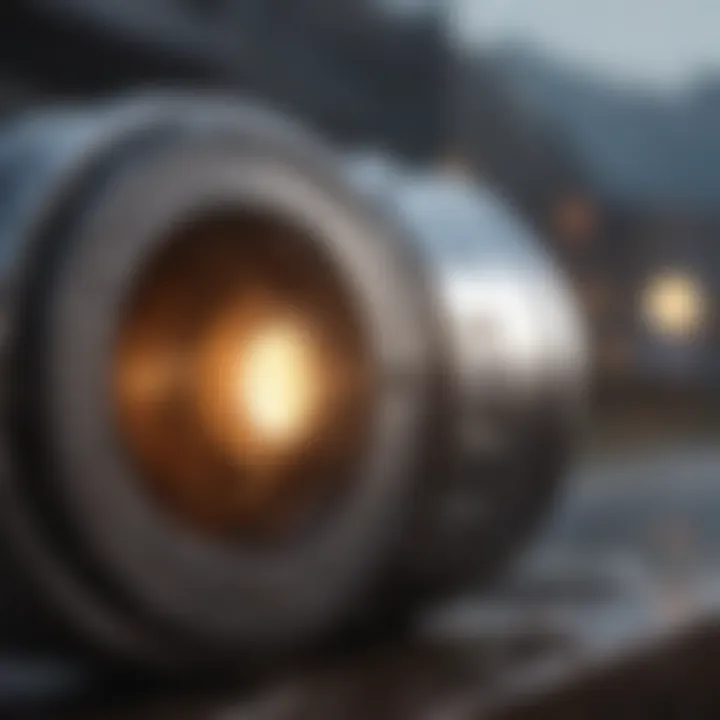
It's also worth noting that both atmospheric and industrial pollutants, such as acids or sulfates, can adversely affect aluminium. For stakeholders, understanding these conditions helps in selecting appropriate protective treatments to mitigate corrosion risks. Regular evaluations of environmental influences are essential.
Galvanic Corrosion in Alloys
Galvanic corrosion is another critical factor when dealing with aluminium alloys. When aluminium is in contact with a more noble metal in the presence of an electrolyte, it can act as an anode and corrode faster. This is particularly relevant in applications where different metals are used together, such as marine and transport industries. The alloys themselves can also display differing corrosion resistance properties.
It's crucial to assess the metallurgy of aluminium components and the types of metals they might encounter. Understanding alloy compositions can help in predicting galvanic reactions and thus avoiding premature failure of materials.
Chemical Exposure and Corrosion
Chemical exposure is a significant contributor to aluminium corrosion. Chemicals such as strong acids or alkalis can react with aluminium and lead to its degradation. Common industries that handle such chemicals, including manufacturing and pharmaceuticals, should take caution. The presence of cleaning agents, solvents, or even chlorides can exacerbate corrosion effects.
To mitigate this, proper material selection is essential. Understanding which chemicals aluminium will come in contact with allows for informed decisions on appropriate protective coatings or barriers.
Methods of Corrosion Treatment
The treatment of aluminium corrosion is vital for prolonging the lifespan of aluminium structures and components. Various methods exist, each with specific advantages and application contexts. Understanding these methods can lead to effective corrosion management, minimizing breakdown and enhancing performance in demanding environments. Effective prevention not only saves costs in repairs and replacements but also ensures safety in structural applications. Let's explore these methodologies in detail.
Preventive Coatings
Preventive coatings play a significant role in corrosion control. These coatings act as a barrier, preventing corrosive agents from reaching the aluminium surface. There are various types of coatings available, including paint, varnish, and specific corrosion-resistant coatings designed for aluminium.
- Advantages:
- Coatings can significantly reduce the rate of corrosion.
- They can enhance the aesthetic appearance of the aluminium surface.
- Many coatings can withstand harsh environmental conditions, providing lengthy protection.
When selecting a coating, considerations include adhesion properties, thickness, and environmental resistance. Surface preparation is crucial. Proper cleaning and priming can ensure that coatings adhere well and do not fail prematurely. It is also important to monitor the integrity of coatings regularly, as any deterioration can expose the aluminium to corrosion risks.
Galvanic Protection Techniques
Galvanic protection is based on the principle of sacrificial anodes. This technique involves connecting a more anodic metal to the aluminium, effectively creating a galvanic cell. Here, the anodic metal corrodes preferentially, protecting the aluminium from corrosion.
- Common materials used for sacrificial anodes:
- Zinc
- Magnesium
- Aluminium alloys
This method is particularly useful in marine environments where aluminium structures are exposed to seawater. It requires careful assessment of the environment to select the appropriate anode material and ensure effective protection. Care must also be taken during installation to avoid unwanted corrosion cells that could compromise the protective benefits.
Cathodic Protection Systems
Cathodic protection is another effective strategy to combat aluminium corrosion, specifically in areas where galvanic protection may not suffice. This method utilizes an external power source to alter the electrochemical environment of the aluminium, turning it into a cathode. Hence, the corrosion process is significantly reduced.
There are two primary types of cathodic protection:
- Impressed Current Cathodic Protection (ICCP): This technique uses a direct current to protect the metal surface. It is useful for large structures such as pipelines and storage tanks.
- Galvanic Cathodic Protection (GCP): Similar to galvanic methods discussed earlier, this approach uses sacrificial anodes. However, it does not require an external power source.
Each method has its advantages and applications depending on specific needs and environmental conditions. Regular monitoring is critical in both techniques to ensure ongoing effectiveness. Appropriate maintenance and system adjustments can maximize protection and extend the life of aluminium structures.
In summary, corrosion treatment methods for aluminium include preventive coatings, galvanic protection techniques, and cathodic protection systems. Understanding when and how to implement these can lead to effective management of aluminium structures in various contexts.
Maintaining thorough documentation related to the treatment methods applied and their performance can help in optimizing future corrosion management strategies.
Surface Treatment Techniques
Surface treatment techniques play a vital role in mitigating aluminium corrosion. By enhancing the surface properties of aluminium, these treatments improve resistance to corrosion, wear, and environmental stresses. Each method has its unique advantages, and understanding them is crucial for choosing the right approach for specific applications.
Anodizing Process
The anodizing process is an electrochemical procedure that forms a protective oxide layer on aluminium. This layer increases corrosion resistance and enhances durability. During anodizing, aluminium acts as an anode in an acid electrolyte bath, facilitating oxidation. The thickness of the oxide layer can be controlled by adjusting the process duration.
Benefits of anodizing include:
- Enhanced aesthetics: Anodized surfaces can be dyed in various colors, improving appearance.
- Improved adhesion: The porous structure allows for better paint and adhesive bonding.
- Increased lifespan: The oxide layer shields aluminium from harmful environmental factors.
Anodizing is widely used in automotive, aerospace, and architectural applications due to its efficacy.
Powder Coating Applications
Powder coating is another effective method for protecting aluminium from corrosion. It involves applying a dry powder to the surface, which is then cured under heat to form a hard, protective layer. This method is ideal for achieving a smooth, uniform finish.
Key aspects include:
- Durability: Powder-coated surfaces are more resistant to chipping, scratching, and fading.
- Variety of finishes: Users can select from a wide range of colors and textures.
- Environmental safety: Powder coating produces minimal volatile organic compounds (VOCs), making it a greener option for surface treatment.
Powder coating is especially popular in the manufacturing of appliances, furniture, and outdoor structures.
Chemical Conversion Coatings
Chemical conversion coatings involve treating aluminium surfaces with a chemical solution to create a thin protective layer. This process enhances corrosion resistance and provides a suitable base for additional coatings.
The characteristics of chemical conversion coatings include:
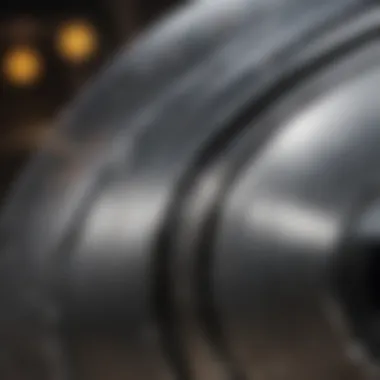
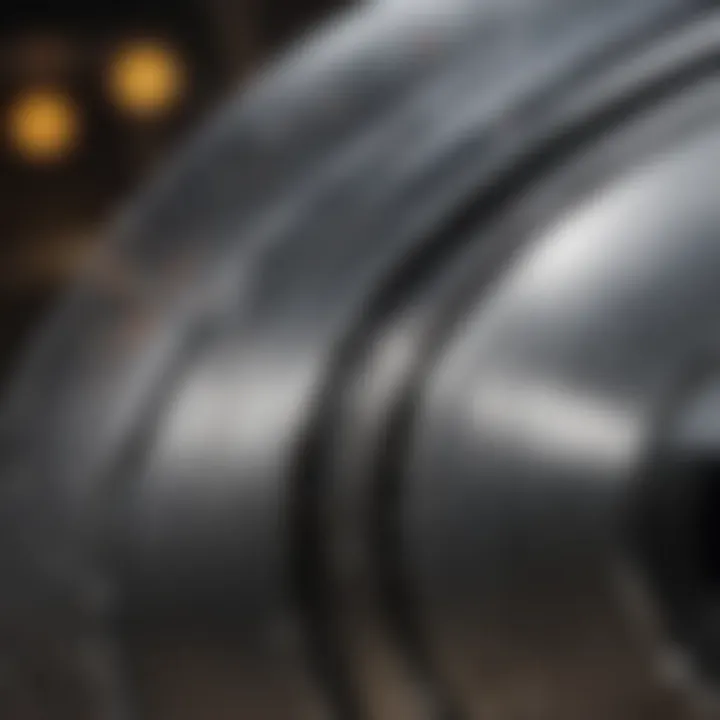
- Adhesion improvement: This method enhances paint adhesion considerably.
- Conductivity: The coating can maintain electrical conductivity, making it useful in electronic applications.
- Customization: Depending on the chemicals used, the coatings can provide a variety of finishes, from matte to gloss.
Chemical conversion coatings are often used in military and aerospace sectors, where both durability and safety are paramount.
In summary, surface treatment techniques such as anodizing, powder coating, and chemical conversion play significant roles in protecting aluminium against corrosion, each with distinct beneficial properties and applications. Understanding these methods is essential for effective corrosion management in practical settings.
Assessment of Corrosion Damage
Assessing corrosion damage is critical for maintaining the integrity and longevity of aluminum structures. Corrosion can occur silently, manifesting in various forms that are often difficult to detect without proper assessment techniques. Not only does this examination reveal the current state of materials, but it also helps in planning maintenance strategies and preventing further deterioration. Accurate assessments can save costs associated with repairs, avoid potential safety hazards, and ensure compliance with industry standards. A well-executed corrosion assessment ultimately extends the service life of aluminum components and structures.
Visual Inspection Techniques
Visual inspection is usually the first step in the assessment of corrosion damage. This technique is straightforward and involves a careful examination of the surface of aluminum structures. Inspectors look for discoloration, flaking, or pitting, which are telltale signs of corrosion. While this method is cost-effective, it has its limitations since some corrosion may be hidden from plain sight.
- Preliminary Assessment: Conducting a visual inspection often begins with checking the overall condition of the structure.
- Surface Cleanliness: Any debris or dirt can obscure defects, hence cleaning the surface can yield more accurate results.
- Documentation: It is important to document all findings consistently for future comparisons.
Visual inspections, although basic, lay the groundwork for more sophisticated evaluation methods.
Electrochemical Impedance Spectroscopy
Electrochemical impedance spectroscopy (EIS) is an advanced technique used to assess corrosion damage. This method measures the electrochemical response of aluminum in a corrosive environment by applying a small alternating current. The impedance data collected can provide insights into the corrosion rate and the effectiveness of protective coatings.
- Data Interpretation: EIS results can be complex, requiring expertise in electrochemistry to interpret.
- Real-time Monitoring: This technique enables continuous monitoring, which can be invaluable in environments prone to rapid corrosion.
- Damage Prediction: Predictive analytics derived from EIS can assist in forecasting when maintenance should be performed.
While more expensive than traditional methods, the data gleaned from EIS is often beneficial for long-term asset management.
Ultrasonic Testing Methods
Ultrasonic testing (UT) is another sophisticated technique employed to assess the thickness of aluminum and detect internal flaws that may not be visible. Sound waves are transmitted through the material, and their reflection indicates the presence of defects or the level of corrosion.
- High Accuracy: UT provides accurate measurements of thickness and can detect localized corrosion.
- Non-Destructive: This method does not harm the material, making it an excellent choice for ongoing assessments.
- Versatile Applications: Ultrasonic testing can be applied to coatings, welds, and joints, making it a crucial tool in numerous industries.
Incorporating these assessment techniques offers a nuanced understanding of corrosion damage, enabling effective interventions and prolonged service life for aluminum components.
Best Practices for Aluminium Maintenance
Maintaining aluminium components is essential to preventing corrosion and extending their lifespan. Best practices in this area can significantly enhance durability, reduce maintenance costs, and promote overall safety in various applications. Effective maintenance ensures that aluminium structures and products are not only visually appealing but also capable of withstanding environmental stresses and chemical reactions that lead to deterioration.
Regular Inspection Schedules
Establishing and adhering to regular inspection schedules is vital in the maintenance of aluminium. By routinely checking for signs of corrosion, such as discoloration, pitting, or scaling, issues can be identified early. This proactive approach prevents minor problems from developing into major failures, which can be costly and time-consuming to repair.
- Frequency of Inspections: Depending on the location and environmental conditions, aluminium products may require checks quarterly or even monthly.
- Key Areas to Inspect: Focus on joints, edges, and areas where water may collect, as these are common spots for corrosion to initiate.
- Documentation: Keep a detailed log of inspection findings to track changes over time and support maintenance planning.
The goal of these inspections is to ensure the longevity of aluminium installations and reduce the potential for unexpected failures.
Appropriate Cleaning Agents
Using the right cleaning agents on aluminium is crucial to avoid damaging the material. Conventional cleaners or abrasive agents can exacerbate corrosion rather than mitigate it. When choosing cleaning products, consider the following:
- Non-Abrasive Cleaners: Select cleaners specifically designed for use on aluminium surfaces. These agents are less likely to scratch or damage the protective oxide layer.
- Avoiding Chlorine Compounds: Chemicals containing chlorine can accelerate corrosion. Opt for safe alternatives like mild detergents or biodegradable products.
- Rinsing: Always rinse thoroughly with clean water after cleaning. Residual chemicals can lead to corrosion if left on the surface.
A focused cleaning routine not only maintains the aesthetic quality of aluminium but also strengthens its protective capabilities, thus prolonging its lifespan.
Environmental Control Measures
Controlling the environment in which aluminium products operate plays a significant role in preventing corrosion. Factors such as humidity, temperature, and exposure to pollutants can accelerate corrosion rates. Consider implementing the following measures:
- Humidity Control: Employ dehumidifiers in enclosed spaces to regulate moisture levels, particularly in storage facilities.
- Temperature Regulation: Equipment that experiences high heat should be monitored closely. Elevated temperatures can increase the rate of oxidation.
- Shielding from Pollutants: If aluminium structures are near industrial or marine environments, consider barriers or coatings to shield against corrosive substances.
Implementing these measures can greatly reduce the susceptibility of aluminium to environmental factors, ensuring better performance and longevity.
Maintaining aluminium effectively means adopting a holistic strategy that combines routine inspections, suitable cleaning practices, and strict environmental control. These practices not only preserve the integrity of the material but also promise substantial cost savings in the long run.
Future Trends in Corrosion Treatment Technologies
The exploration of future trends in corrosion treatment technologies holds significant relevance in the context of aluminium corrosion. As industries evolve and global standards demand higher quality and durability of materials, innovative strategies are essential in addressing corrosion challenges.
Focusing on advanced technologies, these trends highlight critical developments in the coatings, detection methods, and research areas that promise to transform the way corrosion is managed. This forward-looking approach aims to enhance the longevity and performance of aluminium products, which are frequently exposed to harsh environmental conditions.
Innovations in Coating Materials
Innovative coating materials are at the forefront of combating aluminium corrosion. The advancements include the use of nanotechnology, which facilitates the creation of thinner yet stronger coatings that provide excellent protection against corrosion. These coatings often incorporate self-healing properties which allow them to repair minor damages autonomously.
Furthermore, new polymers and hybrid materials offer high flexibility and resistance to various forms of corrosion. These innovations not only improve the longevity of aluminium but also reduce the need for frequent maintenance, thus lowering overall lifecycle costs. Industries are increasingly adopting these coatings to protect components ranging from aerospace elements to automotive parts.
Some key benefits of these innovations include:
- Lightweight construction
- Enhanced adhesion and durability
- Oil and water repellency
- Reduced environmental impact
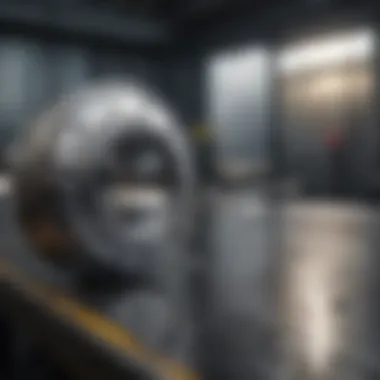
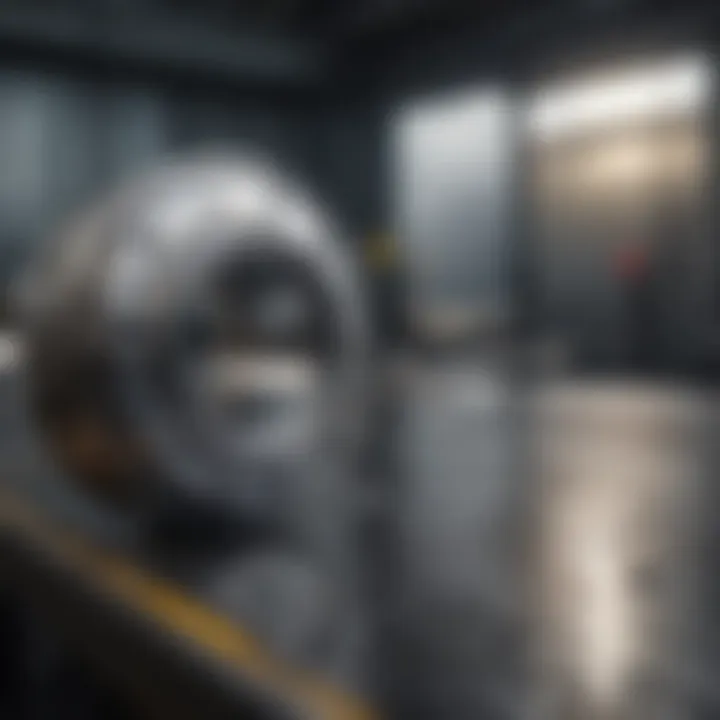
Smart Technologies for Detection
In recent years, the emergence of smart technologies has transformed the detection of corrosion. Tools employing sensors and IoT (Internet of Things) capabilities allow for real-time monitoring of aluminium structures. This technology provides precise data on corrosion rates and conditions, which can prevent severe structural failures.
For example, the integration of electrochemical sensors can detect corrosion potential and current flows, which are vital indicators of material integrity. Similarly, digital imaging and analysis techniques can pinpoint early signs of corrosion, allowing for proactive maintenance actions.
Such smart detection systems offer numerous advantages:
- Increased reliability in maintenance timings
- Cost savings through optimized resources
- Enhanced safety for personnel and infrastructure
"Proactive monitoring through smart technologies serves to extend the service life of aluminium and improve overall reliability."
Research Directions in Corrosion Mitigation
Research into corrosion mitigation continues to advance, focusing on understanding the underlying mechanisms of aluminium corrosion better. Fundamental studies aim to reveal how different environmental factors impact corrosion rates and effectiveness of treatments.
Notably, interdisciplinary research combining materials science, chemistry, and engineering is crucial in this journey. This collaboration can lead to breakthroughs in creating more effective corrosion inhibitors and protective strategies. Areas for future research include:
- Development of bio-inspired materials that naturally resist corrosion
- Exploration of non-toxic and eco-friendly inhibitors
- Analysis of corrosion behavior under extreme conditions (e.g., deep-sea environments)
By investing in these research directions, industries can ensure continuous improvement in corrosion treatment methodologies. This not only fosters innovation but also aligns with global sustainability goals, making it a pertinent area of focus for future development.
Case Studies of Corrosion Treatment
Case studies illustrate real-world applications of aluminium corrosion treatment strategies. They offer insights into how theoretical approaches translate into effective solutions in different environments. Understanding these case studies is critical. They help practitioners to learn from past successes and failures. Additionally, they provide a practical context for the principles discussed in this article.
Industrial Applications
In industrial settings, aluminium components are subject to various corrosive conditions. These can include elevated temperatures and exposure to aggressive chemicals. A case study involving the use of anodizing on aluminium components in the aerospace sector highlights the effectiveness of surface treatments.
Anodizing improves the corrosion resistance of aluminium. In one instance, aerospace manufacturers adopted this method as a standard. The results showed a marked decrease in corrosion-related failures. This case underscores the importance of tailored corrosion treatments based on specific industrial requirements.
- Key takeaways from industrial applications:
- Anodizing provides robust protection against corrosion.
- Regular maintenance is crucial to prolonging the life of components.
- Industry specific solutions yield better performance.
Transport Sector Analysis
The transport sector faces unique corrosion challenges. Vehicles and infrastructure are often exposed to moisture, road salts, and pollutants. A notable case involved the implementation of galvanic protection systems on public transport buses. The study detailed how these systems significantly reduced corrosion rates.
By integrating sacrificial anodes, transport authorities were able to extend the service life of their vehicles. This success not only reduced maintenance costs but also enhanced operational reliability. The insights here are valuable for urban planners and transport logistics teams in managing assets effectively.
- Important aspects of transport sector treatments:
- Galvanic protection offers a cost-effective solution.
- Predictive maintenance strategies improve asset longevity.
- Environmental conditions should guide treatment choices.
Marine Environment Challenges
Marine environments are particularly challenging for aluminium due to factors like saltwater exposure and biofouling. A case study from a coastal city investigated the use of chemical conversion coatings on aluminium boat hulls. The city aimed to mitigate the corrosive effects of saltwater.
Results from this case demonstrated that chemical conversion coatings reduced corrosion effectively. Furthermore, routine inspections were critical in maintaining the integrity of the hulls. Through this case, one learns that proactive measures can keep marine structures safe from corrosion.
- Critical factors for marine corrosion treatment:
- Chemical conversion coatings are effective for harsh conditions.
- Regular inspections can prevent severe damage.
- Understanding local environmental challenges is essential.
Case studies can guide future corrosion treatment strategies and help industries implement effective solutions based on evidence and detailed analysis.
Closures and Recommendations
Understanding aluminium corrosion treatment is crucial for industries and sectors where aluminium materials are prevalent. This article has offered comprehensive insight into the mechanisms, causes, and treatment strategies for aluminium corrosion. By synthesizing various studies and practices, we bring together essential findings that reinforce the significance of this subject.
The analysis indicates that robust corrosion management is integral for maintaining the longevity and performance of aluminium products. Thus, ongoing education in maintenance strategies and treatment methods is vital. Professionals in engineering, metal fabrication, and chemical processing should prioritize gaining expertise in corrosion prevention techniques. This knowledge gap can lead to costly damages if not addressed.
Key recommendations include:
- Implementing regular inspections tailored to environmental conditions.
- Training staff on effective cleaning agents suitable for aluminium surfaces.
- Exploring advanced technologies for continuous monitoring of corrosion rates.
Future efforts should focus on integrating findings from research into practical applications, ensuring a lifecycle approach to corrosion management. This will not only prolong the utility of aluminium components but also contribute to sustainability efforts by minimizing waste and resource use.
"Preventative measures are invariably more effective than remedial ones. Prioritizing proper treatment keeps systems operational and reduces breakdown risks."
Summary of Findings
Throughout this article, we have highlighted critical areas concerning aluminium corrosion treatment. Not only did we examine different corrosion types, but we also analyzed the fundamental factors influencing corrosion rates. The following key findings emerged:
- Aluminium is susceptible to several forms of corrosion, including pitting and galvanic corrosion.
- Environmental factors, such as humidity and exposure to salt, significantly increase corrosion risks.
- Treatment methods such as anodizing and protective coatings can effectively slow down the corrosion process.
- Inspection techniques play a vital role in early detection and management of corrosion, ensuring timely interventions.
These findings underscore the urgency for proactive measures and the implementation of best practices across various industries.
Future Research Needs
The exploration of aluminium corrosion treatment is ongoing, and several areas require further investigation:
- Innovative Coating Materials: Research into new, more effective coatings that offer long-lasting protection without harming the aluminium substrate is essential.
- Smart Detection Technologies: The development of advanced monitoring systems using IoT and sensor technologies can facilitate real-time assessments of corrosion levels.
- Behavioural Studies: Understanding the behaviour of aluminium alloys in different environmental conditions can lead to targeted treatment strategies.
By pursuing these lines of inquiry, researchers can enhance existing paradigms and contribute significantly to the field of materials science, ultimately fostering greater durability and resilience in aluminium applications.