Aluminium Welding Techniques and Applications
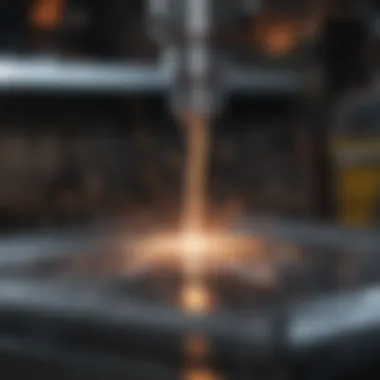
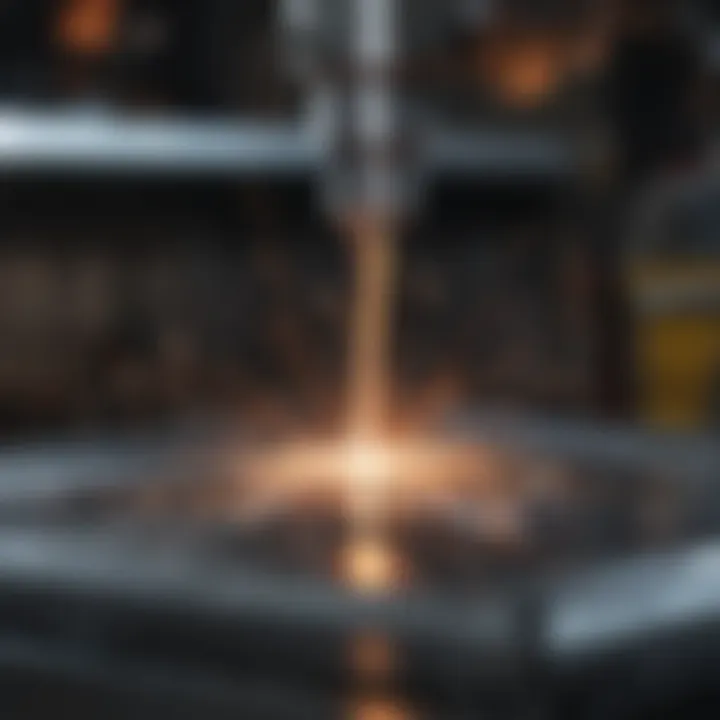
Intro
Aluminium welding is an essential process utilized across various industries. Understanding the techniques, challenges, and the underlying principles can significantly enhance the quality of welded products. Due to aluminium's unique properties such as lightweight and corrosion resistance, it has gained popularity in sectors like aviation, automotive, and construction. This article aims to explore these facets in detail, providing insights that cater to students, educators, researchers, and industry professionals.
Research Overview
Methodological Approaches
The research into aluminium welding techniques incorporates both experimental and theoretical methodologies. Studies often involve mathematical modeling to understand heat distribution during the welding process. Experimental setups allow researchers to test different welding methods in real-world scenarios. Observations during these experiments can provide insights into optimal welding conditions, such as temperature and speed, which are vital for producing strong joints.
Additionally, metallurgical analysis plays a crucial role. Characterization techniques such as X-ray diffraction and scanning electron microscopy help researchers evaluate crystallographic properties and microstructures of welded joints, contributing to a more comprehensive understanding of how different alloys behave under various welding conditions.
Significance and Implications
Understanding aluminium welding is significant not just for academic purposes but also for its implications in industrial applications. Improved welding techniques can lead to stronger and more durable products, reducing costs and enhancing safety. For example, in aerospace applications, the integrity of a welded joint can be the difference between a successful flight and catastrophic failure. Therefore, continual advancements in aluminium welding techniques are paramount.
Current Trends in Science
Innovative Techniques and Tools
Recent advancements in technology have introduced innovative welding techniques such as laser welding and friction stir welding. Laser welding allows for precise control over the heat input, resulting in less distortion and stronger welds. Friction stir welding is unique in that it doesn't involve melting the material, which can lead to enhanced mechanical properties. Understanding these advanced methods is important for engineers looking to improve their welding processes.
Interdisciplinary Connections
Aluminium welding is not a standalone field; it connects with various disciplines including materials science, mechanical engineering, and even robotics. For example, robotics plays a vital role in automating the welding process, increasing efficiency and precision. Collaboration among researchers in these fields fosters innovation and enhances the understanding of materials and processes.
"By continuing to innovate and research in aluminium welding, we ensure that our industries can meet the growing demands for safety and efficiency."
Overall, exploring aluminium welding techniques highlights not just the methods used but also the broader implications for different industries. This understanding is critical for those involved in engineering fields, allowing them to apply knowledge effectively in their work.
Foreword to Aluminium Welding
Aluminium welding is a vital area within the broader context of metal fabrication and manufacturing. Understanding the principles and techniques of welding aluminium is essential for engineers, technicians, and those involved in designing structures or products that incorporate this versatile material. The unique properties of aluminium, such as its lightweight nature combined with significant strength, make it an ideal candidate for various applications across many industries. Furthermore, the increasing demand for sustainable and efficient manufacturing processes has emphasized the relevance of aluminium welding as a key component in modern engineering practices.
One critical aspect of aluminium welding is its significance in creating strong and durable joints. Given the lightweight property of aluminium, welded connections not only provide structural integrity but also contribute to overall weight reduction in products. This is particularly important in sectors such as aerospace and automotive, where every kilogram saved can lead to enhanced performance and fuel efficiency.
Definitions and Basics
At its core, aluminium welding is the process of joining aluminium materials by melting and fusing them together. This process involves the application of heat, which can be generated through various methods such as electric arcs or gas flames. Given aluminium's specific characteristics, such as its high thermal conductivity and low melting point, particular attention must be given to the techniques and equipment used in the welding process.
The different methods of aluminium welding can be defined by the energy source and welding principle applied. Common methods include Gas Metal Arc Welding (GMAW), Tungsten Inert Gas Welding (TIG), and Metal Inert Gas Welding (MIG). Each method has its own set of advantages and limitations based on the specific requirements of the welding application. Choosing the appropriate technique is central to achieving the desired results in terms of strength, appearance, and overall performance of the welded joint.
Historical Context and Development
The history of aluminium welding dates back to the early 20th century when it became essential in industrial applications. The first successful attempts to weld aluminium involved gas welding techniques, which were limited in application due to the high thermal conductivity of the material. Over time, advancements in welding technology led to the development of electric arc techniques, which significantly improved the capability to weld aluminium effectively.
By the mid-20th century, industries began to recognize the advantages of aluminium in construction and manufacturing. This increase in demand led to the refinement of welding processes and equipment specifically designed for aluminium materials. The development of new filler materials, as well as enhancements in shielding gases, has also played a role in improving the quality of aluminium welds over the decades.
In recent years, welding technology has seen significant innovations, particularly with the introduction of automated welding systems and sophisticated control methods. These developments have further increased the efficiency and precision of aluminium welding, making it an even more crucial aspect of modern manufacturing.
Fundamental Principles of Welding Aluminium
Aluminium welding requires a solid understanding of its fundamental principles. These principles govern the behavior of aluminium when exposed to high temperatures and stress. Recognizing the unique characteristics of aluminium is essential for ensuring strong, reliable welds. Effective welding techniques depend on these fundamental aspects, which include thermal properties and metallurgical behavior.
Thermal Properties of Aluminium
Aluminium has distinctive thermal properties that greatly influence its welding processes. It has a high thermal conductivity, which allows heat to dissipate quickly through the material. This quality can create challenges during welding since rapid cooling may lead to various issues, like cracking or poor fusion. Therefore, welders must adjust their techniques to account for this rapid heat loss.
Moreover, aluminium has a relatively low melting point compared to other metals, around 660 degrees Celsius. This aspect means that the welder must have precise control over the heat input to avoid overheating the material. If the temperature exceeds specifications, it may result in distortion or weakened joints.
Another critical point is the thermal expansion of aluminium. When subjected to heat, it expands more than other metals. Understanding this expansion is necessary to prevent warping and misalignment during the welding process.
Metallurgical Behavior During Welding
The metallurgical behavior of aluminium during welding is complex and needs careful study. When welding, aluminium does not only melt but undergoes significant changes in its microstructure. The melting process leads to the formation of a molten pool, where different metallurgical phenomena can occur.
One key concern during welding is the formation of intermetallic compounds, which may influence the weld's strength and ductility. These compounds arise due to the reaction between molten aluminium and other elements, such as impurities or the filler material used during the welding process.
Furthermore, the heat-affected zone (HAZ) in aluminium welding can be sensitive. This region can experience alterations in properties, leading to potential weaknesses in the welded component. It is crucial to tailor welding techniques to minimize the HAZ and its adverse effects.
To sum up, both thermal properties and metallurgical behavior play vital roles in the successful welding of aluminium. Understanding these principles aids welders in producing high-quality, durable welds, with fewer defects. This knowledge is indispensable for students, researchers, and professionals involved in the field of aluminium welding.
"Understanding metallurgical behavior during welding can significantly improve the quality of the final product."
By grasping these fundamental principles, one can navigate the complexities of aluminium welding techniques more effectively.
Types of Aluminium Welding Techniques
The welding of aluminium requires specific techniques that cater to its unique properties. Understanding these techniques is essential for achieving strong and reliable welds. This section delves into various aluminium welding methods that have been developed to address the material's challenges and enhance its applications across industries.
Gas Metal Arc Welding (GMAW)
Gas Metal Arc Welding, commonly referred to as GMAW or MIG (Metal Inert Gas) welding, is a widely used technique for aluminium welding. In GMAW, a continuous solid wire electrode is fed through a welding gun, creating an arc between the wire and the aluminium workpiece. The process uses an inert gas, usually argon or a mixture of argon and carbon dioxide, to shield the weld from contamination.
One of the key advantages of GMAW is its high deposition rate, which leads to faster weld completion. This can be particularly beneficial in high-production environments. Furthermore, GMAW is user-friendly, making it accessible for both novice and experienced welders alike. However, it is crucial to maintain clean surfaces since contaminants can adversely affect the weld quality.
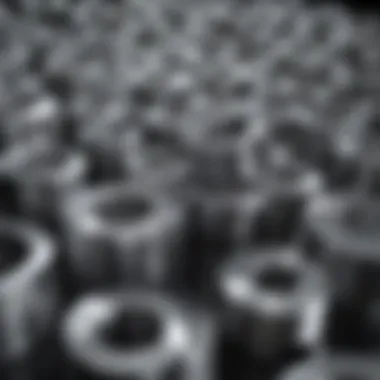
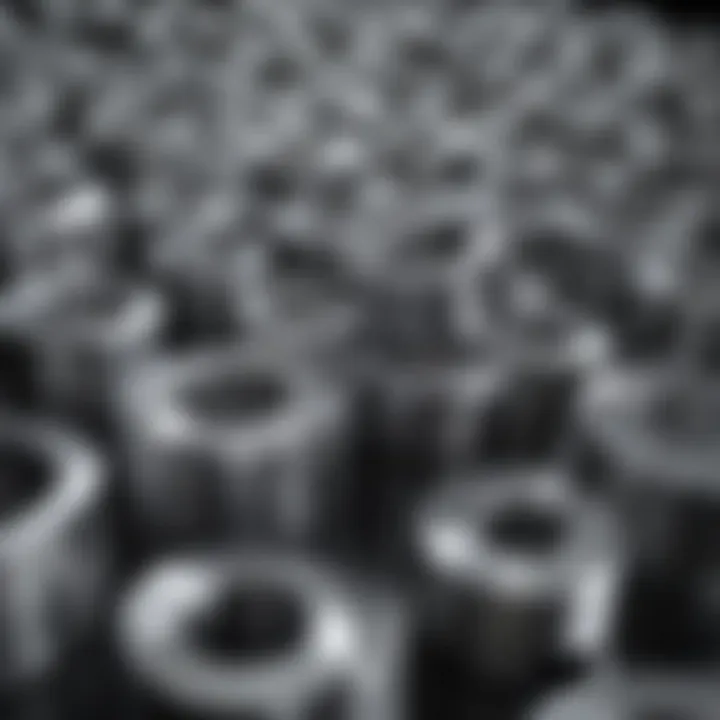
Tungsten Inert Gas Welding (TIG)
Tungsten Inert Gas (TIG) welding is another important method used for welding aluminium. This technique employs a non-consumable tungsten electrode to produce the weld. Like GMAW, TIG also uses an inert shielding gas, typically pure argon, to protect the weld from the atmosphere.
TIG welding is known for its precision and ability to produce high-quality welds, especially in thin materials. Its versatility allows for the welding of various aluminium alloys and thicknesses. The process demands a greater skill level from the welder compared to GMAW, resulting in longer weld times. Yet, the ability to control the heat input makes it an indispensable technique, particularly in applications demanding aesthetics and strength.
Metal Inert Gas Welding (MIG)
Metal Inert Gas (MIG) welding shares similarities with GMAW but is often regarded in industries as a variant. The primary difference lies in the continuous feed of the wire and the types of shielding gases used. MIG welding employs a combination of inert and active gases to yield different welding characteristics.
MIG welding is advantageous for its speed and efficiency, making it suitable for mass production. Its adaptability allows welding of not just aluminium but also various other metals. However, like GMAW, cleanliness is paramount to prevent defects. Casual performance with MIG leads to issues such as porosity or incomplete fusion.
Resistance Welding Techniques
Resistance welding encompasses several methods that rely on heat generated by electrical resistance. Spot welding is a notable application of this technique for aluminium. In this method, two workpieces are pressed together, and an electrical current is passed through, generating localized heat that fuses the surfaces.
Resistance welding is efficient for joining parts without additional filler materials. It is especially useful in assembly lines where rapid welding cycles are necessary. Nonetheless, this technique requires accurate control of parameters such as current, pressure, and time to avoid distortion or inadequate weld formation.
Friction Stir Welding (FSW)
Friction Stir Welding (FSW) is a solid-state joining process that has gained traction in recent years. The technique involves a rotating tool that creates friction and heat at the joint interface between two pieces of aluminium. As the tool advances, the material softens and is mixed, forming a weld without melting the base material.
FSW is beneficial for its unique ability to create strong and defect-free welds, particularly in thicker sections of aluminium. It offers advantages such as reduced distortion and lower energy consumption compared to conventional welding methods. However, the requirement for specialized equipment can limit its widespread adoption in some industries.
Understanding these techniques provides insight into how aluminium welding can be optimized for various applications. Each method has its strengths and challenges, influencing the selection process based on project requirements.
Advantages of Aluminium Welding
Welding aluminium offers distinct advantages that make it a preferred choice in various industries. Understanding these benefits is essential for professionals involved in design and manufacturing. The lightweight properties of aluminium combined with its strength contribute significantly to structural integrity. Additionally, the flexibility of welding techniques adds to the appeal of aluminium as a construction material.
Lightweight and Strong Structures
Aluminium's most notable characteristic is its lightweight nature. This property allows for easier handling and manipulation during construction. As a result, structures that use aluminium tend to be less massive compared to those made from steel or other metals. Such projects can be designed with less supporting material, improving overall efficiency.
From load-bearing walls to vehicle frames, the strength-to-weight ratio of aluminium is impressive. For instance, aerospace and automotive sectors heavily utilize aluminium for components like aircraft bodies and car bodies. This choice enhances performance due to reduced weight without sacrificing strength.
- Materials Science: When properly welded, aluminium maintains its mechanical properties, securing reliable performance under stress.
- Design Flexibility: Engineers can create complex shapes and structures, enhancing design possibilities.
Ultimately, lightweight and strong aluminium structures lead to significant cost savings in both manufacturing and transportation.
Corrosion Resistance Benefits
Corrosion resistance is another major advantage of welding aluminium. Unlike many other metals, aluminium forms a natural oxide layer when exposed to air. This layer provides a protective barrier that helps prevent further oxidation. As a result, aluminium structures often exhibit longevity and durability, even in harsh environments.
In applications like marine construction, where exposure to moisture is a concern, aluminium's resistance to corrosion becomes invaluable. Maintenance costs are lower as well, since structures do not require frequent protective coatings or treatments. This property also supports sustainability initiatives, as using aluminium can lead to less resource consumption over the material's lifecycle.
In summary:
- Natural Protection: The oxide layer significantly enhances resistance against wear and tear.
- Long Lifespan: Structures have a longer operational life, reducing the frequency of repairs.
Challenges in Welding Aluminium
Welding aluminium presents unique challenges that significantly influence the outcomes of the process. Understanding these challenges is crucial for achieving high-quality welds. This section will explore key difficulties faced in aluminium welding, specifically the sensitivity to contamination and thermal expansion issues. These factors demand meticulous attention during the welding operation to ensure the integrity and strength of the final product.
Sensitivity to Contamination
Aluminium is particularly sensitive to contamination. Even the smallest amount of dirt, oil, or paint on the surface can lead to poor weld quality. Contaminants can create defects such as porosity, lack of fusion, and other structural weaknesses. This is especially problematic since aluminium oxide forms rapidly on the metal's surface, which can hinder effective bonding during the welding process.
To mitigate contamination, it is critical to implement thorough cleaning protocols. Typical cleaning methods include using solvents and abrasives to remove surface impurities. Further, pre-welding procedures should ensure that the environment is controlled to minimize dust and airborne contaminants.
Keeping surfaces clean helps maintain the quality of the weld. In welding environments, practitioners should develop routines to inspect and prepare materials. A clean work area lowers the risk of introducing foreign particles into the weld zone.
Thermal Expansion Issues
Thermal expansion poses another significant challenge in aluminium welding. When aluminium is heated, it expands, and upon cooling, it contracts. This characteristic can lead to warping or distortion in the welded components. Such deformation can affect the alignment and assembly of weld joints, which is particularly crucial in precision applications.
To address expansion issues, careful management of heat input is necessary. Techniques such as controlling welding speed and using appropriate filler materials can help maintain the dimensions of the workpiece. Additionally, implementing weld strategies that distribute heat evenly can reduce the potential for distortion.
Moreover, designing weld joints with allowances for thermal expansion can be beneficial. Engineers should consider the specific characteristics of the materials and the application environment when planning designs. Awareness of thermal dynamics during the welding process is invaluable to achieve durability and structural integrity in the final product.
In summary, comprehending the challenges of welding aluminium is essential for engineers and welders alike. The impact of contamination and thermal expansion on weld quality cannot be overstated. By adopting best practices in surface preparation and heat management, professionals can enhance the effectiveness and reliability of aluminium welded components.
Welding Equipment and Materials
In the context of aluminium welding, the selection of appropriate equipment and materials is key to achieving high-quality results. The proper setup can significantly affect the strength, durability, and appearance of the weld. Moreover, understanding the equipment involved lays the groundwork for improving the efficiency of welding procedures.
Welding Machines and Tools
Aluminium welding utilizes various machines and tools, each designed to serve specific purposes in the welding process. Electric arc welding machines, for example, provide a steady power supply crucial for aluminium's low melting point. These machines come with options like direct current (DC) or alternating current (AC), and the choice can affect the outcome of the weld.
Common types of welding machines used for aluminium include:
- TIG (Tungsten Inert Gas) Welders: These units provide precise control necessary for thin materials. Their versatility makes them suitable for intricate work.
- MIG (Metal Inert Gas) Welders: Known for their efficiency, these machines are often used for larger, thicker pieces of aluminium due to their speed and ease of use.
- Multi-process Welders: These can switch between different welding methods, providing flexibility for diverse projects.
In addition to machines, proper tools such as clamps, grinders, and safety equipment also play critical roles in ensuring a smooth welding process. For instance, using the correct clamps can hold materials securely, helping to maintain alignment during welding.
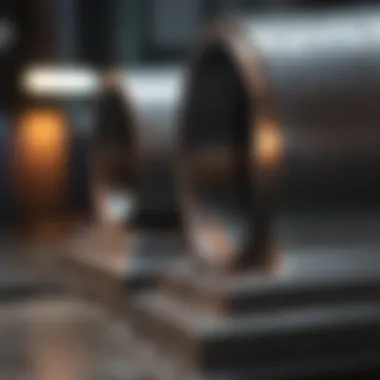
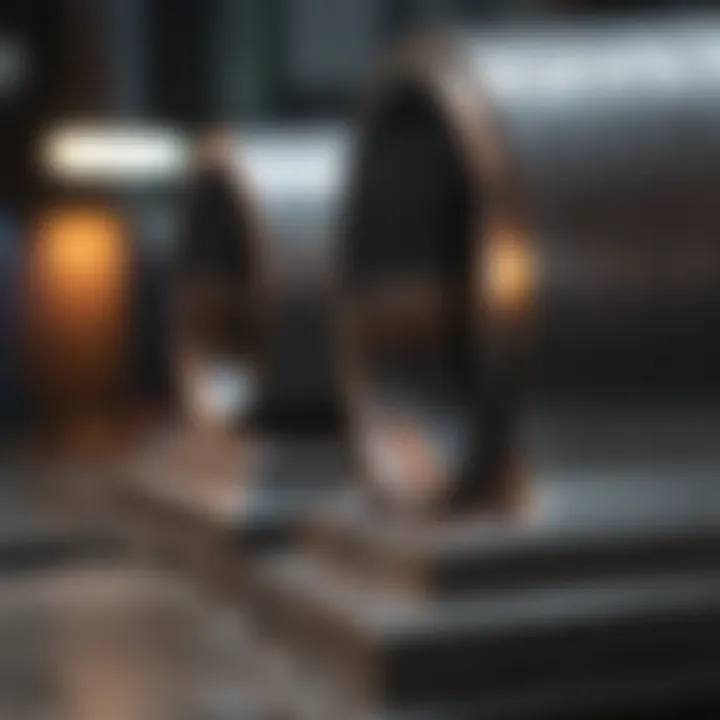
Choosing Filler Materials
The choice of filler material directly influences the mechanical properties and aesthetics of the weld. In aluminium welding, filler rods or wires can vary depending on the alloy being welded and the specific requirements of the application. When selecting a filler material, one must consider the following:
- Compatibility with the Base Material: Different aluminium alloys may require different filler materials. For instance, if welding 6061 alloy, a filler material like 4047 may be appropriate to enhance weld strength.
- Weld Position and Application: In certain applications, a higher percentage of silicon in the filler may reduce porosity and enhance flow, which is essential for achieving a smooth finish.
- Properties Required in the Weld: Factors such as corrosion resistance, strength, and electrical conductivity are vital when determining which filler to use.
The use of appropriate filler materials not only enhances the integrity of the weld but also minimizes defects. Careful consideration at this stage can save time and cost in later stages of production.
Selecting the right equipment and materials in aluminium welding is not merely technical; it is also a strategic decision that impacts the overall project success.
In summary, understanding welding equipment and materials is crucial for anyone working with aluminium. The right machines, tools, and filler materials set a strong foundation for achieving high-quality welds and advancing one’s skills in this vital area of engineering.
Alloy Types in Aluminium Welding
An understanding of alloy types is crucial in aluminium welding. This knowledge determines the success of welded joints and the performance of the finished product. Various aluminium alloys exhibit different properties. These properties influence not just the welding process, but also the applications for which the welded components are suited. Recognizing the characteristics of alloys provides insights into their welding behavior and the expected outcomes.
Commonly Used Aluminium Alloys
Aluminium alloys generally fall into two categories: wrought and cast.
- Wrought alloys are those produced by deformation processes like rolling or extruding. Their common series include:
- Cast alloys have different designations, often characterized by higher silicon content. Examples include:
- 1XXX series: Pure aluminium, which boasts excellent corrosion resistance and high thermal conductivity.
- 2XXX series: Copper alloyed, recognized for high strength but less corrosion resistance.
- 6XXX series: Mainly magnesium and silicon, famous for good workability and corrosion resistance.
- A356: Known for good mechanical properties and weldability.
- A380: Excellent fluidity and corrosion resistance, suitable for intricate shapes.
These alloys cover a range of applications, from aerospace to automotive components. Each series has unique attributes that influence welding outcomes.
Influence of Alloy Composition on Weldability
The composition of an aluminium alloy directly affects how it performs during the welding process. Several factors come into play:
- Strength vs. Weldability: Higher strength alloys, like those in the 2XXX series, often present challenges in terms of weldability. They may be susceptible to hot cracking.
- Filler Material Compatibility: Not all filler materials work with every alloy. Understanding the recommended filler for each type ensures better integration and minimizes defects.
- Heat Treatment Responses: Some alloys, such as 7XXX series, are heat treatable. When welded, they may lose some of their properties unless appropriate steps are taken.
- Hydrogen Embrittlement: Alloys can absorb hydrogen during welding, impacting their mechanical performance. This is particularly concerning in high-strength alloys.
Important Note: Proper selection of alloy types and understanding their characteristics is essential for achieving effective welds. It enables better decision-making regarding the welding technique and parameters.
Defects in Aluminium Welded Components
Understanding defects in aluminium welded components is essential for several reasons. Defects can significantly affect the performance, strength, and longevity of the welded joints. Identifying these defects is a key part of quality control in the welding process. This section discusses the common defects encountered in aluminium welding, their causes, and the methods used for inspection and testing.
Common Defects and Their Causes
Welded aluminium components can suffer from various defects. Recognizing these issues is vital for ensuring the integrity of the final product. Some common defects include:
- Porosity: This defect appears as small holes or voids within the weld. It occurs when gases are trapped during the solidification process. Factors contributing to porosity include contamination of the weld area and improper gas shielding.
- Cracking: Cracks can form in the weld or base metal. They often result from rapid cooling or improper heat input. Common causes of cracking include excessive heat during welding and residual stresses.
- Lack of Fusion: This occurs when the weld metal does not properly fuse with the base material. It often stems from insufficient heat or poor technique. It can weaken the joint.
- Inconsistency in Weld Appearance: Uneven bead shape may hint at varying travel speeds or variable arc length during the welding process. This inconsistency can indicate a poor technique or equipment issues.
It is critical to analyze these defects to prevent them in future welds. Understanding their root causes helps to develop better welding practices and improve the quality of the welds.
Inspection and Testing Methods
To ensure the quality of aluminium welded components, several inspection and testing methods are employed. Each method targets different potential failure points. Some common techniques include:
- Visual Inspection: This is the simplest method. Inspectors visually assess welds for any obvious defects such as cracks or improper bead shapes. While this method is quick, it is limited in detecting internal defects.
- Ultrasonic Testing (UT): This non-destructive method uses high-frequency sound waves to detect internal flaws. It is effective at identifying cracks and voids within the material without damage.
- Radiographic Testing (RT): This method employs X-rays or gamma rays to view the internal structure of the weld. It is a powerful tool for detecting porosity and lack of fusion, providing a comprehensive picture of weld integrity.
- Dye Penetrant Testing (DPT): This technique uses liquid dye to reveal surface-breaking defects. After applying the dye, it is drawn into defects, making them visible under UV light.
These methods facilitate a systematic approach to quality assurance in aluminium welding. Regular inspection ensures that any defects can be identified and rectified early in the process.
Regular inspection of welded aluminium components is not just about maintaining quality, but also about safeguarding the longevity and safety of the applications they serve.
To effectively manage defects in aluminium welding, it is necessary to have a keen understanding of potential flaws, their causes, and robust practices for inspection. By addressing these aspects, the welding process can be optimized, leading to stronger, more reliable welded joints.
Preventive Measures for Welding Defects
Minimizing welding defects is crucial to ensure the integrity and performance of aluminium welded components. The potential issues that can arise during the welding process lead to significant problems, including reduced strength and lifespan of the final product. By implementing preventive measures, it is possible to mitigate these risks effectively. Key aspects include maintaining equipment, ensuring a clean work environment, and adhering to the correct techniques and training.
Maintenance of Equipment and Work Environment
Proper maintenance of welding equipment is fundamental. Equipment that is well-maintained operates efficiently, producing high-quality welds. Regular checks on welding machines, cables, and tools help identify and address wear and tear. This proactive approach prevents sudden breakdowns that could lead to defects.
In addition to equipment upkeep, the work environment plays a significant role in welding quality. A clean and organized workspace reduces the likelihood of contamination, which can affect weld quality. This includes keeping surfaces free from dust, grease, and moisture.
Consider the following maintenance tasks:
- Regular calibration of machines
- Checking and replacing worn-out parts
- Cleaning workspaces after each project
Establishing a routine maintenance schedule is a practical approach. This not only extends the life of equipment but also enhances the overall welding performance.
Proper Technique and Training
Successful aluminium welding hinges on both technique and the skill level of the welder. Proper training ensures that welders understand the characteristics of aluminium. Knowledge of specific welding techniques for this material is vital. For instance, the handling of heat input and understanding thermal expansion should be part of training curricula.
It's essential to incorporate ongoing education into the professional development of welders. This can be achieved through:
- Workshops on advanced welding techniques
- Seminars focusing on specific issues related to aluminium welding
- Hands-on practice sessions that simulate real-world conditions
The right technique not only leads to stronger joints but also minimizes the chances of defects. Therefore, investing in skilled training is as important as maintaining equipment.
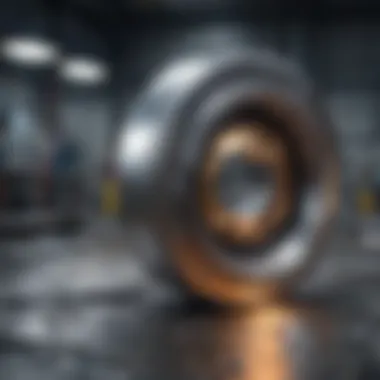
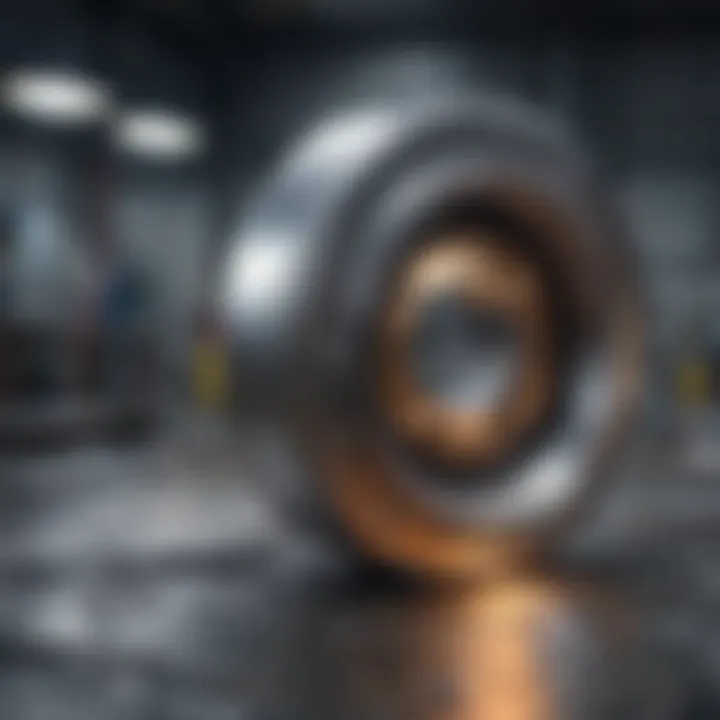
"Preventive measures are not just about avoiding defects; they are about ensuring quality throughout the production process."
Applications of Aluminium Welding Across Industries
Aluminium welding plays a crucial role in various sectors due to its lightweight and strength. The demand for aluminium welded components is rising. This trend is fueled by the need for efficiency and innovation in manufacturing. Each industry applies these techniques based on specific requirements and challenges. Understanding these applications helps in appreciating the relevance of aluminium welding in modern engineering.
Aerospace Industry
The aerospace sector is a leading player in the aluminium welding arena. Aluminium's properties contribute significantly to reduced weight and increased fuel efficiency in aircraft.
Key reasons for its importance in aerospace include:
- Weight Reduction: Aluminium structures are lighter, which improves fuel efficiency and payload capacity.
- Strength-to-Weight Ratio: Aluminium alloys possess high strength while remaining lightweight, ideal for aircraft components.
- Corrosion Resistance: This is vital for durability in harsh environments at high altitudes.
Aircraft manufacturers often rely on techniques such as Gas Metal Arc Welding and TIG for producing components that must endure extreme conditions. The aerospace industry continuously innovates to enhance performance, and aluminium welding is at the forefront of these advancements.
Automotive Sector
The automotive industry also benefits from aluminium welding. As vehicle designs evolve, there's an increasing focus on lightweight materials to improve efficiency and emissions standards.
Applications of aluminium welding in this sector involve:
- Lightweight Construction: Using aluminium aids in reducing the overall vehicle weight, which in turn enhances fuel efficiency.
- Recyclability: Aluminium is easily recyclable, making it a sustainable choice in modern automotive design.
- Crash Safety: Certain aluminium alloys provide excellent crash performance, essential for safety standards.
The use of MIG and TIG welding techniques is prevalent in automotive manufacturing. For example, the manufacturing of chassis and body panels incorporates these techniques extensively, showcasing their advantages in production processes.
Construction and Infrastructure
In construction, aluminium welding is commonly used for various structural frameworks, facades, and roofing. The lightweight nature and corrosion resistance of aluminium make it ideal for diverse applications.
Benefits of using aluminium welding include:
- Durability: Structures maintained with aluminium exhibit longer life spans due to their resistance to environmental degradation.
- Aesthetic Appeal: Aluminium can be finished in multiple ways, contributing to the overall aesthetic of buildings and bridges.
- Versatility: Aluminium can be easily extruded into different shapes, allowing for flexible architectural designs.
Moreover, the techniques employed in welding allow for quick assembly on job sites, reducing labor time and costs.
Marine Applications
The marine sector increasingly utilizes aluminium welding for boats and ships. The need for lightweight yet strong materials is critical for performance in water.
Highlights of aluminium usage in the marine industry:
- Weight Efficiency: Boats constructed with aluminium benefit from improved speed and maneuverability compared to heavier steel counterparts.
- Resistance to Corrosion: Aluminium is inherently resistant to seawater corrosion, making it ideal for marine environments.
- Repair and Maintenance: Welding techniques allow for easy repair, ensuring longevity of marine vessels.
Techniques like TIG welding are frequently used to fabricate hulls and other critical components, providing reliability and strength essential in marine applications.
"Aluminium’s unique properties and welding techniques make it an essential material across industries, driving innovation and efficiency."
In summary, aluminium welding serves vital functions in aerospace, automotive, construction, and marine industries. The ongoing advancement in these techniques continues to enhance the scope and capability of aluminium components in various applications.
Future Trends in Aluminium Welding
Understanding the future trends in aluminium welding is crucial for both academia and industry. This section will analyze how emerging technologies and sustainability considerations are shaping the field. These trends not only promise to improve efficiency but also to enhance the quality of welds and reduce the environmental impact of welding practices.
Advancements in Technology
As industries evolve, new technologies in aluminium welding are emerging. These advancements provide solutions that address current challenges and optimize processes. For instance, automated welding systems are gaining traction, enabling precision and consistency in welds, essential for complicated geometries commonly found in modern designs.
One notable technology is laser beam welding. This method utilizes a high-intensity laser to melt the aluminium, resulting in minimal heat input. Consequently, it reduces distortion and enables welding of thin materials without compromising structural integrity. Other technologies such as robotic welding systems are also becoming prevalent, enhancing accuracy and speed while minimizing human error.
Additionally, hybrid welding techniques that combine different methods, like laser and arc welding, are gaining attention. These techniques provide the benefits of both processes and can increase productivity significantly.
"Technological advancements are enabling aluminium welding to achieve higher standards in precision and efficiency, reshaping manufacturing processes across sectors."
Companies pursuing these advancements can expect better product quality, decreased production costs, and greater competitiveness in the market.
Sustainability Considerations
Sustainability is becoming a priority in aluminium welding. As industries confront the realities of climate change, the need for environmentally friendly practices is more pressing than ever. Companies are looking to reduce waste and energy consumption during the welding process.
Aluminium recycling is one of the significant sustainability focuses. Due to the metal’s extensive recyclability, initiatives are springing up to encourage the recycling of scrap aluminium from welding operations. This practice not only conserves resources but also minimizes energy expenditure compared to sourcing new aluminium.
Moreover, using welding materials and processes that have lower environmental impacts is gaining popularity. For instance, selecting fillers that produce fewer emissions can contribute to a cleaner work environment. Employers are also implementing energy-efficient equipment to further decrease their carbon footprint during production.
End
The conclusion serves as a critical element in encapsulating the insights gained throughout this article regarding aluminium welding. It synthesizes a broad spectrum of knowledge regarding the techniques and applications of aluminium welding, emphasizing the importance of this process in contemporary manufacturing and engineering.
In summary, aluminium welding not only enhances structural integrity but also contributes to the lightweight nature of various products, which is a key advantage in multiple industries. The overall efficiency of welding processes influences both productivity and cost-effectiveness, highlighting the need for continual advancements in technology.
The exploration of common defects and their preventive measures illustrates the complexity of aluminium welding. Knowing these can lead to improved quality and reliability in finished components.
"Understanding the nuances of aluminium welding is crucial for advancing engineering practices around the world."
Summary of Key Points
- Aluminium offers a lightweight yet strong material option for various applications.
- Each welding technique—GMAW, TIG, MIG, resistance welding, and FSW—has its unique benefits and use cases.
- Challenges such as contamination and thermal expansion must be addressed to achieve high-quality welds.
- The choice of alloy significantly affects weldability.
- Defects can be minimized through proper training and maintenance of work environments.
- Aluminium welding plays a vital role in industries such as aerospace, automotive, construction, and marine.
Final Thoughts on the Importance of Aluminium Welding
Aluminium welding is fundamental to innovation in modern engineering. As industries strive for lighter and more durable materials, the role of aluminium cannot be overstated. Awareness of the welding techniques and considerations involved allows professionals to push the boundaries of design and functionality. The continuous development in this field will propel many applications forward, ensuring that aluminium remains a material of choice for engineers across disciplines.