Advancements in Carbon Coating on Metals
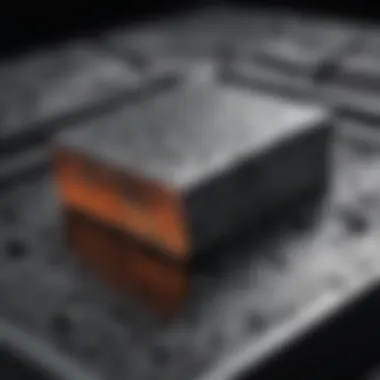
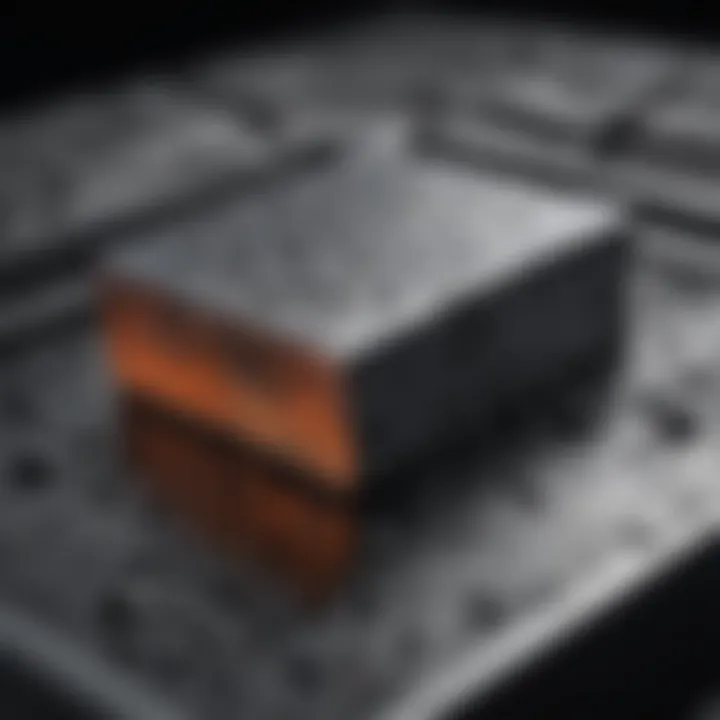
Research Overview
Carbon coating technology evolves as a pivotal process in metallurgy and materials science. Understanding its applications and techniques requires a comprehensive exploration of its underlying principles and methodologies. Carbon coatings, primarily composed of carbon atoms, enhance the mechanical properties and corrosion resistance of metals. This overview provides a framework to grasp these concepts, connecting theory with practical applications.
Methodological Approaches
The methods used for applying carbon coatings vary widely. Common techniques include physical vapor deposition (PVD) and chemical vapor deposition (CVD). Each method yields different outcomes based on the specific conditions under which the coating is applied. In PVD, the material transitions from a solid to a vapor state before being deposited on the substrate. Conversely, CVD involves chemical reactions that deposit a solid layer from gaseous precursors. The choice of technique hinges on the desired properties of the coating and the nature of the base metal.
Research indicates that varying the parameters in these methods can lead to significantly different structural characteristics. For example, alterations in temperature and pressure during CVD can influence the uniformity and thickness of the carbon layer. Such meticulous control ensures that the resulting coatings meet industry specifications tailored for distinct applications, from cutting tools in aerospace to decorative finishes in consumer products.
Significance and Implications
The implications of efficient carbon coating are profound. Enhanced wear resistance and improved surface hardness are only a few advantages that such coatings confer on metals. In application, industries such as automotive, aerospace, and manufacturing stand to benefit immensely.
"Carbon coatings not only increase longevity of components but also play a crucial role in reducing maintenance costs across various sectors."
Investing in carbon coating technologies can reduce overall energy consumption. Additionally, the environmental impacts are worth noting, as these coatings can minimize waste and promote sustainability in metal fabrication processes. Transitioning toward advanced coating methods paves the way for innovative developments in metallurgical applications.
Current Trends in Science
The science surrounding carbon coatings is continuously evolving, driving forward the development of new materials and techniques. Today, researchers are exploring advantages in nanotechnology and nanostructured coatings to achieve unprecedented performance characteristics in metals.
Innovative Techniques and Tools
Awareness of emerging nanomaterials escalates due to their performance advantages over traditional bulk materials. Techniques such as atomic layer deposition (ALD) introduce a new paradigm in producing thin and uniform coatings at the atomic scale. With tools becoming more sophisticated, precision in surface modification is no longer a distant goal. Moreover, advancements in real-time monitoring techniques enhance control over deposition processes, further refining the quality of the coatings produced.
Interdisciplinary Connections
Carbon coating research intersects various fields like physics, chemistry, and engineering. Collaboration among these disciplines fosters innovation. For instance, combining insights from materials science and mechanical engineering can lead to novel applications in constructing more resilient components in harsh environments. As industries increasingly demand high-performance materials, the warming relationship between carbon coating technologies and interdisciplinary research will undoubtedly cultivate new possibilities.
Such connections underscore the necessity for rigorous academic inquiry and industry feedback. Their synergy is essential for pushing boundaries and achieving groundbreaking results in carbon coating applications.
Foreword to Carbon Coating
Carbon coating has gained significant attention in recent years, primarily due to its applicability across various industries. As a process, it enhances the properties of metals, making them more suitable for demanding environments. There is a growing need for advanced materials that can withstand stressors like heat, corrosion, and wear. This section aims to delve into the fundamentals of carbon coating, highlighting its definition and importance, as well as providing a comprehensive historical background to understand its evolution.
Definition and Importance
Carbon coating refers to the application of a layer of carbon material onto metal substrates. This process aims to modify the surface characteristics, thereby improving the overall performance of the material. The carbon coatings can vary in thickness, composition, and structure, depending on the specific application.
The importance of carbon coating lies in its ability to significantly enhance the physical and chemical properties of metals. For instance, carbon coatings can improve hardness, wear resistance, and thermal stability. This makes them desirable in sectors such as automotive, aerospace, and electronics, where durability is critical.
Furthermore, the environmental aspect cannot be overlooked. Carbon coatings can serve as a barrier, protecting metals from corrosion, which prolongs the lifespan of components and reduces maintenance costs.
"Carbon coatings are becoming essential in modern engineering, representing a vital step towards more sustainable material usage."
Historical Background
The use of carbon as a coating agent can be traced back several decades. Initially, methods such as flame spraying and traditional painting included carbon materials, but these lacked the controlled environment necessary for effective bonding.
The introduction of Chemical Vapor Deposition (CVD) in the 20th century marked a major turning point. This technique allowed for better control over the deposition process, leading to more uniform and adherent coatings. Over the years, advancements in technology have enabled the development of more sophisticated methods, such as Physical Vapor Deposition (PVD) and electrochemical coating techniques.
These advancements reflect a growing understanding of material science and the importance of tailoring coatings to meet specific operational demands. As industries continue to evolve, the role of carbon coatings is likely to expand even further, setting the stage for innovative applications and research.
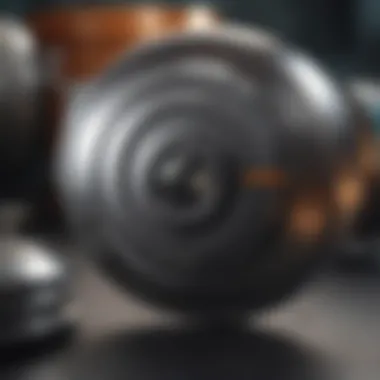
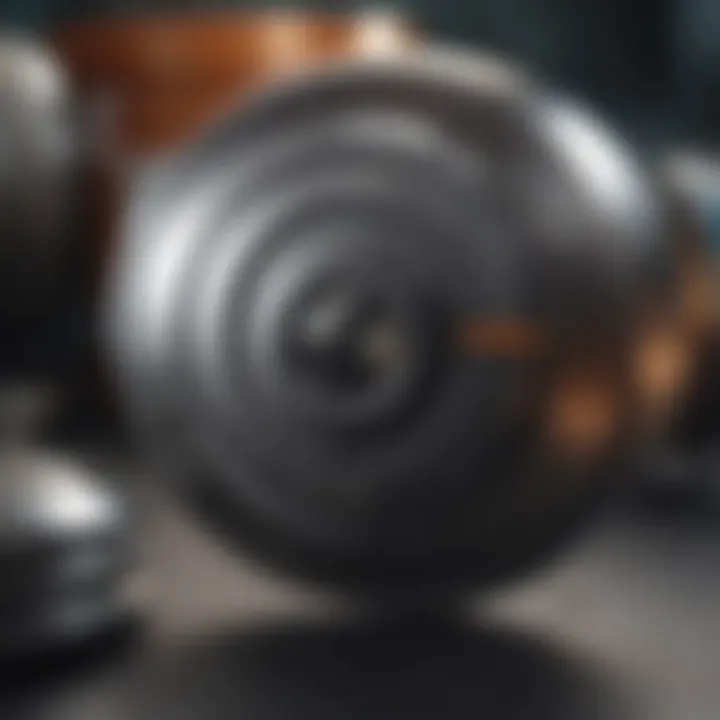
Chemical and Physical Properties of Carbon Coatings
Understanding the chemical and physical properties of carbon coatings is crucial for appreciating their role in modern materials science. The performance and longevity of metal components can drastically improve through careful manipulation of these properties. This section will explore several significant characteristics, detailing how these attributes impact the wider application of carbon coatings across various industries.
Structural Characteristics
The structure of carbon coatings plays a pivotal role in their effectiveness. Carbon can exist in various allotropes, such as graphite, graphene, and amorphous carbon. Each form presents unique structural features that influence the coating's density, porosity, and crystallinity.
- Graphene-Based Coatings: These coatings tend to have superior mechanical strength and electrical conductivity due to their two-dimensional structure. The arrangement of carbon atoms in a lattice allows for exceptional structural integrity.
- Amorphous Carbon: This type offers a more random atomic arrangement, generally enhancing wear resistance and reducing friction. Its lack of long-range order makes it suitable for applications requiring uniform coverage on complex geometries.
In addition to structural components, the adhesion quality of carbon coatings to the substrate material is important. It directly affects durability and performance, impacting wear and fatigue resistance during service.
Mechanical Properties
Mechanical attributes are paramount when assessing the suitability of carbon coatings for various applications. Key mechanical properties include hardness, toughness, and wear resistance.
- Hardness: Typically, carbon coatings exhibit high hardness levels, making them ideal for protecting metal surfaces against abrasive wear. For instance, diamond-like carbon (DLC) coatings are often utilized in automotive and aerospace applications due to their remarkable hardness.
- Toughness: Some carbon coatings maintain good toughness while having high hardness, an essential balance for many engineering solutions. This quality prevents cracking under stress.
- Wear Resistance: The ability of a carbon coating to withstand wear is heavily depended on its microstructure. Enhanced wear resistance leads to longer component life and reduced maintenance costs.
Thermal and Electrical Conductivity
The thermal and electrical conductivity of carbon coatings also warrants careful examination, especially in fields where thermal management and electrical performance are critical.
- Thermal Conductivity: Certain carbon coatings, such as those made of graphene, exhibit excellent thermal conductivity, enabling efficient heat dissipation. This property is critical in electronics, where overheating can significantly reduce performance and lifespan.
- Electrical Conductivity: Carbon coatings can be tailored to exhibit varying levels of electrical conductivity. This versatility allows for widespread use in electronic applications, from conductive pathways on circuit boards to advanced sensors.
"The unique properties of carbon enable it to fulfill diverse roles in engineering and manufacturing, offering solutions to complex challenges in material performance and longevity."
Methods of Applying Carbon Coatings
The application of carbon coatings on metals involves several methods that each have their unique advantages and limitations. Understanding these methods is essential, as they define the quality, performance, and applicability of the coating. The techniques discussed here include Chemical Vapor Deposition, Physical Vapor Deposition, and Electrochemical Coating. Each method contributes to enhancing material properties, providing wear resistance, and improving performance across various industries.
Chemical Vapor Deposition ()
Process Overview
Chemical Vapor Deposition, or CVD, is a widely used method for creating thin films of carbon on metal surfaces. The process requires gaseous precursors that decompose on the substrate, leading to the formation of a solid carbon layer. One key characteristic of CVD is its ability to produce uniform and conformal coatings, even on complex geometries. CVD is a popular choice due to its ability to achieve precise control over coating thickness and film quality. The method's capacity for high deposition rates and suitability for large substrates makes it advantageous for various applications. However, the need for high temperatures can limit the types of metals that are compatible with CVD.
Advantages and Limitations
CVD offers significant advantages, including excellent adhesion between the coating and substrate. This contributes to enhanced mechanical properties and extended service life. CVD can also enable the deposition of various carbon forms, like diamonds and amorphous carbon. However, the process has certain limitations, including the complexity of equipment and the need for rigorous safety measures due to hazardous gases involved. Cost considerations also play a role in the choice of CVD compared to other methods.
Physical Vapor Deposition (PVD)
Technique Description
Physical Vapor Deposition, or PVD, encompasses a range of vacuum-based techniques to apply carbon coatings. PVD works on the principle of vaporizing a solid or liquid source material, which then condenses onto the substrate. A notable aspect of this technique is its versatility, which allows for various forms of carbon to be deposited, including graphene and hard carbon films. PVD is beneficial as it typically operates at lower temperatures than CVD, making it suitable for a wider range of metal substrates.
Applications in Industry
PVD is employed extensively in industries such as aerospace and electronics. In aerospace, coatings applied via PVD improve wear resistance and reduce drag, enhancing performance. In the electronics field, PVD coatings enable miniaturization while maintaining electrical properties. The technique’s ability to create precise and uniform coatings makes it popular; however, the thickness of the coating may be less than what can be achieved with CVD. Increasing the production cost per square meter is another aspect that must be considered when choosing PVD.
Electrochemical Coating
Basic Principles
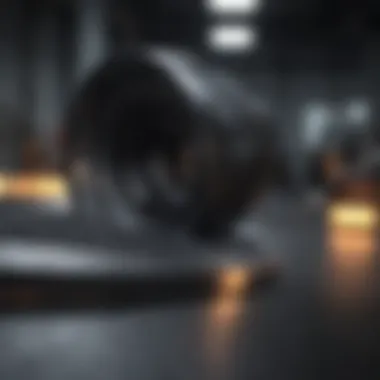
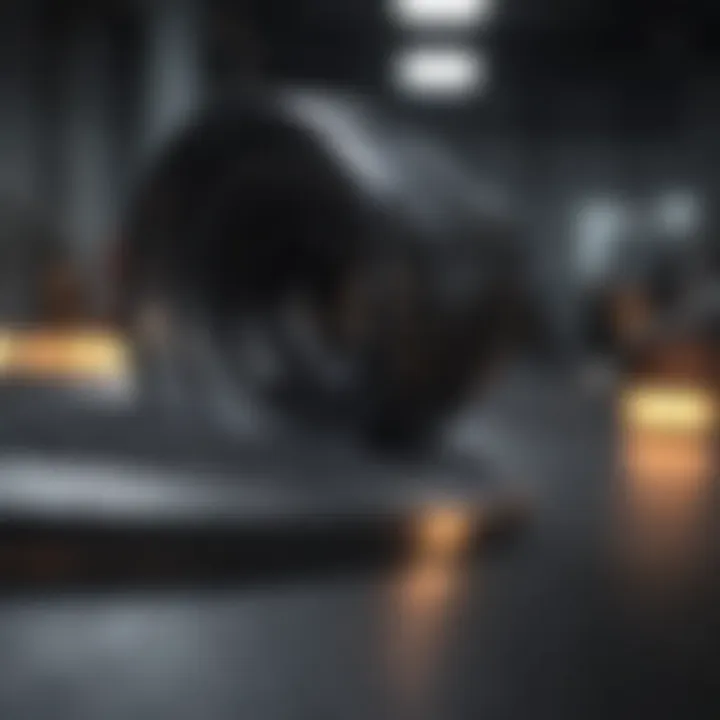
Electrochemical Coating is a process that uses electrical current to deposit a layer of carbon onto a metal substrate. This method involves immersing the metal in an electrolyte solution containing carbon. The unique feature of this approach is its lower energy requirements compared to CVD and PVD. Electrochemical Coating allows for the control of layer thickness and uniformity. It is particularly effective for complex shapes and intricate designs, which provides an edge over traditional methods.
Process Parameters
Controlling process parameters, such as current density, temperature, and bath composition, is vital for the success of Electrochemical Coating. These elements directly influence the quality and characteristics of the resulting layer. Adequate management of these parameters can lead to better adhesion and improved performance of the coatings. While the method is generally consistent, variations in process control can lead to inconsistencies in coating properties. Considering these factors is crucial for achieving desired outcomes in applications.
The choice of coating method is critical as it influences both the effectiveness and applicability of carbon coatings in diverse industrial fields.
Application Areas of Carbon Coatings
Understanding the various application areas of carbon coatings is essential when discussing their significance in enhancing metal performance. This section will elaborate on the different industries that benefit from carbon coatings, highlighting specific advantages tied to their applications. Carbon coatings play a vital role in improving durability, wear resistance, and functionality across diverse fields, making them invaluable in today's technological landscape.
Automotive Industry
Engine Components
Engine components are critical elements in any vehicle, playing a crucial role in operational efficiency. The application of carbon coatings on these parts has shown promising results in enhancing performance. Carbon coatings can withstand high temperatures and pressures, which are common in engine environments. This high strength enables these parts to maintain structural integrity, thus prolonging their lifespan. The unique feature of these coatings is their ability to reduce friction. By reducing wear, vehicles can operate more efficiently, which in turn leads to better fuel economy. This characteristic renders carbon coatings a popular choice among manufacturers aiming to increase performance while also considering environmental impacts through reduced emissions.
Wear Resistance
Wear resistance is another significant aspect of carbon coatings, especially in the automotive sector. Coatings designed for this purpose enhance the longevity of components exposed to friction and stress. The remarkable durability of these coatings can minimize the frequency of part replacements, ultimately leading to cost savings for both manufacturers and consumers. Additionally, the ability of carbon coatings to resist abrasive actions is a distinct advantage, ensuring that critical components such as gears and axles function optimally. This aspect of carbon coatings contributes positively to an overall decrease in maintenance costs, making them a beneficial addition in automotive applications.
Aerospace Engineering
Lightweight Structures
In aerospace engineering, the importance of lightweight structures cannot be overstated. Carbon coatings are pivotal in achieving desired weight reductions without compromising strength. The unique lightweight characteristic of carbon coatings allows for enhanced fuel efficiency and improved payload capacities in aircraft. This application is not only beneficial for performance but also addresses increasing demands for energy-efficient operations in the aviation sector. Such attributes underscore the necessity of incorporating carbon coatings in flight structures.
Corrosion Protection
Corrosion protection is another area where carbon coatings excel in aerospace applications. Airborne components are susceptible to environmental factors that can lead to degradation. Applying carbon coatings offers resistance against corrosion, which is essential for maintaining the longevity and safety of aircraft. These unique coatings effectively shield metal surfaces, contributing to reduced maintenance and repair costs. As a result, this functionality can extend the operational life of aircraft components significantly.
Biomedical Applications
Implant Coatings
In the biomedical sector, implant coatings using carbon technology have gained traction. These coatings are specifically engineered to enhance biocompatibility, allowing them to integrate better with human tissue. The essential characteristic of these coatings is their ability to promote osseointegration, which is critical for the stability of implants. This application is significant because it can lead to better patient outcomes and lower chances of complications post-surgery. The unique feature of implant coatings is their customization potential, allowing for tailored solutions for different types of implants, which brings additional benefits in functionality and safety.
Antimicrobial Properties
Carbon coatings also showcase impressive antimicrobial properties, making them suitable for various biomedical applications. The ability to inhibit microbial growth is vital in surgical environments, as it reduces the risk of infections. This characteristic of carbon coatings can be crucial for medical devices and implants, promoting better health outcomes. However, while the potential for infection reduction is notable, it is important to evaluate the long-term effects and safety of these properties in medical contexts.
Electronics and Optoelectronics
Conductive Coatings
Within the electronics industry, conductive coatings made from carbon materials are gaining attention. These coatings facilitate electrical conductivity, which is essential in many devices. The key characteristic of conductive carbon coatings is their ability to maintain conductivity while being lightweight and flexible. This makes them an increasingly preferred choice in the production of various electronic components, including sensors and flexible circuits. However, the balance between cost and performance remains a consideration for manufacturers in this space.
Photovoltaic Applications
Carbon coatings have also found their way into photovoltaic applications, primarily in solar cells. Their unique ability to enhance light absorption plays a crucial role in improving the efficiency of solar energy systems. This contributes to greater sustainability efforts, promoting the use of renewable energy. Nonetheless, it is essential to assess the efficiency and durability of carbon-coated solar cells over time to ensure they meet market demands.
As the demand for carbon coatings continues to rise, their applications in various industries illustrate the versatility and necessity of this technology in modern engineering.
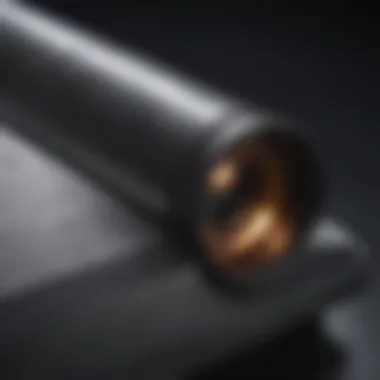
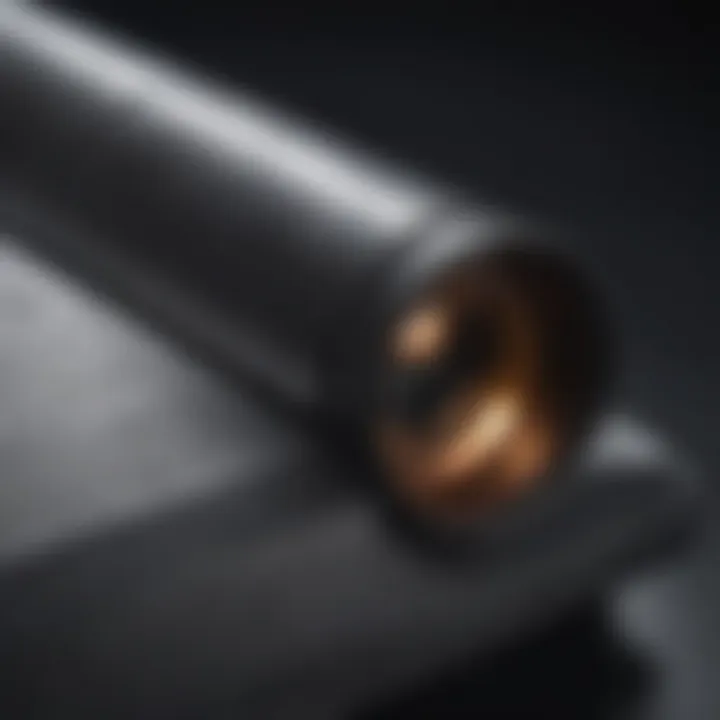
Challenges and Limitations
Understanding the challenges and limitations of carbon coating on metals is essential to fully appreciate the technology's impact on various industries. While carbon coatings offer extensive benefits such as wear resistance and improved durability, several factors can hinder their effectiveness. These challenges often arise during the application process, the financial implications of coating technology, and the environmental impacts associated with certain methods.
Adhesion Issues
Adhesion strength is a critical aspect when it comes to the performance of carbon coatings. If the coating does not adhere well to the substrate, it can lead to premature failure. The mechanism of adhesion involves the interaction between the coating and the metal surface. Various factors influence this process, including surface roughness, contamination, and chemical composition of the substrate. Techniques such as plasma treatment or surface roughening may enhance adhesion but can introduce additional complexity into manufacturing. Poor adhesion can result in delamination or chipping, both of which compromise the longevity and effectiveness of the coating.
Cost Considerations
The financial aspect of implementing carbon coating technologies cannot be overlooked. While the benefits are significant, the initial setup costs for applying carbon coatings, particularly methods like Chemical Vapor Deposition (CVD) and Physical Vapor Deposition (PVD), can be high. Equipment and maintenance expenses can deter some organizations from adopting these processes. Additionally, specialized training for personnel adds another layer of cost. Yet, these initial investments should be viewed in light of the long-term savings associated with improved product lifespan and performance. To mitigate costs, companies may need to evaluate whether the benefits justify the expenses and explore alternative coating techniques that are more cost-effective.
Environmental and Health Concerns
Carbon coating processes can pose environmental and health concerns that deserve attention. Certain deposition techniques release harmful byproducts, which can have detrimental effects on surrounding ecosystems. Furthermore, the handling of materials used in coatings must comply with rigorous safety standards to protect workers. Adequate ventilation and protective gear are essential during the application of coatings to minimize health risks. As industries move towards more sustainable practices, researchers are exploring greener materials and techniques, aiming to reduce the environmental footprint of carbon coating processes.
In summary, while carbon coatings bring numerous advantages, it is vital to acknowledge and address the associated challenges and limitations. Addressing adhesion issues, managing costs effectively, and keeping environmental and health concerns in mind will help industries to optimize the use of carbon coatings successfully.
Emerging Trends in Carbon Coating
The landscape of carbon coating technology is witnessing significant advancements. These emerging trends are reshaping how industries apply carbon coatings to metals, pushing the boundaries of their applicability and functionality. By focusing on novel approaches, material development, and innovative applications, these trends promise to enhance the efficiency, durability, and sustainability of coated products in numerous fields.
Nanostructured Coatings
Nanostructured coatings have gained attention for their unique properties and enhanced performance. The modification of carbon coatings at the nanoscale allows for improved mechanical strength and reduced weight. These coatings often exhibit superior wear resistance, making them suitable for demanding applications in aerospace and automotive industries. Furthermore, the high surface area provided by nanostructuring improves adhesion and enhances the effectiveness of the coating.
Key benefits include:
- Enhanced mechanical properties: Increased hardness and elastic modulus.
- Improved corrosion resistance: Protects substrates in harsh environments.
- Tailored surface functionalities: Can be engineered for specific applications, such as hydrophobic or oleophobic surface characteristics.
Biocompatible Coatings
Biocompatible coatings represent a critical area of research, especially in the biomedical field. These coatings are designed to interact safely with biological systems, which is essential for devices such as implants or prosthetics. Carbon-based materials, like graphene oxide or diamond-like carbon, have been explored due to their favorable properties such as biocompatibility, which minimizes adverse responses once implanted in human tissue.
Important aspects of biocompatible coatings include:
- Reduced inflammatory response: Promotes healing and acceptance in the host body.
- Enhanced integration: Increases bone or tissue integration with implants, improving overall stability.
- Antimicrobial properties: Some carbon coatings can reduce infection risks, crucial for surgical applications.
Smart Coatings
The evolution of smart coatings integrates multifunctional capabilities into carbon coatings. These smart coatings can respond to environmental stimuli such as changes in temperature, pH, or moisture levels. For instance, they may release biocides in response to bacterial presence on surfaces or change color to indicate corrosion.
Attributes of smart coatings include:
- Active monitoring: Provide real-time data on the condition of the substrate.
- Environmental responsiveness: Adapt properties in real-time, improving functionality.
- Self-healing abilities: Some smart coatings can repair damage autonomously, prolonging the life of the coated material.
End
The conclusion of this article encapsulates critical elements of carbon coating on metal, emphasizing its irreplaceable role in enhancing material performance across various industries. As we explore the diverse applications of carbon coatings, it becomes evident that their significance stretches beyond mere protection. They contribute to improved durability, wear resistance, and even optimize thermal and electrical efficiency in complex systems.
Summary of Key Points
In summary, carbon coating presents several advantages worth reiterating:
- Enhanced Durability: Carbon coatings create a protective barrier against wear and corrosion, ensuring longer lifespans for metal components. This is particularly vital in industries like automotive and aerospace, where performance and reliability are paramount.
- Versatile Applications: The adaptability of carbon coatings allows their use in various sectors including biomedical, electronics, and optoelectronics. Each application harnesses distinct properties of the coatings to meet specific demands.
- Advanced Techniques: The methods for applying these coatings, such as Chemical Vapor Deposition and Physical Vapor Deposition, are fine-tuned to achieve optimizing results, demonstrating ongoing innovation in material science.
- Emerging Trends: The movement toward nanostructured and biocompatible coatings illustrates the field's commitment to sustainability and health-conscious solutions, paving the way for future advancements.
Future Research Directions
Looking ahead, several research avenues present themselves:
- Sustainable Coating Solutions: Investigating environmentally friendly processes for creating carbon coatings could greatly enhance their adoption in sensitive applications. Developing methods that minimize hazardous waste or energy consumption is integral.
- New Composite Materials: Exploring combinations of carbon coatings with various substrates might yield superior qualities that traditional materials cannot achieve alone. The goal will be to enhance the functional properties while retaining structural integrity.
- Smart Coatings Development: Innovations are paving the framework for smart coatings that can change properties based on environmental conditions. Research can focus on integrating sensors or responsive chemicals within the coatings to extend their functionality.
- In-depth Characterization Techniques: Refining methodologies for understanding how these coatings behave under extreme conditions can lead to better prediction models. This will assist engineers and scientists in tailoring solutions for specific industrial challenges.