Exploring Ceramic Welding: Techniques and Innovations

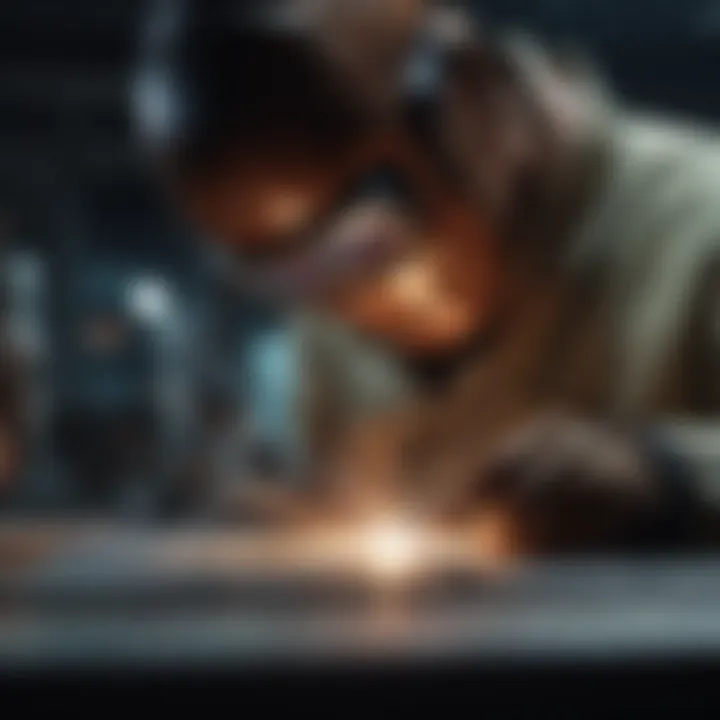
Intro
Ceramics have long been hailed for their remarkable properties, offering a unique blend of durability, thermal resistance, and aesthetic appeal. However, when it comes to welding these materials, the task becomes a different kettle of fish. The process of joining ceramics through welding techniques is an intricate venture that brings both challenges and innovations to the forefront of scientific inquiry.
Understanding the welding of ceramics involves not just a glance at techniques but a deep dive into the properties that make ceramics both valuable and difficult to manipulate. As industries evolve and the demand for advanced materials increases, the spotlight turns to ceramic welding as a frontier of technological advancement. From aerospace components needing high heat resistance to medical devices requiring biocompatibility, the applications of ceramic welding are vast and growing.
In this article, we will navigate through various aspects of ceramic welding, including the methods that professionals employ to achieve successful joints, the obstacles that they encounter, and the cutting-edge innovations that are shaping the future of this field.
Preface to Ceramic Welding
Ceramic welding is a fascinating branch of materials science that merges the complexities of ceramics with various welding techniques. Understanding this field is not just an academic pursuit; it carries significant implications for industrial applications, scientific advancements, and technological innovation. By exploring ceramic welding, one can appreciate the nuances of joining materials that are otherwise notorious for their rigidity and brittle nature.
Defining Ceramic Welding
Ceramic welding can be observed as the art and science of fusing ceramic materials through various techniques that maintain the integrity of the ceramics involved. Unlike traditional metal welding, which often involves melting the materials, ceramic welding typically employs processes that minimize heat to prevent damage. The essence of this technique lies in how it approaches the challenge of bonding two rigid structures without compromising their essential properties. For example, methods like laser welding or plasma arc welding are employed to create strong joints while addressing the inherent fragility of ceramics.
Historical Context
Historically, the welding of ceramics has been a lesser-explored territory compared to metals. The lack of significant technical development in ceramic welding processes can be traced back to the traditional belief that ceramics could not be welded effectively. Early attempts at ceramic bonding were often through adhesives or mechanical fastening. However, as the demand for advanced materials increased in sectors like aerospace and electronics, the focus began to shift. Innovative techniques emerged in the late 20th century, paving the way for a new era where ceramic welding can be performed with precision and reliability. The historical evolution reflects a growing recognition of the potential that ceramics hold in various applications, demanding new methods to harness these materials effectively.
Importance in Modern Applications
The significance of ceramic welding in contemporary industry cannot be understated. With the rapid advancement of technology, ceramics have found roles in high-performance applications that benefit from their unique properties. Here are some key areas where ceramic welding proves vital:
- Electronics: Ceramic components ensure electrical insulation and withstand high temperatures, making them fundamental in circuit boards and components.
- Aerospace: The stringent requirements for materials in aircraft and spacecraft mean that ceramics, often in the form of thermal barriers, require strong and durable welding solutions.
- Automotive: With the need for weight reduction without sacrificing strength or heat resistance, ceramics can be joined to metallic components, enhancing vehicle performance and efficiency.
In summary, understanding ceramic welding helps researchers and engineers tap into the vast potential of ceramics in modern applications.
As we dive deeper into this article, readers will gain insights into the diverse techniques available for ceramic welding, the challenges that practitioners face, and innovations that may define the future of the field.
Properties of Ceramics Impacting Welding
Ceramics may seem like a straightforward category when it comes to materials, but their unique properties significantly affect how they are welded. Understanding these aspects is essential for researchers and industries aiming to optimize ceramic welding techniques. The mechanical, thermal, and chemical properties of ceramics play a pivotal role in the success of welding processes. Each attribute can introduce specific challenges or advantages during welding, making it crucial for practitioners to adapt and tackle these characteristics effectively.
Mechanical Properties
When it comes to ceramics, mechanical properties are fundamental. Ceramics are known for their high hardness and brittleness. This means that while they can withstand substantial pressure, they break rather than deform under stress. These mechanical traits impact how ceramics can be welded together. High hardness often makes it challenging to achieve a solid bond without introducing microcracks.
- Tensile Strength: Ceramics generally exhibit high tensile strengths, which is a plus when in service. However, the high input of energy during welding might exceed the material's capacity, leading to cracks or fractures.
- Ductility: Most ceramics are not ductile, which implies that any misalignment or shift during the joinery process could result in joint failure.
These mechanical intricacies necessitate a strategic approach in welding methods to ensure a reliable bond. Itâs essential that the selected welding technique not only accommodates these properties but also enhances the integrity of the weld.
Thermal Properties
The thermal properties of ceramics are another critical aspect influencing their welding behaviors. Ceramics typically have a high melting point, which should be taken into consideration when applying heat. If the temperature rises too high, it can lead to unexpected melting or deformation, compromising the integrity of both the base material and the weld.
- Thermal Conductivity: Ceramics usually exhibit poor thermal conductivity, meaning that the heat may not distribute evenly during welding. This uneven distribution can create thermal gradients, which in turn lead to differential expansion rates. As a result, residual stresses and cracks can develop as the weld cools and solidifies.
- Thermal Expansion: The difference in thermal expansion coefficients between different types of ceramics and between the ceramic material and any filler materials can also create stresses at the weld interface. Understanding and accommodating these variations is crucial for successful welds.
Chemical Stability
Chemical stability is yet another defining characteristic of ceramics that influences welding. Generally, ceramics exhibit excellent resistance to corrosion and chemical degradation. However, during the welding process, high temperatures can cause reactions between the ceramic materials and the environment or contaminants. This can degrade the quality of the weld.
- Oxidation: For instance, some ceramics may oxidize under extreme heat, leading to changes in their microstructure and mechanical properties. This fact requires careful control of the welding atmosphere to maintain the integrity of the material.
- Compatibility: Some ceramic materials are more chemically reactive than others and may require different welding techniques or protective atmospheres, such as inert gases, to prevent adverse reactions.
Understanding the properties of ceramics in relation to welding helps to navigate the complexities and employ suitable strategies to enhance welding performance. Addressing these factors can make a significant difference when it comes to designing effective ceramic joints.

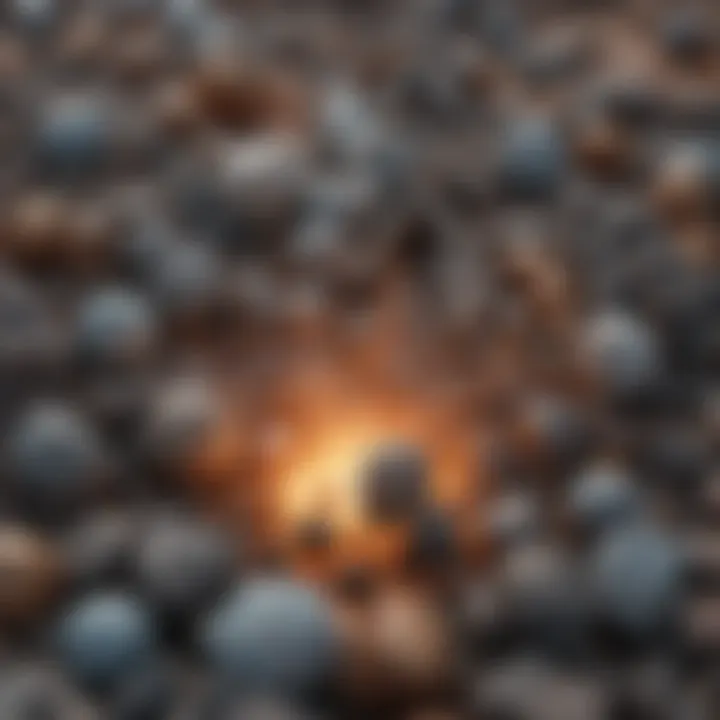
"In many ways, the success of ceramic welding hinges on how well one grasps the material properties at play. Knowing the quirks and benefits can set the stage for innovation in the field."
Professionals engaging with ceramics must, therefore, consider these mechanical, thermal, and chemical properties as they strategize their welding plans. This knowledge not only improves the quality of welds but also paves the way to more innovative applications in various industries.
Techniques in Ceramic Welding
When diving into ceramic welding, the techniques employed are not just methods but foundational elements that shape the potential of the material in various applications. Each technique comes with its benefits, considerations, and impacts on the overall quality of the weld. Understanding these techniques is vital for students, researchers, educators, and professionals alike who are looking to enhance the processes involved in welding ceramics and to innovate in this promising field.
Laser Welding
Laser welding has been making waves in the world of ceramics. Utilizing concentrated beams of light, this technique allows for precise control over the welding process. Simply put, it's like using a magnifying glass to focus sunlight on a particular spot. The process generates high temperatures, leading to rapid melting of the ceramic material at the focused area, which then solidifies to form a robust bond.
Benefits of laser welding include:
- Precision: The focused nature of the laser means that you can work with delicate materials that might otherwise fracture under traditional welding methods.
- Speed: This technique often requires less time than others, which can be a game changer in production settings.
- Less thermal input: Since the laser only affects a small area, it reduces the chances of thermal damage to the surrounding material.
However, it's not without challenges. The requirement for specialized equipment can limit access, particularly in smaller workshops. Moreover, achieving a consistent quality throughout the process can demand significant skill and experience. This points to the need for ongoing training and development in using laser welding effectively.
Plasma Arc Welding
Plasma arc welding stands out due to its versatility and effectiveness in dealing with ceramics. This method creates an electric arc between a tungsten electrode and the workpiece, forming a constricted plasma that reaches extremely high temperatures. Itâs a bit like a science experiment gone rightâwhere the combination of electricity and gas creates a mini-sun that melts materials at precision levels.
Key advantages of plasma arc welding include:
- Control over heat input: This is crucial when welding ceramics, as excessive heat can lead to unwanted structural changes.
- Capability to work with thick materials: Unlike some techniques that struggle with thickness, plasma arc welding holds its ground and can handle substantial ceramic pieces.
- Reduced risk of contamination: The process can be conducted in an inert gas environment, minimizing the potential for unwanted reactions.
On the flip side, learning how to master plasma arc welding does come with its own steep learning curve and requires significant investment in equipment. As with laser welding, there's a balance to strike between cost and capability, which can make it a point of consideration for those venturing into this field.
Adhesive Bonding
Adhesive bonding is sometimes overlooked in discussions around welding techniques for ceramics. In temperament, this method is different, resembling more of a high-stakes puzzle than traditional welding. It focuses on using specialized adhesives that can form strong bonds between ceramic surfaces without melting the materials themselves. Itâs the slow and steady approach that can yield impressive results.
Key points about adhesive bonding include:
- Flexibility: This technique can accommodate a range of ceramic types and properties, providing diverse options for bond strength.
- Reduced thermal distortion: By avoiding high heat, the risk of cracks and warps is significantly reduced, which is a boon for delicate components.
- Application versatility: Adhesive bonding can be used in conjunction with other methods, allowing for hybrid approaches.
Nevertheless, itâs essential to select the right adhesive for the job, as not all are created equal in terms of chemical compatibility and long-term durability. Also, the curing time can be longer compared to other welding methods, potentially affecting production timelines.
Other Emerging Techniques
The exploration of welding ceramics doesnât stop at these traditional methods. Researchers and engineers are continually looking for innovative techniques that could transform how ceramics are welded. For instance, methods like Friction Stir Welding (FSW) and Ultrasonic Welding have started gaining traction in niche applications. Both of these methods rely on mechanical energy rather than thermal energy, which can sometimes work wonders in minimizing issues related to thermal stresses and distortion.
Emerging techniques present various advantages:
- Friction Stir Welding: This method can create strong joints in materials without the need for molten states, proving particularly effective for joining different kinds of ceramics.
- Ultrasonic Welding: Known for its speed, this method is especially useful in applications requiring precise overlapping, often seen in the electronics sector.
Incorporating these newer methods into the ceramic welding toolkit could very well pave the way for future innovations, driving advancements that lead to stronger, more efficient products.
In summary, each technique in ceramic welding offers unique benefits and challenges, demanding careful analysis of both the material at hand and the desired outcome. As the industry continues to evolve, the ongoing refinement of these techniques will be vital for ensuring that ceramic welding can meet the requirements of tomorrow's technology.
Challenges in Ceramic Welding
Ceramic welding stands as an intricate discipline, intertwining the scientific with the practical. Itâs crucial to grasp the multifaceted challenges during the welding process, as these elements directly influence both the performance and reliability of the final product. Understanding these challenges helps in creating tailored solutions, driving innovation, and ensuring quality in ceramic applications. Without acknowledging potential issues, the applications of ceramic welding may stumble, leading to costly errors or failures.
Cracking and Delamination
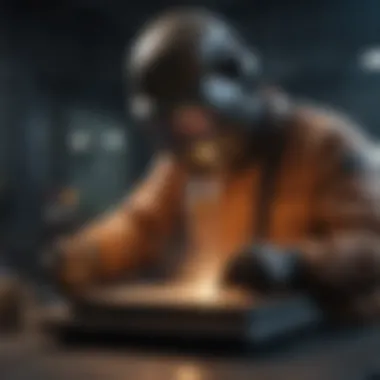
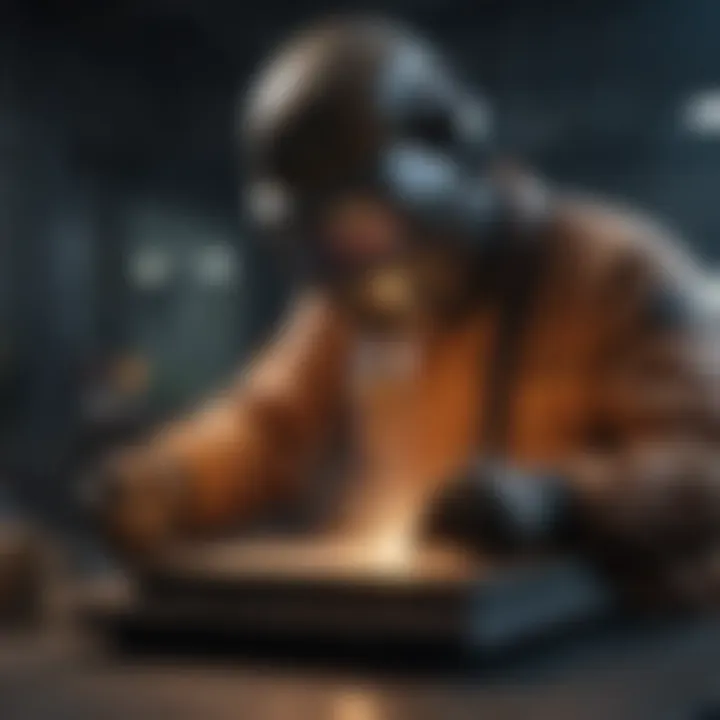
In the realm of ceramic welding, cracking and delamination are among the most significant adversaries. These phenomena usually stem from the inherent brittleness of ceramics. When subjected to thermal extremes or mechanical stresses, the structural integrity of the weld can falter.
- Microstructural Weakness: The process involves different materials with varied thermal expansion coefficients, exacerbating the likelihood of cracking.
- Environmental Factors: Humidity, temperature fluctuations, and even impurities during welding contribute to delamination. Addressing these elements is vital.
- Control Measures: Engineers and researchers keep exploring solutions, like adjusting welding speeds or developing more compatible materials, to mitigate these risks.
Through systematic approaches and a thorough understanding of materials, it is possible to fortify joints and minimize these issues.
Thermal Stress Management
When it comes to thermal stress, itâs a balancing act. The welding of ceramics can lead to rapid heating and cooling cycles. This thermal shock can create stress points within the material that can do more than just weaken a joint; it can cause complete failure over time.
- Gradual Heating/Cooling: Techniques like preheating the ceramic can alleviate sudden temperature changes, offering a more stable environment throughout the welding process.
- Insulation Strategies: Utilizing insulative barriers during welding can help control the heating rates, ultimately contributing to enhanced welding outcomes.
- Predictive Modeling: Computational models are also being employed to simulate thermal behavior in ceramics, allowing for proactive adjustments before issues arise.
Managing thermal stress isn't just a technical necessity; it is integral for improving the durability and lifecycle of ceramic products in various applications.
Joint Integrity and Reliability
Lastly, ensuring joint integrity and reliability is paramount in the world of ceramic welding. After all, a strong joint can mean the difference between success and failure in critical applications. The integrity of a joint not only relies on the welding technique but also on the materials chosen and the environmental conditions during and after welding.
- Quality Control: Routine inspections using methods like ultrasonic testing can help in gauging the health of the welds over time.
- Material Selection: Selecting compatible materials enhances joint reliability. Compatibilities in thermal properties and mechanical strengths play a vital role in creating robust joints.
- Standards and Protocols: Developing standardized procedures for welding ceramics aids in establishing benchmarks for quality and reproducibility.
Taking into account these considerations promotes a deeper strength in ceramic welding, which is indispensable in sectors such as aerospace, automotive, and electronics.
"In tackling the challenges of ceramic welding, we pave the way for innovation and progress, ensuring structures that excel both in strength and functionality."
The complexities in ceramic welding challenge us to think creatively, pushing the boundaries of what can be achieved. Here, the journey of overcoming obstacles leads to breakthroughs that can transform industrial practices.
Applications of Ceramic Welding
The application of ceramic welding holds immense significance in various industrial sectors due to its unique properties and capabilities. With ceramics known for their rigidity, heat resistance, and electrical insulation, the demands for their use in specialized applications are considerable. Understanding where and how ceramic welding can be utilized not only speaks to its technical advantages but also illuminates how it enhances performance across different fields.
Electronics and Insulation
In the realm of electronics, ceramic welding serves as an indispensable technique. The ability of ceramics to withstand high temperatures and provide excellent electrical insulation makes them ideal for various applications. For instance, these materials are often employed in insulators used in high-voltage systems. The welding process ensures that components maintain their structural integrity while also adhering to stringent electrical standards. Moreover, soldering ceramics in electronic devices like capacitors and resistors can lead to improved efficiency and longevity of these components.
- Key Benefits:
- High dielectric strength ensures reliable electrical performance.
- Resistance to thermal and mechanical stresses enhances durability.
- Variety of ceramic materials leads to diverse applications in insulating and conducting roles.
Aerospace and Defense
Ceramic welding takes on a crucial role in the aerospace and defense sectors. The demands for lightweight yet robust materials in aircraft and spacecraft have driven innovation in ceramic welding techniques. Advanced ceramics, combined with welding processes, facilitate the creation of components that can endure extreme conditions. For example, gas turbine engines incorporate ceramic components to improve their efficiency and reduce weight. The ability to weld ceramics in these applications leads to enhanced safety and performance, which are non-negotiable in aerospace engineering.
"The integration of ceramic materials achieves a fine balance between lightweight construction and high strength, pivotal for any aerospace mission."
Common Uses in Aerospace:
- Engine components such as combustion chamber liners.
- Heat shields that protect spacecraft during re-entry.
- Sensors and navigational aids requiring precise material characteristics.
Automotive Industry
The automotive sector is another area where ceramic welding proficiency proves valuable. With the rise in demand for lightweight yet strong materials to promote fuel efficiency, ceramics have become essential. Applications include exhaust systems, brake pads, and various engine components. The welding of ceramics contributes to better resistance against wear and high temperatures, thus enhancing overall vehicle performance. Moreover, the use of ceramics in automotive applications reflects a broader trend towards sustainable engineering practices, as they often exhibit lower environmental impacts compared to traditional materials.
- Highlights of Benefits in the Automotive Sector:
- Reduced weight of components leads to improved fuel efficiency.
- Enhanced performance of high-temperature parts extends service life.
- Innovative designs foster a move towards greener manufacturing practices.
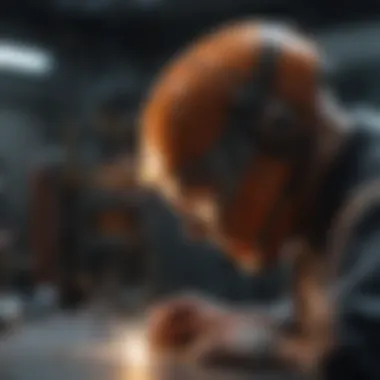
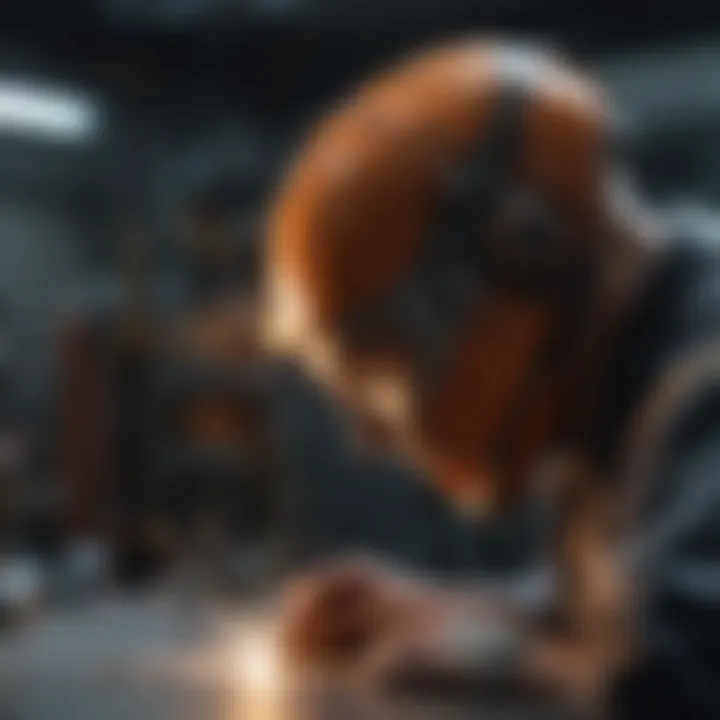
Recent Innovations in Ceramic Welding
Recent innovations in ceramic welding signify a pivotal advancement in the field, demonstrating how technology continues to shape material processing. As industries progress, so do the challenges of working with ceramics due to their inherent properties and susceptibilities. Innovations not only enhance the versatility and applicability of ceramic materials but also address significant hurdles by offering improved techniques and materials. In this section, we dive into two notable areas: recent advancements in materials and the emergence of new welding techniques.
Advancements in Materials
The progression of material science has paved the way for new compounds and composites that facilitate more robust ceramic welding. Innovative materials, like zirconia-toughened alumina, exhibit higher fracture toughness and thermal stability, making them ideal for high-stress applications. This has allowed manufacturers to bridge the gap between traditional ceramics and more ductile alternatives.
Also, advancements in nanomaterials are crucial. By integrating nano-scale particles into ceramic matrices, manufacturers create materials with excellent thermal and mechanical properties. This technique not only improves the bonding compatibility in welding processes but also elevates the overall reliability of end products. Here are some key advancements:
- Modified Ceramics: New formulations have been developed to enhance thermal and chemical resistance, making them suitable for extreme environments.
- Composite Innovations: The combination of different ceramic materials broadens the application range, notably in high-performance industries like aerospace.
- Sintering Techniques: Enhanced sintering methods help create more uniform microstructures, leading to consistent quality in welds.
These advancements have the potential to significantly reduce production costs and improve product longevity, making innovations in materials a cornerstone of progress in ceramic welding.
Development of New Techniques
The evolution of fabrication techniques is another vital area of innovation within ceramic welding. Traditionally, methods like adhesive bonding faced limitations in performance and durability. However, recent developments have introduced novel techniques that further improve efficiency and effectiveness in the welding process.
For instance, the implementation of hybrid welding methods combines the best of laser and plasma approaches, creating a synergy that enhances precision and strength without compromising thermal integrity. Hereâs a glance at some important techniques:
- Direct Energy Deposition: This innovative method involves the simultaneous melting of materials and formation of ceramic structures, allowing more elaborate designs to be realized without complex processing.
- Transverse Arc Welding: Utilizing a plasma arc developed in a controlled transverse manner allows for better involvement of the filler material in the weld, producing strong joints with minimized thermal shock.
- Ultrasonic Welding: This technique uses high-frequency vibrations to create localized heat at the interface of ceramics, leading to precise welds with reduced risk of defects.
These new methodologies not only enhance the quality of welds but also optimize production methods, catering to the growing demand for high-performance ceramics in various sectors.
Future Directions of Ceramic Welding Research
Exploring the future directions in ceramic welding research is paramount, as it lays the groundwork for the next generation of applications and technology advancements. This topic not only highlights the existing progress but also opens doors to new methods that can potentially revolutionize the field. The exploration of innovations is crucial for enhancing the performance and reliability of ceramic components in various industries, particularly as the demand for advanced materials increases in sectors such as aerospace, electronics, and medicine. Researchers are keen on methods that can address the inherent challenges posed by ceramics â primarily their brittleness and sensitivity to thermal stresses. Gradually, these advancements will carve pathways for the integration of ceramics in ways previously thought impractical, amplifying their utility.
Nanotechnology Applications
Nanotechnology is making waves within the realm of ceramic welding. At its core, this approach focuses on manipulating materials at the atomic or molecular level to enhance their properties. In ceramic welding, the application of nanotechnology can lead to significant improvements in joint strength and durability. For instance, embedding nanoparticles within the ceramic matrix can bolster its toughness, effectively reducing the chances of cracking during the welding process. These nanoparticles often enhance thermal conductivity, ensuring the material can better withstand extreme temperatures.
Moreover, nanotechnology facilitates the creation of more efficient bonding agents, allowing for better adhesion of ceramic materials without compromising their structure. This could mean different welding techniques can be intertwined, leading to hybrid approaches that leverage both mechanical and chemical bonding.
"The application of nanotechnology in ceramics may just be the key to solving many traditional challenges associated with welding in this field."
Integration with Other Materials
The future of ceramic welding does not solely rest on the development of ceramic materials themselves but also on their integration with other substances. Combining ceramics with metals or polymers can yield composites that draw from the strengths of each material. For example, metal-ceramic composites offer enhanced thermal stability while maintaining a lower weight, making them ideal for applications in space and aviation.
The challenges of joint integrity in welding ceramics can often be alleviated through hybrid solutions. Imagine a ceramic forming a tough outer shell, complemented by a metal core that provides flexibility and strength. This approach not only enhances the performance of the material but also offers solutions to problems of cracking and thermal expansion discrepancies.
As research progresses, we may see a surge in multi-material approaches where ceramic elements are seamlessly integrated into architectures with other materials. This will likely lead to new frameworks in design and manufacturing processes, promising to optimize material performance for specific applications.
In summary, the future directions of ceramic welding research open up avenues brimming with potential, emphasizing the necessity for innovation in our approaches and the technology that supports them. This journey will undoubtedly shape the future landscape of materials science, paving the way for materials that could change the way we design and utilize technology in various sectors.
End
The conclusion serves as a critical juncture in the journey through ceramic welding. It brings together the multifaceted aspects of this field, summarizing both the complexities faced and the advancements achieved over time. Highlighting the sheer importance of this topic, especially in an age where technology dances to the tune of innovation, it becomes clear why understanding ceramic welding matters to various stakeholders.
Summary of Key Points
In revisiting the essential components discussed, several key points emerge:
- Diverse Techniques: From laser welding to plasma arc, a variety of methods can be employed, each offering unique benefits and challenges specific to ceramics.
- Material Properties: The inherent properties of ceramicsâmechanical, thermal, and chemicalâshape the welding processes, requiring tailored approaches to ensure strong, stable unions.
- Challenges: Issues such as thermal stress and joint integrity play significant roles in defining how these materials behave when welded, making it essential for researchers and professionals to remain vigilant about these factors.
- Innovative Solutions: Ongoing research and advancements in nanotechnology and technique development signal a promising horizon for ceramic welding, demanding attention from engineers and researchers alike.
- Applications Across Industries: The implications stretch across various fieldsâincluding electronics, aerospace, and automotiveâshowing that mastering ceramic welding is not just an academic pursuit but a crucial industry need.
"Unlocking the potential of ceramic welding can lead to breakthroughs in technology and manufacturing, enhancing performance and durability in critical applications."
The Path Forward
Looking ahead, the trajectory of ceramic welding research paints a dynamic picture. Future explorations might focus on:
- Integration with Advanced Materials: Ongoing studies indicate a trend towards blending ceramics with other materials to enhance welding compatibility and performance.
- Sustainable Practices: Deploying eco-friendly techniques and materials could transform the landscape of ceramic welding, aligning with broader environmental goals.
- Enhanced Simulation Techniques: Utilizing sophisticated modeling and simulation tools could streamline the understanding of complex welding behaviors, paving the way for more efficient and effective processes.