Cubic Boron Nitride: Properties, Synthesis, and Uses
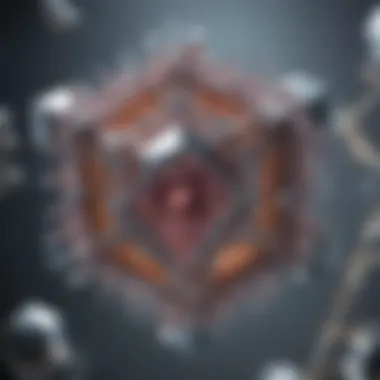
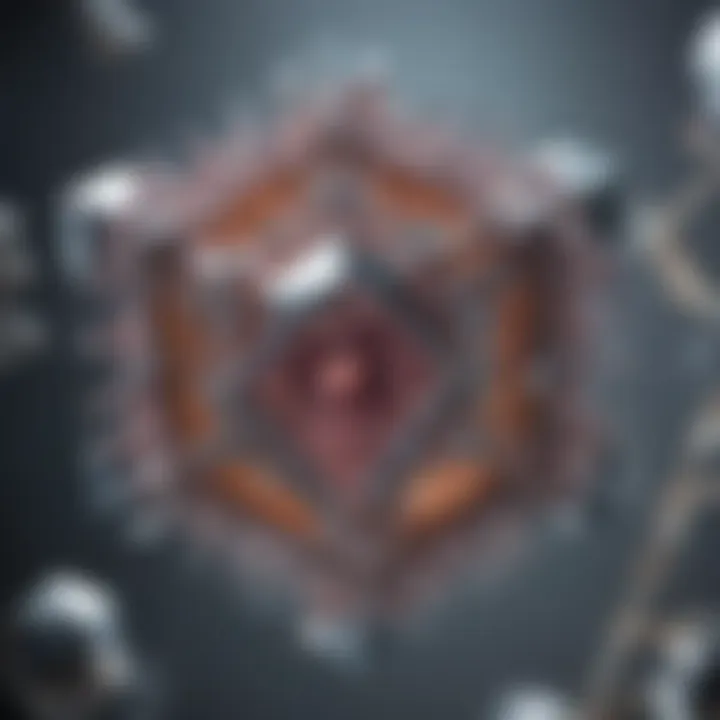
Intro
Cubic boron nitride (CBN) is not just another material floating in the vast sea of synthetic substances; it carries with it a compelling story of discovery, utility, and promise. Born from the need for a tougher alternative to diamond, CBN has forged its own niche in various industries, demonstrating its prowess as an abrasive and its role in cutting tools. While many might associate toughness merely with economics, the scientific implications of cubic boron nitride stretch beyond cost-effectiveness and into the very fabric of material science.
To understand CBN, one must first grasp its foundational structure. Similar to diamond, it crystallizes in a cubic lattice, yet possesses distinct properties that set it apart. Its robustness allows it to withstand high temperatures and corrosive environments, thereby earning its place in specialized applications ranging from manufacturing to electronics. (The nuances of its molecular bonds and the arrangement of atoms contribute to these unique characteristics.)
In this exploration, we’ll dive deep into the many facets of CBN, from its synthesis methods to its current applications, while also taking a glimpse into the future implications for research and innovation.
Research Overview
Methodological Approaches
Understanding the nuances of CBN entails examining the methodologies employed in its study and production. Various synthesis techniques have popped up over the years, each with its own merits and drawbacks. Whether it’s through high-pressure, high-temperature (HPHT) methods or chemical vapor deposition (CVD), the approach often greatly influences the end material’s characteristics, such as hardness and thermal stability.
For instance, HPHT methods often yield CBN crystals at faster rates, but the energy input can be quite significant. Alternatively, CVD allows for more controlled growth of films suitable for industrial coatings and has garnered attention for its adaptability to different substrates. The following methods are integral in shaping the landscape of CBN production:
- High-Pressure High-Temperature (HPHT): Mimics natural diamond formation, yielding bulk crystals.
- Chemical Vapor Deposition (CVD): Enables the creation of thin films, often vital in coating applications.
Significance and Implications
The significance of understanding cubic boron nitride extends well beyond the laboratory table. CBN’s unique properties position it as a viable candidate for advanced applications in cutting and grinding tools, which is critical in various sectors, including manufacturing and mining. Furthermore, with its high thermal stability, there’s increasing interest in its application in electronics, helping address challenges related to heat management in high-performance devices.
"Cubic boron nitride is not just about abrasiveness; it represents a crossroads of various scientific fields, linking material science, engineering, and technology."
In an era where efficiency and sustainability hold significant weight, exploring the potential of CBN in new arenas not only benefits industries economically but also contributes to the broader discourse on sustainable material practices.
Current Trends in Science
Innovative Techniques and Tools
As research progresses, the advent of innovative techniques in the synthesis of cubic boron nitride has become increasingly clear. Scientists are tirelessly refining methods to enhance the quality of CBN produced, focusing on reducing impurities and maximizing crystal growth efficiency. The introduction of machine learning algorithms in predicting growth outcomes has also been noteworthy, as it helps streamline processes and improve yields.
Interdisciplinary Connections
Moreover, the interdisciplinary nature of CBN research brings together chemists, material scientists, and engineers. This collaboration fosters novel perspectives and applications, promoting a holistic study of how CBN can be integrated into new technology developments. By understanding its interactions with other materials and its behaviors in various applications, fresh pathways can be opened for its use, heralding an exciting possibility for future hybrids in the world of materials.
Understanding Cubic Boron Nitride
Cubic boron nitride, commonly referred to as cBN, embodies a topic that calls for in-depth exploration due to its unique characteristics and applications. Considered the second hardest material, right after diamond, cBN is more than just a synthetic substitute. The importance of understanding cubic boron nitride lies in its multifaceted role across various industries, particularly in manufacturing and material technology. Emerging from its distinctive properties, cubic boron nitride presents substantial benefits that differentiate it from its well-known counterpart, diamond.
The discussion begins with how cubic boron nitride can withstand harsh conditions, enabling its usage in high-temperature operations that would be detrimental to traditional materials. Additionally, its thermal stability and wear resistance make cBN an invaluable asset, which we will delve into further along this article.
"Cubic boron nitride not only matches diamond's hardness but also offers unique advantages in thermal and chemical stability, making it essential in modern machining processes."
Definition and Basic Composition
Cubic boron nitride is a synthetic compound composed of boron and nitrogen, structured in a crystal lattice similar to that of diamonds. It was synthesized first in the 1950s and its chemical formula, simply written as BN, consists of one boron atom for every nitrogen atom. The cubic form of this compound reflects a tight arrangement of atoms, contributing to its formidable hardness and durability.
In its essence, cBN is particularly significant in industrial applications where durability and resilience to wear are paramount. The elemental composition, combined with its structured configuration, creates a material that not only withstands the tests of time but also performs effectively under astronomic pressures and temperatures. The end product is a rugged material able to handle mechanical stress, making cBN a go-to choice for tools and abrasives.
Comparison with Diamond
Comparing cubic boron nitride to diamond reveals both similarities and differences that are crucial for understanding their respective applications and advantages. Both materials share a cubic crystal structure, and both possess extreme hardness. However, cBN has distinct properties that can outshine diamond in various applications. For example, while diamond remains a benchmark for hardness, it lacks the same thermal stability as cBN. At elevated temperatures, diamonds can degrade, which is not the case for cubic boron nitride, leading to its preference in high-heat industrial environments.
Moreover, in chemical applications, cBN has proven to be resistant to oxidation and reactive environments, trumping diamond once again. These qualities allow it to be utilized in cutting tools and abrasives that encounter extreme conditions. Given these factors, the consequence is a notable shift in tool design and utilization, having implications that reach across various manufacturing sectors.
In summary, while both cubic boron nitride and diamond shine brightly as materials at the top of the hardness scale, understanding their differences clarifies why cubic boron nitride holds an irreplaceable position in technological advancement.
Structural Characteristics
Understanding the structural characteristics of cubic boron nitride (CBN) is crucial for grasping its functionality in various applications. The unique arrangement of atoms and the resulting properties enable CBN to outperform other abrasives and cutting materials. These structural elements not only contribute to its impressive hardness but also affect thermal stability, electrical conductivity, and chemical resistance. As we delve deeper, it becomes evident that the design and bonding of CBN’s components are key to its role in modern industries.
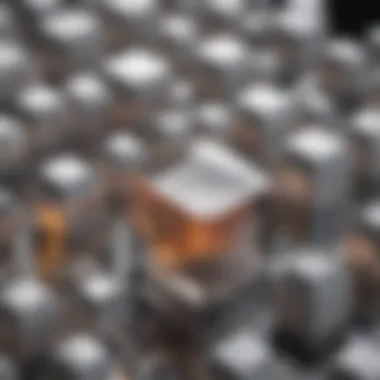
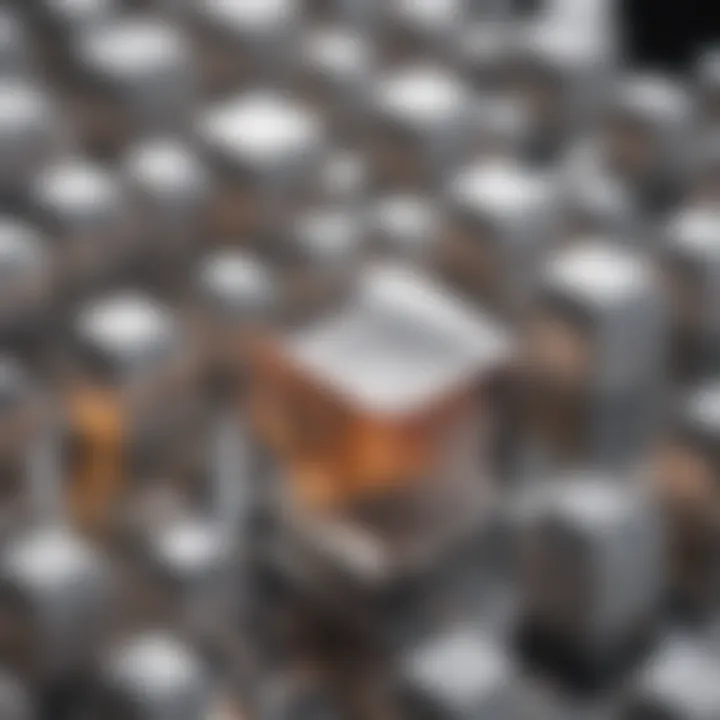
Crystal Structure
The crystal structure of cubic boron nitride is significant. It crystallizes in a face-centered cubic (FCC) lattice, similar to diamond. This arrangement means that boron and nitrogen atoms are densely packed, providing high stability. The FCC structure allows for a strong geometric arrangement that enhances hardness, making CBN an ideal replacement for diamond in certain situations. Unlike diamond, which is a pure carbon structure, CBN's alternating boron and nitrogen atoms create a different set of mechanical and thermal properties.
Key aspects of CBN's crystal structure include:
- Variability: The crystal structure can adapt slightly based on temperature and pressure conditions during synthesis.
- Symmetry: High symmetry contributes to the isotropic nature of CBN, meaning its properties are consistent in all directions.
- Density: CBN has a density of about 3.4 grams per cubic centimeter, which is substantial but less than that of diamond, around 3.5 grams per cubic centimeter. This difference can affect choices in specific applications.
The crystal lattice not only provides physical strength but also influences how CBN interacts with other materials. This is especially important in machining or cutting tools where materials are subjected to high stress and wear.
Bonding Nature
The bonding nature of cubic boron nitride showcases how chemical interactions contribute to its robust properties. CBN is formed primarily through covalent bonding between boron and nitrogen atoms, creating a stiff network that endows CBN with immense hardness.
- Covalent Bonds: Boron and nitrogen share electrons, resulting in strong bonds that are crucial for structural integrity. The orientation and strength of these bonds are significant for applications requiring durability and resistance to abrasion.
- Hybridization: The bonding involves sp3 hybridization, a characteristic shared with diamond, which leads to a tetrahedral arrangement around each boron and nitrogen atom. This arrangement is responsible for unique hardness levels and thermal conductivity.
- Thermodynamic Stability: The strong bonding contributes to the high thermal stability of CBN, which can withstand temperatures up to about 1,500 degrees Celsius without degrading. This stability allows CBN to maintain its shape and cutting ability in challenging conditions.
In summary, the structural characteristics of cubic boron nitride provide a robust framework that defines its use in various industries, from cutting tools to abrasives. The unique crystal structure, combined with its strong chemical bonds, makes CBN an essential material in advanced engineering applications. As the demand for high-performance materials increases, understanding these characteristics will be crucial for future innovations.
Properties of Cubic Boron Nitride
Cubic Boron Nitride (cBN) stands out as more than just a synthetic gemstone or an industrial material; it embodies a plethora of properties that lend it practical value across various sectors. Understanding these properties isn't just an academic exercise; it reveals how cBN can outperform other materials and meet the demanding challenges of modern applications. Let's take a closer look at the key properties that define cBN, focusing on its hardness and durability, thermal stability, and electrical characteristics. Each of these aspects underscores the significance of cubic boron nitride in contemporary engineering and materials science.
Hardness and Durability
Cubic Boron Nitride is renowned for its remarkable hardness, ranking second only to diamond on the Mohs scale. This quality is pivotal in its role as an abrasive. Notably, cBN does not only match diamond’s abrasive capabilities but also surpasses it when it comes to machining hard materials—especially those that would quickly wear out conventional tools. This is crucial because in manufacturing, tool longevity means less downtime and reduced costs.
Key characteristics of cBN hardness:
- Wear Resistance: cBN exhibits exceptional wear resistance compared to other materials, which allows it to maintain sharp cutting edges for extended periods.
- Minimal Degradation: Unlike diamond, cBN does not deteriorate when working with ferrous materials. This means tools made from cBN can effectively cut through steel without going dull.
An often-cited statistic: cBN tools can last two to three times longer than traditional tools, leading to substantial cost savings in industrial applications.
“Using cubic boron nitride tools results in larger returns on investment due to their longevity and performance.”
Thermal Stability
Another defining property of cBN is its impressive thermal stability. While many materials begin to degrade at high temperatures, cBN can endure extremes—making it invaluable for high-speed machining and other heat-intensive operations. The temperature at which cBN starts to break down is significantly higher than that of diamond, which is particularly advantageous in situations where heat generation is a concern.
Consider the key thermal stability features of cBN:
- High Thermal Conductivity: It possesses efficient heat dissipation capabilities, allowing for cooler operation during machining processes.
- Thermal Shock Resistance: It can withstand rapid temperature changes, which is critical in applications such as composites machining and the automotive sector.
This makes cubic boron nitride not just a go-to choice for professionals aiming to keep their processes cost-effective, but also a reliable companion in the struggle against thermal degradation.
Electrical Properties
Beyond its mechanical characteristics, cBN also showcases unique electrical properties. It is classified as an electrical insulator, which allows it to be beneficial in high-temperature applications where electrical conductivity could lead to problems.
Finding highlights on electrical properties:
- Insulating Capabilities: The insulation properties keep the performance of electric components stable, especially in high-stress environments.
- Low Friction: When used in lubricants, cBN reduces friction, leading to extended machinery life.
In summary, the properties of cubic boron nitride—its hardness and durability, thermal stability, and electrical properties—make it a material of choice in numerous applications ranging from cutting tools to abrasives. The combination of these exceptional characteristics positions cBN at the forefront of modern material science, promising an array of innovative applications and efficiency solutions for various industries.
Synthesis Methods
Synthesis methods are core to understanding how cubic boron nitride can be produced and tailored for various applications. This section dives deeper into the pathways that lead to the creation of this remarkable material. The chosen synthesis method not only influences the material's structure but also determines its properties and potential uses. Knowing about these methods enriches our knowledge, allowing us to appreciate the advancements and limitations associated with cubic boron nitride. The two prominent synthesis techniques discussed here are the High-Pressure High-Temperature method and the Chemical Vapor Deposition method.
High-Pressure High-Temperature (HPHT) Method
The High-Pressure High-Temperature method is quite significant because it mimics the conditions under which natural diamonds form. In a nutshell, this method employs a pressure of about 5-15 GigaPascals and temperatures around 1,400 to 2,500 degrees Celsius. The result? A robust production line for cubic boron nitride.
This approach entails using boron and nitrogen as the starting materials, often in the presence of a metal catalyst that promotes the reaction. The process not just produces cubic boron nitride, but it also ensures that the resulting material exhibits superior hardness, making it ideal for industrial abrasives.
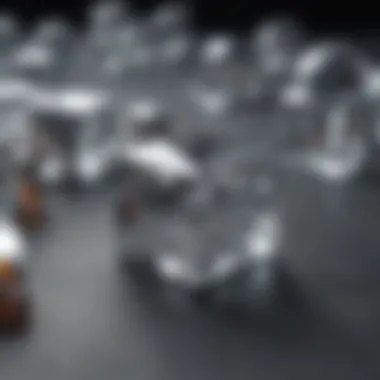
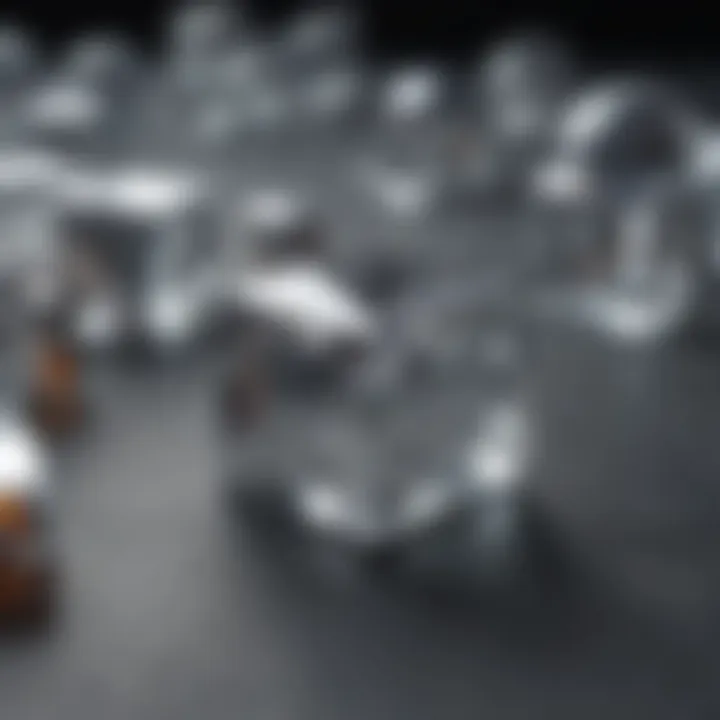
Benefits of HPHT include:
- High Purity: It often yields high-purity cubic boron nitride, which is critical for many applications.
- Control Over Properties: By adjusting pressure and temperature, one can fine-tune the physical properties.
- Potential for Large-Scale Production: While initially seen as experimental, advances have made this method more feasible for large-scale use.
However, there are challenges with this method. The energy costs can be astronomical, and the equipment needed to achieve these high pressures and temperatures is far from trivial. Overall, HPHT offers a wonderful balance between complexity and the desirable properties of the resultant cubic boron nitride.
Chemical Vapor Deposition ()
On the other hand, Chemical Vapor Deposition stands out for its versatility and efficiency. In CVD, gaseous precursors decompose on a substrate to form a solid layer. It’s not just a method; it’s an art form of material engineering.
The typical process involves nitrogen and boron gases, which react to deposit cubic boron nitride onto a suitable surface. One of the significant advantages of CVD is its capability to produce thin films of cubic boron nitride with excellent adherence and uniformity.
Key features of CVD include:
- Scalability: The process can be adjusted for small or large-scale production without significant changes in methodology.
- Lower Energy Requirements: Compared to HPHT, the energy consumption tends to be lower, marking it as a more eco-friendly option.
- Superior Control: CVD allows tighter control over the thickness and quality of the deposit.
Drawbacks? Well, while the method is flexible, it can sometimes be limited by precursor availability or purity. Moreover, the final properties of cubic boron nitride can be sensitive to the deposition conditions, which makes process optimization essential.
In summary, both methods — HPHT and CVD — bring unique benefits and challenges when synthesizing cubic boron nitride. As we forge ahead, understanding these synthesis pathways will pave the way for innovative applications, furthering our grasp of this extraordinary material.
"The choice of synthesis method can fundamentally alter the properties of cubic boron nitride, affecting everything from hardness to thermal stability."
This deep dive into synthesis methods not only illuminates the pathways of creation but also hints at its future potential, providing a foundational insight into cubic boron nitride's role in advanced material science.
Applications of Cubic Boron Nitride
Cubic boron nitride, often hailed as the second hardest material after diamond, finds its niche in diverse applications that leverage its unique properties. Its robustness and remarkable thermal performance make it a material of choice across several industrial domains. Understanding these applications not only sheds light on its practical significance but also illustrates its potential to drive advancements in various fields. From grinding to cutting, the attributes of cubic boron nitride play crucial roles that enhance efficiency and precision.
Industrial Abrasives
The application of cubic boron nitride as an industrial abrasive is perhaps the most prevalent. Its exceptional hardness and thermal stability are pivotal in the production of abrasive products used for grinding and polishing. When compared to conventional abrasives, which can lose effectiveness under high temperatures, cubic boron nitride maintains its integrity and performance. This property is particularly crucial in industries that require machining of tough materials, such as hardened steel and superalloys.
- High-Performance Grinding: Abrasive wheels made with cubic boron nitride can deliver superior performance in grinding applications due to their resistance to wear and ability to cut through materials more efficiently.
- Tool Longevity: Tools crafted from cubic boron nitride are known to outlast traditional abrasives, reducing production costs over time due to less frequent replacements.
- Versatility: This material is adaptable for various grinding processes, including fine grinding and surface finishing, enhancing overall operational flexibility.
Cutting Tools
Cubic boron nitride has carved out a substantial role in cutting tool applications, taking center stage in machining operations. The attributes of this material make it particularly effective in cutting non-ferrous metals and other tough materials that would otherwise wear down conventional cutting tools.
- Efficiency: The cutting tools infused with cubic boron nitride are capable of achieving higher speeds and feeds, leading to improved productivity in machining processes.
- Heat Resistance: The ability to withstand higher temperatures without degrading allows these cutting tools to maintain sharp edges longer, significantly elevating their performance over time.
- Enhanced Surface Finish: Tools made from cubic boron nitride provide superior surface finishes due to their fine-cutting capabilities, often eliminating the need for additional polishing.
Other Precision Tools
Beyond abrasives and cutting tools, cubic boron nitride is utilized in various other precision tools offering benefits that are hard to overlook. Tools engineered from this material can facilitate better control and precision in applications like die-making and precision machining.
- Drills and Inserts: Cubic boron nitride is a trusted material for manufacturing drill bits and insert tips due to its sharpness retention and wear resistance.
- Specialized Equipment: It is also incorporated into specialized equipment used in aerospace and automotive industries, where the demand for precision and durability is paramount.
- Advancements in Technology: Research and development continue to introduce innovative uses of cubic boron nitride, driving its application in emerging sectors like nanotechnology and semiconductor fabrication.
"Cubic boron nitride isn't just another material; it’s a cornerstone of modern machining and manufacturing."
These applications highlight the crucial role that cubic boron nitride plays in enhancing productivity and efficiency across various industries. As researchers and engineers continue to explore its unique properties, the scope of its applications is destined to expand, paving the way for groundbreaking innovations.
Advantages Over Traditional Materials
Cubic boron nitride (CBN) has emerged as a standout material in a range of applications, especially when stacked against more common options. Understanding why CBN is considered superior to traditional materials offers valuable insights into its unique value. This section digs into the critical benefits and considerations tied to CBN’s adoption in various fields.
Performance Efficiency
The efficiency of a material in practical applications can make or break its desirability. CBN is not just resilient; its performance characteristics often overshadow those of traditional materials like diamond and aluminum oxide. Its hardness and thermal stability are essential factors when it comes to machining and cutting operations. CBN tools can endure higher temperatures without degrading, which is crucial when cutting superalloys or hardened steels.
Furthermore, CBN exhibits a chemical inertness that makes it less prone to wear compared to other abrasives. This gives it longevity, which appeals to industries looking to optimize their operational times. Also, the enhanced cutting speeds offered by CBN tools translate into reduced processing times, meaning less downtime for machinery.
"CBN tools provide a cutting edge in both durability and efficiency, making them indispensable for modern manufacturing."
Cost-Effectiveness
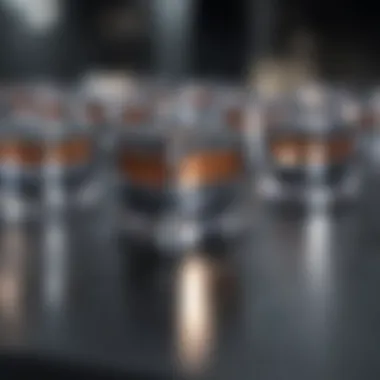
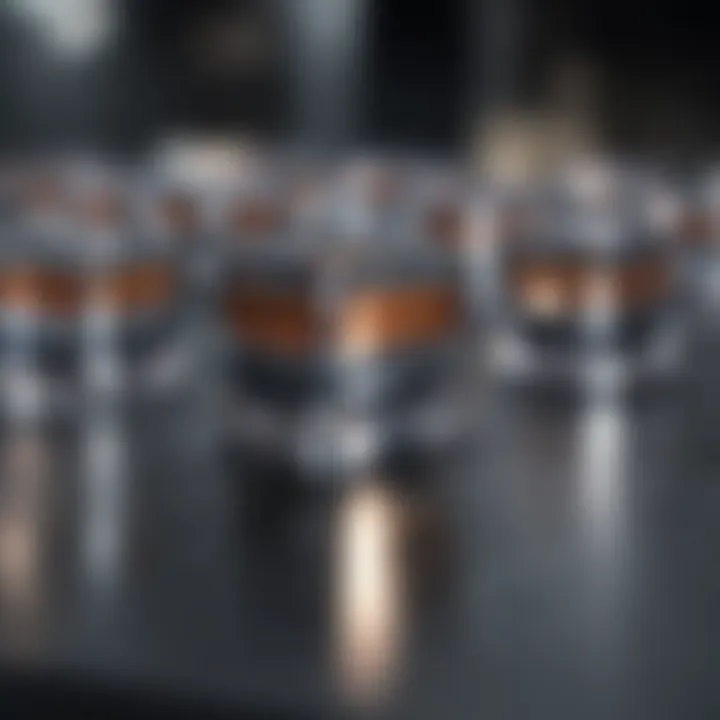
While the upfront cost of cubic boron nitride products may appear higher than the familiar alternatives, a closer examination reveals a cost-effectiveness that can’t be overlooked. The extended lifecycle of CBN tools significantly reduces the frequency of replacements. This justifies the initial investment, particularly in high-demand situations where the cost of downtime can be substantial.
Moreover, as businesses scale and demand for precision increases, the savings realized from CBN’s performance efficiency can outpace traditional materials long term. Using CBN eliminates the need for constant replacements which further tightens budget constraints.
In practical terms, operators often find that CBN tools can maintain their sharpness longer than those made from diamond or other conventional materials, yielding a lower overall cost of ownership. This factor cannot be underestimated in an industry driven by margins.
In summary, while specific applications will often dictate material choice, the advantages that cubic boron nitride holds over traditional options create compelling arguments for its broader utilization in modern manufacturing and precision tooling.
Challenges in the Use of Cubic Boron Nitride
Cubic boron nitride (CBN) has carved its niche in numerous industries due to its impressive properties, but like all materials, it is not without its challenges. Understanding these obstacles is crucial for anyone looking to utilize CBN in practical applications. This section examines the primary challenges associated with CBN, categorized into processing techniques and market competition.
Processing Techniques
The synthesis of cubic boron nitride involves various processing techniques, each with its own set of complexities. While methods like High-Pressure High-Temperature (HPHT) and Chemical Vapor Deposition (CVD) have yielded excellent results, they also present challenges that need to be tackled.
- HPHT Method Challenges
HPHT, despite being widely used, is notorious for requiring immense pressure and temperature to create conditions conducive to CBN formation. This means that the equipment used is not only expensive but also requires constant maintenance. Moreover, achieving uniform quality in the produced CBN material can be tricky. Inconsistent outcomes can lead to performance issues in the end-use applications. - CVD Method Limitations
CVD has its own hurdles. One major concern is the scaling up of production. When trying to translate laboratory success into large-scale manufacturing, the parameters that worked in small batches may not yield the same outcomes in larger volumes. Additionally, the cost of precursor materials needed for CVD is often high, which can affect the overall cost-effectiveness of CBN applications. - Impurities and Defects
Regardless of the method, impurities and defects in the crystalline structure tend to crop up, impacting the performance of the final product. This necessitates rigorous quality control processes, which can drive up costs and limit agility in production cycles.
Market Competition
The landscape of materials used in similar applications as cubic boron nitride is highly competitive. CBN competes primarily with industrial diamonds as abrasives and cutting tools. While CBN offers unique advantages, navigating the market competition poses considerable challenges:
- Established Alternatives
Diamonds have been around for much longer and hold a strong position in the market. The trust and familiarity that industries have with diamonds make it hard for CBN to gain a foothold. Reinforcing the mentality that CBN can deliver superior performance is not an easy task. - Cost of Entry
For businesses, investing in CBN technology often requires a significant upfront financial commitment. This becomes a deterrent, especially when more established options, although not as durable, are available at a lower price point. - Consumer Awareness
There’s a general lack of awareness around the benefits of CBN compared to traditional materials. Educating potential users about its advantages—like thermal stability, hardness, and cutting efficiency—requires substantial marketing resources and time. Without this investment, CBN can struggle to break into new sectors.
Future Research Directions
As we forge ahead in the quest for materials that meet the increasingly demanding requirements of modern technology, cubic boron nitride (cBN) stands out as a subject ripe for further inquiry. The significance of this material extends beyond its established uses in tools and abrasives; its potential innovative applications and advancements in synthesis methods represent pivotal areas for future research. Understanding these directions can illuminate the broader implications for material science and industrial applications.
Innovative Applications
One promising avenue for research involves finding novel applications for cubic boron nitride. Traditionally recognized for its hardness and thermal stability, researchers are now exploring its suitability in various fields. For instance, cBN could play a critical role in advanced coatings for cutting tools or high-temperature machinery, where extreme environments demand materials that can withstand not only intense heat but also wear and corrosion.
Moreover, the electronic industry may benefit significantly from cBN. As a semiconductor, it exhibits unique properties that could lead to the creation of ultra-efficient electronic devices. Its potential as a substrate for gallium nitride-based devices opens up new possibilities in optoelectronics and high-frequency applications.
- Possible innovative applications include:
- Advanced coatings for aerospace and automotive industries
- Semiconductor material in electronics
- Components for high-power lasers
- Thermal management systems
The pursuit of these applications necessitates interdisciplinary collaboration among experts from fields such as materials science, engineering, and electronics. Researchers must not only identify the requirements of these potential uses but also tailor cBN properties accordingly.
Enhancements in Synthesis
Another key area for future exploration is the enhancement of synthesis methods for cubic boron nitride. As highlighted earlier, the High-Pressure High-Temperature (HPHT) and Chemical Vapor Deposition (CVD) processes serve as the primary techniques for cBN production. However, optimizing these processes could lead to higher purity, better quality, and reduced costs of synthesized cBN.
Advancements might include:
- Developing new catalysts that can streamline the CVD process, enhancing reaction rates while reducing energy requirements.
- Exploring alternative precursors that could improve the efficiency of diamond-like material without compromising the inherent properties of cubic boron nitride.
- Investigating environmentally friendly methods to produce cBN, addressing sustainability concerns while maintaining high performance.
"In material science, the synthesis route can often determine the properties and performance of materials more than the composition itself."
Efforts to refine these synthesis methods underscore the larger trend in materials research focused on efficiency and sustainability. As industries lean toward greener practices, the demand for innovative and resource-efficient manufacturing techniques will only increase.
The journey into the future for cubic boron nitride is undeniably promising, but it will require concerted efforts from diverse fields to unlock its fullest potential. As researchers get their hands dirty in the synthesis labs and application workshops, the next breakthrough might just be around the corner. Understanding and adapting to these directions not only ensures that cubic boron nitride remains competitive but also expands its horizons into uncharted territories.
End and Implications
Cubic boron nitride stands strong as a remarkable material in the field of science and technology. Its unique properties and versatility provide significant advantages over other materials, particularly in industrial applications. Understanding the importance of cubic boron nitride leads to a clearer picture of its future impact on various sectors, especially as industries strive for efficiency and superior performance.
Summary of Key Points
- Unique Characteristics: Cubic boron nitride showcases similar hardness to diamond while exhibiting superior thermal stability. This makes it an ideal replacement in many tools where diamonds may fall short due to thermal degradation.
- Applications: Its primary uses are found in industrial abrasives, cutting tools, and precision instruments. The resilience and durability of cubic boron nitride enhance the longevity of these tools, making them more cost-effective over their operational life.
- Synthesis Methods: The successful synthesis techniques, such as HPHT and CVD, highlight the advancements in material science, opening doors for innovations in forming other similar materials with desirable properties.
- Challenges and Competition: The market for cubic boron nitride faces challenges, particularly from other materials like synthetic diamond. However, ongoing research can lead to improved production methods that enhance its compatibility and cost-effectiveness.
In sum, the advantages present within cubic boron nitride should compel industries to further invest in its study and application.
Broader Impact on Material Science
The exploration of cubic boron nitride is not just limited to its immediate application; it holds vast implications for the future of material science. As researchers delve deeper into its properties and synthesis, several outcomes are possible.
- Innovative Materials Development: Cubic boron nitride can inspire the creation of new materials that harness the specific qualities that make it desirable. For instance, exploring composite materials that combine boron nitride with other elements could yield even greater performance.
- Environmental Considerations: As industries seek sustainable practices, cubic boron nitride offers a lead by potentially reducing waste in manufacturing processes due to its durability. The higher costs of typical diamond tools could prompt a shift to more sustainable options like cubic boron nitride, aligning with global movements toward eco-friendliness.
- Interdisciplinary Research: The study of cubic boron nitride crosses various fields—physics, engineering, and chemistry, prompting a collaborative approach to research and development that can lead to breakthroughs beyond conventional boundaries.