Exploring Spray Drying Encapsulation Mechanisms
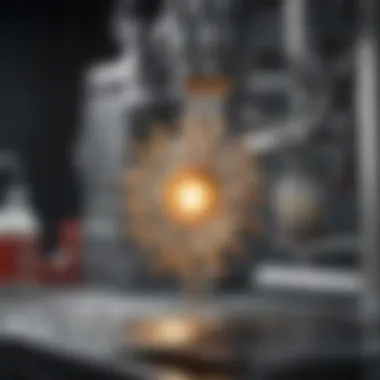
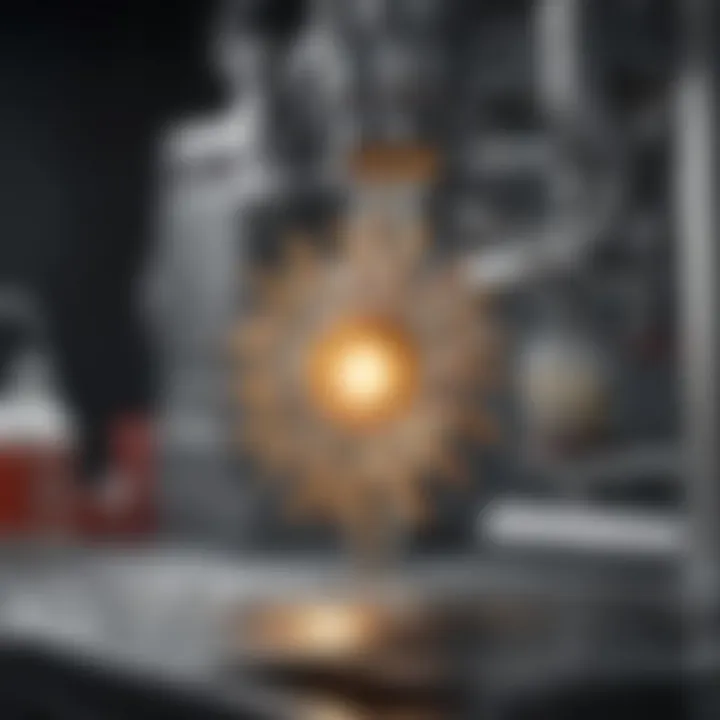
Intro
Spray drying encapsulation serves as an important process in modern industries. This technique is crucial for stabilizing sensitive compounds, enhancing their bioavailability, and broadening their applications. Industries like food and pharmaceuticals rely heavily on this technology. As we move forward in this article, we will explore the intricate mechanisms behind spray drying encapsulation and its various applications.
Research Overview
Methodological Approaches
In order to understand spray drying encapsulation, we must first examine its methodological framework. The process primarily involves the transformation of liquid feed into a dry powder. This is achieved through the evaporation of solvents, usually water, under controlled temperature and pressure conditions. Here are some key components of the methodology:
- Feed Preparation: The materials used must be selected with care. They often include polymers, sugars, and proteins, each influencing the final product properties.
- Spray Drying Process: Involves atomization where the liquid feed is converted into droplets, followed by rapid drying in a heated air environment.
- Characterization of Products: Analysis of the physical and chemical properties of the resultant powder is essential to assess performance in real-world applications.
This combination of steps leads to a robust understanding of how the encapsulation process affects the sensitive compounds involved.
Significance and Implications
The significance of spray drying encapsulation cannot be overstated. By improving stability, this method enhances the functionality and effectiveness of various ingredients, particularly in the following areas:
- Food Industry: Improving shelf-life and taste of food products.
- Pharmaceuticals: Enhancing drug delivery systems and the effectiveness of active ingredients.
- Cosmetics: Stabilizing key ingredients ensuring their efficacy in formulations.
"Spray drying encapsulation not only enhances stability but also addresses challenges posed by environmental factors."
These implications can lead to innovative solutions and improved formulations across multiple sectors, thereby impacting consumer products and experiences positively.
Current Trends in Science
Innovative Techniques and Tools
Recent advancements in spray drying encapsulation have introduced various innovative techniques and tools. These advancements are designed to optimize processes and product quality. Some notable trends include:
- Microencapsulation Technologies: Such as co-spray drying, which allows for improved control over particle size and morphology.
- Advanced Monitoring Systems: Real-time monitoring of temperature and humidity during the spray drying process to ensure uniformity.
Interdisciplinary Connections
Spray drying encapsulation operates at the intersection of various scientific disciplines, including chemistry, material science, and engineering. This interdisciplinary nature allows collaboration and integration of new ideas, aiding in the advancement of techniques and applications. For example:
- Collaborations between material scientists and food technologists can lead to the development of novel food preservation methods.
- Partnerships within the pharmaceutical sector are pushing the boundaries of nanotechnology applications in drug delivery systems.
Each of these connections demonstrates how spray drying encapsulation evolves through combined expertise and shared knowledge.
Prelims to Spray Drying Encapsulation
Spray drying encapsulation is a crucial technique in many modern industries. It plays a significant role in increasing the stability and bioavailability of sensitive compounds. This process involves transforming a liquid solution into a dry powder. Through encapsulation, substances, such as vitamins or flavors, benefit from improved protection against environmental factors. Thus, exploring this topic offers insights into both scientific and practical applications.
Definition and Overview
Spray drying encapsulation refers to the method by which liquids, often containing heat-sensitive materials, are converted into a dry powder through precise control of temperature and airflow. This technique creates micro- or nanoparticles that enclose the sensitive compounds. Encapsulated materials can be better protected against oxidation, moisture, and light, which enhances their shelf life and efficacy.
Key aspects of spray drying encapsulation include the choice of carrier materials, which can vary based on the target compound. For example, a polymer might be selected for its ability to form a barrier around a bioactive material. Moreover, the process parameters, such as inlet temperature, atomization pressure, and feed rate, need careful optimization for optimal results.
Historical Context
The roots of spray drying encapsulation trace back to the early 20th century. Initially, the food industry adopted spray drying as a method for preserving flavor and nutrients in powdered formulations. Early applications were simple, primarily focusing on liquid food products.
However, as industries evolved, researchers identified the potential of this technique in pharmaceuticals and cosmetics. Throughout the decades, advancements in technology have led to more sophisticated equipment and methods.
Governments and institutions have invested in research to explore the scientific principles behind spray drying encapsulation. Today, it is a well-established process that continues to grow in importance across various sectors. The combination of efficiency and effectiveness makes it a focal point in innovative product development.
The Spray Drying Process
Understanding the spray drying process is essential for comprehending how encapsulation methods can enhance the stability and bioavailability of various compounds. This technique has earned its prominence due to its efficiency and versatility in producing dry powders from liquid feeds. These fine powders can preserve the qualities of sensitive materials, making the process crucial for many applications in food, pharmaceuticals, and cosmetics.
Basic Principles
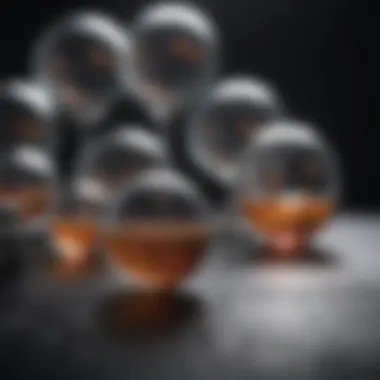
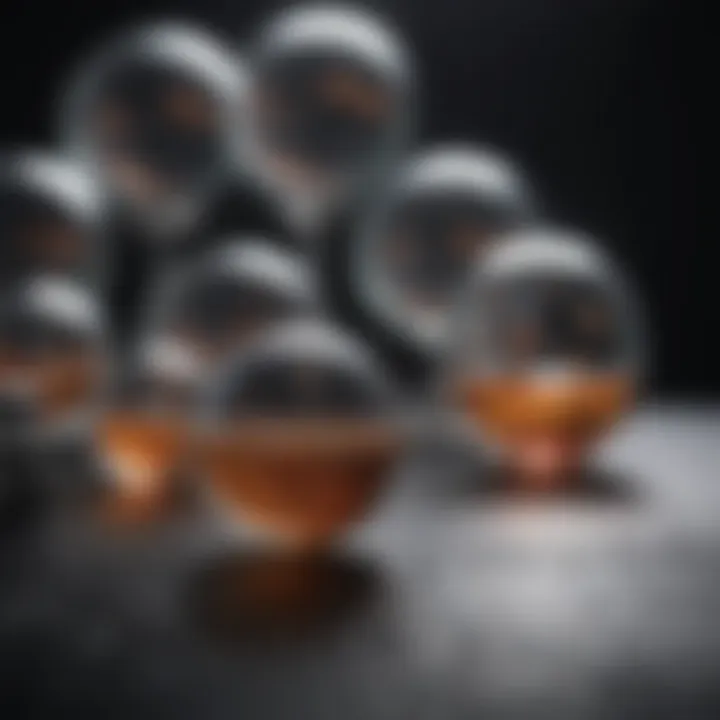
Spray drying is a continuous process designed to transform liquid solutions or suspensions into powder form by employing heat. The main principle involves atomization, where the liquid is broken into tiny droplets that are then exposed to hot air. The solvent evaporates rapidly, leaving behind solid particles. The following key points highlight the basic principles:
- Atomization: The initial step where liquids are transformed into fine droplets using a nozzle or rotary atomizer.
- Evaporation: Hot air is introduced to facilitate rapid drying, ensuring that moisture is removed efficiently.
- Collection: Once the solvent has evaporated, the resulting powder is then collected, often using cyclones or bag filters to separate dry particles from the exhaust air.
This process safeguards the integrity of sensitive compounds because the exposure time to heat is brief. Therefore, the risk of degradation of heat-sensitive materials is minimized.
Equipment Used in Spray Drying
A variety of equipment is employed in spray drying, each playing a critical role in achieving effective encapsulation. The most common types include:
- Atomizers: Devices like pressure nozzles and centrifugal atomizers that create the droplets from the liquid feed. The choice of atomizer influences the size and consistency of the resulting powder.
- Drying Chambers: These are designed to hold the hot air required for evaporation while ensuring adequate residence time for the droplets to dry completely. The configuration of the drying chamber affects the efficiency of the process.
- Air Heaters: They are essential for raising the temperature of the air entering the drying chamber. Precise control of air temperature is vital to maintain optimal drying rates without damaging the compounds.
- Cyclones and Filters: Used for the collection of the final product, they separate the dry powder from the air, ensuring minimal loss of material.
Selecting the right equipment is crucial, as it can significantly impact the overall yield and quality of the encapsulated product.
Process Flow and Parameters
The spray drying process consists of several key parameters that need careful management to ensure high-quality output. These parameters include:
- Inlet and Outlet Temperatures: Controlling the temperatures is crucial as it directly affects the moisture content of the final product. Keeping the inlet temperature high while managing outlet temperatures prevents degradation of the compounds being dried.
- Feed Rate: The speed at which the liquid feed is introduced into the system must be regulated to match the drying capabilities. If the feed rate is too fast, it can lead to inadequate drying and clumping.
- Atomization Pressure: Adjusting the atomization pressure influences droplet size, which is essential for uniform drying and particle size distribution in the final product.
A controlled flow of the drying process not only maximizes efficiency but also ensures that the characteristics of the encapsulated materials are maintained. Understanding these variables allows for the optimization of the spray drying process, leading to better encapsulation outcomes.
Mechanisms of Encapsulation
Understanding the mechanisms of encapsulation is crucial in the context of spray drying. Encapsulation, in this process, serves multiple purposes, including enhancing the stability, bioavailability, and controlled release of various bioactive compounds. This is particularly pertinent for sensitive materials that are prone to degradation due to environmental factors such as heat, moisture, and light. Therefore, investigating both physical and chemical encapsulation mechanisms offers valuable insights into the efficacy of the resulting particles and their applications across various industries.
Different mechanisms can lead to varying outcomes in the properties of encapsulated materials. For example, some methods might prioritize maximizing the retention of volatile compounds, while others could aim for prolonged release profiles. Understanding these mechanisms, therefore, informs best practices and optimizations that meet specific needs across sectors like food, pharmaceuticals, and cosmetics. With this in mind, the exploration of both physical and chemical encapsulation mechanisms becomes not just an academic exercise, but rather an essential element in advancing practical applications of spray drying encapsulation.
Physical Encapsulation Mechanisms
Physical encapsulation mechanisms primarily involve creating a barrier around the active ingredients. This barrier serves to protect the core material from adverse conditions, which prolongs its integrity and effectiveness. Two main methods are widely discussed in the field: matrix formation and layer-by-layer coating.
- Matrix Formation: This mechanism involves embedding bioactive compounds within a solid matrix, typically made from polymers, sugars, or proteins. When the material undergoes spray drying, the solvent evaporates rapidly, trapping the active ingredient within the matrix. This method ensures a steady release of the encapsulated compound during storage and application.
- Layer-by-Layer Coating: Another approach involves depositing various layers of material around the core substance. Using techniques like electrostatic assembly or simple mixing, multiple layers can be added. This not only increases the physical protection of the encapsulated ingredient but can also tailor the release profile based on the thickness and composition of the layers used.
Physical encapsulation is generally preferred due to its simplicity and efficiency. However, it does have limitations, such as the possibility of incomplete encapsulation or leakage over time.
Chemical Encapsulation Mechanisms
In contrast to physical methods, chemical encapsulation mechanisms rely on chemical reactions to secure bioactive materials. This method utilizes various chemical substances to form bonds between the encapsulating agents and the active components.
- Chemical Crosslinking: This technique employs agents that initiate crosslinking reactions, resulting in a network that traps the active ingredient. The stability offered by this method is significant, especially for compounds that are sensitive to heat or other degrading conditions.
- Interactions with Ionic Agents: Some encapsulation strategies involve the use of ionic interactions. The active component forms complexes with oppositely charged agents which results in a stable encapsulation. For example, negatively charged polysaccharides may interact with positively charged proteins to form stable complexes. This could enhance both the stability and bioavailability of the encapsulated material.
Chemical encapsulation often results in stronger bonds, which can lead to improved control over the release dynamics of the active component. While it may involve more complex processes, its advantages make it a valuable method in many applications.
"Both physical and chemical encapsulation mechanisms play a pivotal role in enhancing the effectiveness of spray drying encapsulation, particularly in fields such as pharmaceuticals and food technology."
This exploration of encapsulation mechanisms underscores a broader understanding of how various strategies can influence the effectiveness and application of spray drying encapsulation in real-world scenarios.
Materials for Spray Drying Encapsulation
Materials significantly influence the effectiveness of spray drying encapsulation. The choice of materials determines not only the stability of the encapsulated substances but also affects release profiles, shelf life, and bioavailability of the active compounds. Each material contributes specific properties that can enhance or inhibit the encapsulation process. Therefore, understanding these materials is crucial for optimizing formulations and achieving desired outcomes in various applications.
Polymers and Their Properties
Polymers play a vital role in spray drying encapsulation due to their versatility and ability to form protective matrices around sensitive ingredients. Different polymers exhibit varying thermal and mechanical properties, which are essential for ensuring effective encapsulation.
- Natural vs. Synthetic Polymers: Natural polymers such as gelatin, alginate, and starch possess biocompatibility and good film-forming capabilities. Their biodegradability is beneficial for applications in food and pharmaceuticals. Conversely, synthetic polymers like polyvinyl alcohol and polylactic acid provide superior mechanical stability and tailored release profiles. The choice between natural and synthetic often depends on the specific application and regulatory requirements.
- Molecular Weight: The molecular weight of polymers affects the viscosity of the solution, which influences atomization and particle size during the spray drying process. Higher molecular weight polymers generally provide more robust encapsulation, yet they may increase the viscosity beyond optimal levels, complicating processing.
- Glass Transition Temperature (Tg): Tg is critical for defining the thermal stability of the polymer matrix. Polymers with a high Tg may resist deformation under heat, which is advantageous during spray drying. However, too high a Tg can hinder flowability, making it difficult to achieve a uniform spray.
Stabilizers and Excipient Choices
Stabilizers and excipients are essential in the formulation process for spray drying encapsulation. They assist in maintaining the product's integrity and enhancing the performance of the active ingredients.
- Role of Stabilizers: Stabilizers such as maltodextrin and various sugars help to protect sensitive compounds from degradation. They act by reducing moisture absorption and ensuring a consistent matrix. Additionally, stabilizers can prevent particle agglomeration during the drying process, leading to uniform particle sizes.
- Function of Excipients: Excipients serve multiple purposes, including enhancing solubility and controlling the release rate of active ingredients. For instance, lactose or sucrose can improve the flow properties of the powder, facilitating better processing. Each excipient should be chosen based on its compatibility with the active ingredient and the intended application.
- Synergistic Effects: Using combinations of stabilizers and excipients can yield synergistic effects, leading to improved outcomes. For example, pairing a natural polymer with a synthetic stabilizer may enhance both stability and release control, optimizing the performance of the encapsulated product.
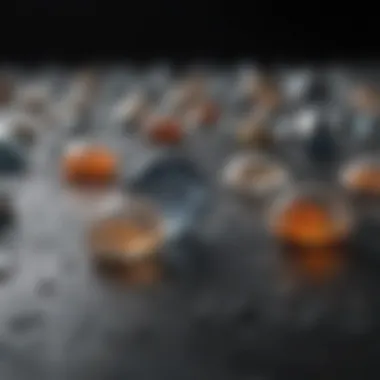
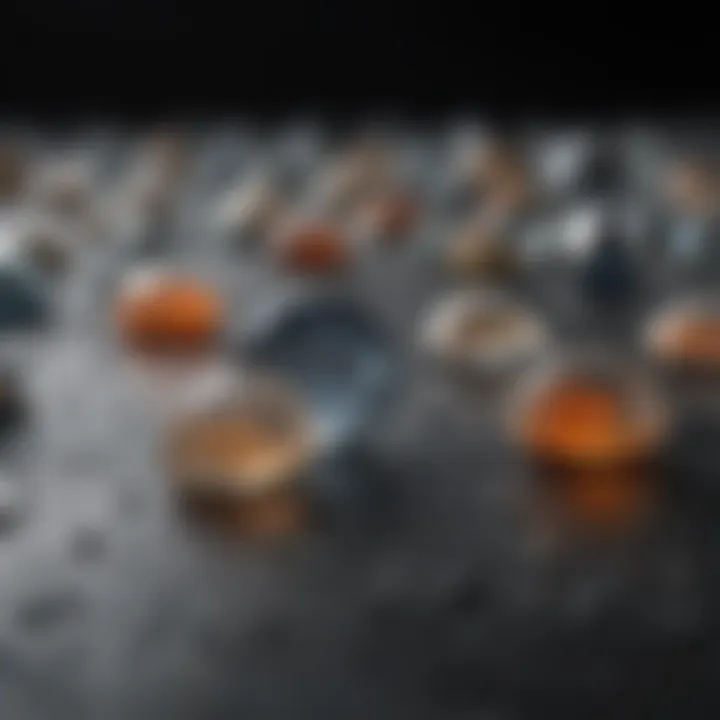
In summary, the careful selection of stabilizers and excipients is vital for ensuring the efficacy and stability of encapsulated products. Their impact on the overall performance cannot be overstated, as they support maintaining the bioactivity of sensitive compounds during storage and application.
The choice of materials in spray drying encapsulation is not merely a technical consideration; it is foundational to the success of product formulation across various industries.
Optimization of Process Parameters
In the arena of spray drying encapsulation, optimization of process parameters stands as a critical factor influencing the overall efficacy and quality of encapsulated products. A thorough understanding of how different parameters interact significantly determines the stability of encapsulated materials as well as their performance in application. This section will address several specific elements related to the optimization of process parameters including temperature control, feed rate management, and atomization techniques.
Temperature Control
Temperature control is fundamental in spray drying processes. It affects the evaporation rate of solvents and the physical state of the encapsulated materials. High temperatures can lead to the degradation of sensitive compounds, while low temperatures might result in inefficient drying.
Specific attention must be paid to the drying temperature settings, which often depend on the nature of the feed solution and the properties of the encapsulating agent. Furthermore, a careful balance must be maintained: if the temperature is too high, it can denature sensitive bioactive compounds, reducing their functionality. In contrast, appropriate temperature settings facilitate a quick drying process, preserving the integrity and stability of the product.
Feed Rate Management
Managing the feed rate is also vital in achieving optimal encapsulation. The feed rate refers to how quickly the feed solution is introduced into the spray dryer. An inappropriate feed rate can lead to several challenges.
- Underfeeding can result in insufficient throughput, decreasing the overall efficiency of the encapsulation process.
- Overfeeding may lead to wet particles, which can agglomerate and compromise the quality of the final product.
Adjusting the feed rate requires careful monitoring of the moisture content and other intrinsic properties of the feed solution. Ideally, a consistent feed rate ensures optimal conditions for effective evaporation while maintaining the efficiency of the drying process.
Atomization Techniques
Atomization is another critical component in the optimization of spray drying encapsulation. This process involves breaking the feed solution into droplets, which significantly influences the drying kinetics and the properties of the final product. Different atomization techniques can be employed, including pressure nozzles, rotary atomizers, and air-assisted atomizers. Each method has its advantages and potential limitations.
- Pressure Nozzles tend to create uniform droplet sizes, which promotes uniform drying.
- Rotary Atomizers are beneficial in producing fine droplets, enhancing evaporation rates.
- Air-Assisted Atomizers, while efficient, may introduce variability in droplet size.
Selecting the right atomization technique can optimize the drying process and influence the quality of the encapsulated material, ensuring desirable particle size distribution and enhanced stability.
Effective management of process parameters is essential for creating reliable encapsulation processes. By fine-tuning temperature, feed rate, and atomization techniques, significant improvements in product quality and efficiency can be achieved.
Applications of Spray Drying Encapsulation
The applications of spray drying encapsulation are vast and varied, leading to significant advancements across multiple industries. This method not only enhances the stability of sensitive compounds but also boosts their bioavailability. It addresses numerous challenges faced in the storage and delivery of various materials. The underlying benefits encompass improved solubility, extended shelf-life, and protection from degradation, all while offering ease of handling and processing.
Food Industry Applications
In the food industry, spray drying encapsulation serves several pivotal roles. It is instrumental in preserving flavors, aromas, and nutrients. Many natural compounds, like essential oils, are prone to instability. Through encapsulation, these compounds can be shielded from environmental factors such as light and oxygen. This ensures that consumers enjoy a product that retains its original quality over time.
Moreover, encapsulation allows for controlled release of flavors during food preparation. For instance, encapsulated flavors in powders can be activated only upon heating or mixing, enhancing the sensory experience. Additionally, it supports the reduction of food waste by maintaining the quality of ingredients longer, a notable aspect amid growing global concerns about sustainability.
- Examples of encapsulated ingredients include:
- Flavor compounds in seasonings
- Omega-3 fatty acids in health foods
Pharmaceutical Applications
The pharmaceutical sector greatly benefits from spray drying encapsulation. It addresses the challenge of formulating drugs that possess low solubility and stability. Many bioactive compounds undergo degradation before reaching the target site within the body. By encapsulating these compounds, their stability is enhanced, and delivery to the bloodstream becomes more efficient.
Additionally, this method aids in the creation of controlled-release formulations, enabling drugs to be released over an extended period. This is especially beneficial for chronic conditions where consistent drug levels are necessary.
โSpray drying encapsulation has transformed the way pharmaceuticals are delivered, ensuring efficacy and patient compliance.โ
- Key advantages include:
- Improved bioavailability
- Protection of sensitive compounds
- Potential for enhanced therapeutic effects
Cosmetic and Personal Care Applications
In the realm of cosmetics and personal care products, spray drying encapsulation finds significant utility. Ingredients like vitamins and essential oils are frequently sensitive to heat and light. Encapsulation provides a means to protect these elements, preserving their efficacy until the product is applied on the skin.
Moreover, it allows for the formulation of products that offer sustained release of beneficial compounds, improving overall skin health and efficacy. This ensures that consumers experience enhanced results when using skincare or cosmetic products.
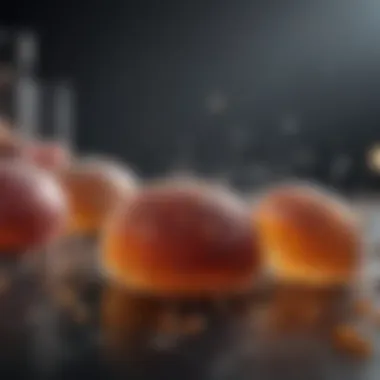
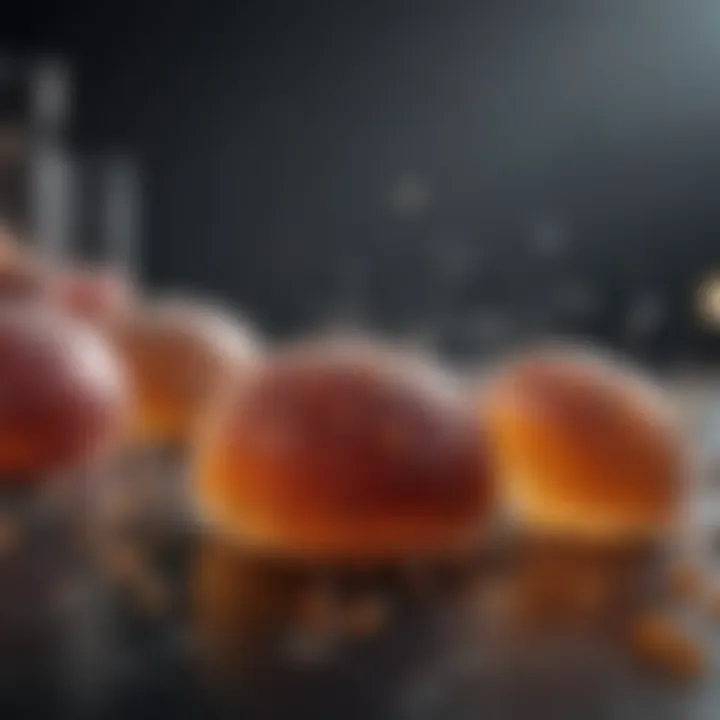
- Common applications in cosmetics include:
- Vitamin E in creams
- Fragrance encapsulation in perfumes
In summary, the applications of spray drying encapsulation across the food, pharmaceutical, and cosmetic industries demonstrate its versatility and importance. By enhancing the stability and bioavailability of sensitive compounds, this technique supports innovation and meets the demands of modern consumers.
Challenges in Spray Drying Encapsulation
Understanding the challenges in spray drying encapsulation is crucial. This knowledge enables researchers and professionals to innovate and enhance the effectiveness of encapsulation processes. Encapsulation is intended to protect sensitive compounds from degradation, yet challenges can impede its success. By exploring these challenges, one can improve the stability and delivery of bioactive ingredients across various industries including food and pharmaceuticals.
Loss of Bioactive Compounds
A significant concern in spray drying encapsulation is the loss of bioactive compounds. During the drying process, conditions such as temperature and the choice of materials can lead to degradation. Sensitive compounds, such as vitamins, flavors, and other nutrients, may lose their efficacy when exposed to heat or oxygen. This loss is particularly troublesome in food and pharmaceutical industries where potent bioactivity is desired.
Key factors include:
- Temperature: High temperatures can denature proteins and degrade vitamins. The design of the spray dryer and drying parameters must carefully balance temperature to protect compounds.
- Process Duration: Longer drying times can exacerbate instability issues, leading to reduced bioactive retention.
- Carrier Materials: The choice of polymers or sugars as carriers can influence how well sensitive materials are protected during the process.
- Moisture Content: If the final product retains too much moisture, it can lead to hydrolytic degradation. Finding a proper balance is necessary for maximizing bioactive compound retention.
This loss affects product quality and marketing appeal. By optimizing drying parameters and selecting appropriate carrier materials, it is possible to minimize this issue.
Scalability Issues
Scalability presents another challenge in the effective use of spray drying encapsulation.
Organizations may struggle to transition from lab-scale to industrial-scale processes. Factors that complicate scaling include:
- Inconsistent Results: Success at small scale does not always translate to large scale. Variations in equipment and conditions can result in different product quality and encapsulation efficiency.
- Equipment Limitations: Not all equipment can handle large volumes while maintaining the necessary control over parameters such as temperature and pressure.
- Cost Considerations: Efficiently scaling up processes can significantly increase costs, which may not always be justifiable in the competitive marketplace.
Developing strategies to address these scalability issues is essential. Manufacturers must consider their process designs carefully to ensure that they can replicate lab results on a larger scale, maintaining product quality and performance.
Future Perspectives in Spray Drying Encapsulation
The future of spray drying encapsulation promises to be exciting and transformative. As industries strive for improved stability of sensitive compounds, researchers and manufacturers are increasingly looking toward new innovations and more sustainable practices. This section will explore technological advancements and sustainability considerations that are shaping the future landscape of this encapsulation technique.
Technological Innovations
Technological innovations play a critical role in enhancing spray drying encapsulation processes. Several key areas of focus include:
- Advanced Materials: The development of new polymers and excipients continues to push boundaries. These materials can provide better protective effects for bioactive compounds.
- Enhanced Equipment: Modernizing spray drying equipment can improve efficiency and product quality. Continuous spray drying systems are emerging, maximizing throughput while ensuring consistent quality.
- Control Systems: Improved control over process conditions can lead to optimized encapsulation efficiency. Automation in monitoring temperature and pressure ensures the preservation of sensitive ingredients.
- Nanotechnology: Applying nanotechnology in spray drying offers high surface area and improved release profiles. This can significantly enhance bioavailability for pharmaceuticals and functional foods.
- Real-Time Monitoring: Integration of real-time monitoring tools can identify issues as they arise, providing immediate corrective actions and increasing production reliability.
"The evolution of technologically advanced spray drying systems is critical for meeting the growing demands of varied industries."
Sustainability Considerations
Sustainability is a pivotal element guiding future research and development in spray drying encapsulation. Several factors underscore its significance:
- Resource Efficiency: Innovations aim to reduce energy consumption in the spray drying process, utilizing lower temperatures to save on resources.
- Biodegradable Materials: The shift toward eco-friendly and biodegradable encapsulating materials is gaining traction. This reduces environmental impact and aligns with global sustainability goals.
- Waste Reduction: Techniques focused on minimizing waste during the spray drying process are crucial. Methods such as recycling used solvents and optimizing feed materials can contribute to lower waste generation.
- Circular Economy: Transitioning toward circular economy principles in production can enhance sustainability. This promotes recycling and reusing materials within the industry, aligning with broader environmental objectives.
Closure and Implications
The study of spray drying encapsulation holds significant relevance in various fields. This concluding section will highlight the main findings and discuss the implications this technique has for future research and applications. Spray drying encapsulation is not merely a processing method; it represents a bridge between existing technologies and future innovations. By ensuring the stability and bioavailability of sensitive compounds, it has become essential in food science, pharmaceuticals, and cosmetics.
Summary of Key Findings
Throughout this article, several critical elements emerged concerning spray drying encapsulation. Some of the key findings include:
- Efficiency of the Process: Spray drying encapsulation is effective in protecting bioactive compounds from environmental factors.
- Diverse Applications: It showcases a wide variety of applications across multiple industries, enhancing ingredients in food, drugs, and personal care products.
- Optimization Challenges: Fine-tuning parameters such as temperature and feed rate is crucial for maintaining the integrity of the encapsulated compounds.
- Innovative Materials: The choice of polymers and other materials directly affects the encapsulation efficacy and product quality.
These findings underscore that while challenges exist, the benefits provided by spray drying encapsulation far outweigh the drawbacks, making it a vital area of focus for researchers and industry professionals alike.
Importance for Future Research
Future research in spray drying encapsulation is essential for numerous reasons. First, understanding the mechanisms involved can lead to improvements in product formulations and processing efficiency. Investigating new materials may allow researchers to identify more effective polymers or stabilizers that enhance encapsulation performance.
Furthermore, as global demand for more stable and bioavailable products increases, innovative approaches and technologies will open new avenues. Sustainability is another paramount concern. Future studies should focus on the environmental impact of the materials used in spray drying and discover alternatives that can reduce waste or enhance biodegradability.
"Spray drying encapsulation is a powerful tool in modern formulations, but continued exploration is required to fully harness its potential."
In summary, the implications of the findings in this article extend beyond the present applications. They echo a need for continued diligence in research and development to maximize the effectiveness of spray drying encapsulation and meet the evolving needs of industries and consumers.