Attributes and Applications of Kevlar Material
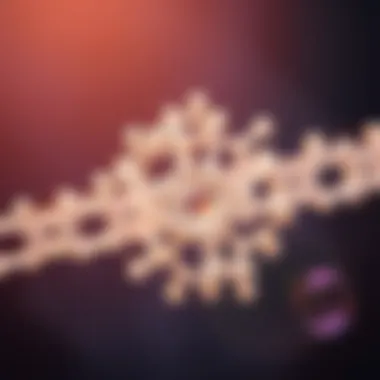
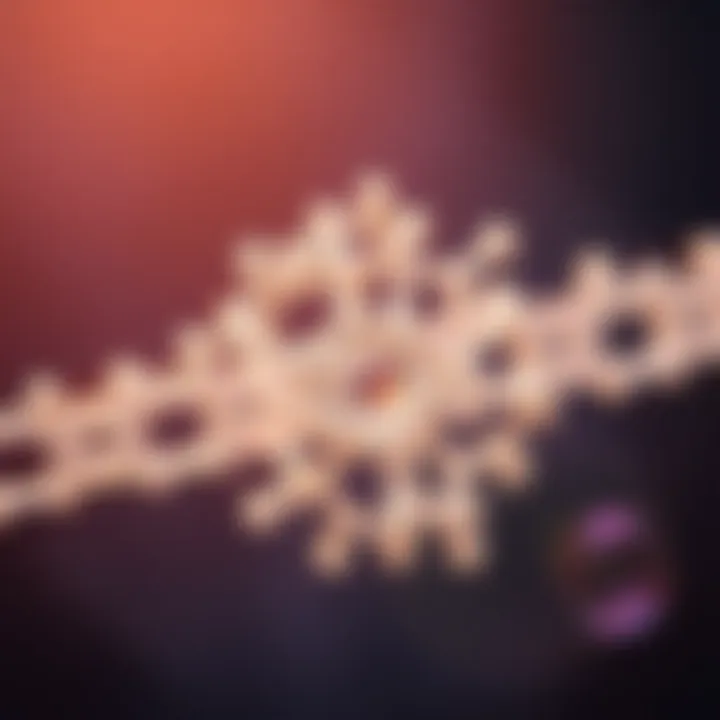
Intro
Kevlar is more than just a name; itâs a game-changer in the realm of materials science. As a synthetic fiber known for its incredible strength and durability, Kevlar has transformed various industries. Originally, this remarkable material was designed for use in vehicle tires, but its unique characteristics have paved the way for numerous applications, from protective clothing to aerospace components. The exploration of Kevlar's attributes goes beyond its physical propertiesâit's a discussion of its production methods, uses, and even its environmental impact.
Understanding Kevlar becomes crucial, especially in today's fast-paced world where safety and innovation are paramount. Whether you're a student or a seasoned professional, diving into the nitty-gritty of Kevlar offers insight into its essential role in modern technology and everyday life.
Prelims to Kevlar
Kevlar is more than just a name in the realm of materials science; it is a benchmark of strength and innovation. The introduction of Kevlar into this article sets the stage for an in-depth examination of a material that has transformed industries and influenced the development of various applications. Its significance is rooted in its remarkable propertiesâan elusive blend of durability, lightweight design, and resistance to impacts. From body armor to aerospace components, the versatility of Kevlar is astonishing.
History and Development
Initial Purpose of Kevlar
Originally discovered by Stephanie Kwolek in the 1960s, the primary purpose of Kevlar was to create a more durable material for tires. At that time, scientists aimed for a solution to enhance the performance and lifespan of tires, which faced constant wear and tear on the road. The initial purpose not only paved the way for countless technological advancements but also demonstrated the potential of synthetic fibers in pushing boundaries.
The key characteristic of Kevlar's inception was its striking tensile strength, which made it a desirable choice for various applications. Initially viewed as a mere solution for tire performance, its unique features soon drew attention from military and aerospace fields, positioning Kevlar as a powerful contender in the protective gear market.
Despite its original focus, Kevlar's properties showed that its applications went far beyond what was initially imagined. However, the shift in perception brought about challengesâhow to tailor the material for different uses without compromising its fundamental strengths.
Evolution of Kevlar Technology
Since its launch, the journey of Kevlar has witnessed a rapid evolution in technology. Various modifications and improvements have made it adaptable for countless applications. As industries discovered new use cases, the technology behind Kevlar has evolved to enhance its performance.
The important aspect of this evolution lies in the development of specialized variants, each serving distinct purposes. Today's Kevlar comes in numerous grades, each carefully crafted to meet specific requirements like weight, flexibility, and resistance to environmental factors.
A notable unique feature is the introduction of Kevlar blends, which combine it with other materials to maximize functionality. While this advancement has resulted in a more versatile product lineup, it also raises questions about consistency and performance standards across different applications.
Chemical Composition
Polymeric Nature
Delving into the chemical composition, Kevlar is predominantly a polymer, specifically an aramid fiber. Its polymeric nature imparts not only strength but also resilience against heat and chemical degradation. This pivotal characteristic makes Kevlar stand out in comparison to natural fibers or standard synthetics.
The beneficial aspect of this polymeric structure is its ability to maintain integrity under stress and various conditions. For applications requiring durability, this quality cannot be overstated. However, a lurking disadvantage is the complexity of production, involving specific conditions to create these polymer chains effectively.
Unique Molecular Structure
A defining element of Kevlar is its unique molecular structure, which sets it apart from other fibers. Structured in a linear form, the alignment of the molecules in Kevlar allows it to be incredibly strong and resistant to tensile forces. This molecular configuration is essential for maintaining the material's performance over time.
What makes this structure particularly commendable is its contribution to Kevlar's lightweight natureâan essential quality, especially in applications ranging from sports to aerospace. However, along with its strengths, the molecular structure also presents challenges; working with Kevlar can be more intricate, requiring specialized manufacturing processes to preserve its benefits.
"Kevlarâs unique molecular structure makes it one of the leading materials used in protective gear, showcasing a remarkable balance of strength and weight."
Through exploring the history, development, and chemical composition of Kevlar, readers can appreciate how this innovative fiber has established its place across diverse industries. As we transition into discussing its mechanical properties, the implications of these attributes on real-world applications become increasingly evident.
Mechanical Properties of Kevlar
The mechanical properties of Kevlar are vital to understanding why this synthetic fiber has become synonymous with strength and durability. These properties dictate how the material performs under stress, significantly impacting its applications across various industries. In a world where safety and efficiency are paramount, knowing what makes Kevlar tick can have transformative implications for everything from personal protective equipment to automotive innovation.
Tensile Strength
Comparison with Steel
When comparing the tensile strength of Kevlar to that of steel, it's essential to recognize that while steel is often seen as the heavyweight champion in strength, Kevlar is not far behind, offering a strength-to-weight ratio that is hard to ignore. Kevlar can resist breaking under tension when weighed against steel, making it a popular, lightweight choice for many applications.
One standout characteristic is that Kevlar can possess five times the tensile strength of steel at the same weight. This quality means that, for similar applications, Kevlar can provide effective resistance without adding bulk. The unique features in the molecular structure of Kevlar contribute to its chain-like formation, allowing it to distribute loads effectively, unlike steel which relies on its mass. While steel is extensively used in construction and heavy machinery, Kevlarâs lightweight nature presents a unique edge, particularly in fields where reduced weight means enhanced mobility. However, steel can withstand high temperatures better than Kevlar, a consideration worth evaluating.
Importance in Applications
The importance of tensile strength is paramount in applications where failure under load could lead to catastrophic consequences. In body armor, for example, itâs crucial that the material used is not only lightweight but can also absorb and disperse energy efficiently. With Kevlar, you get precisely that.
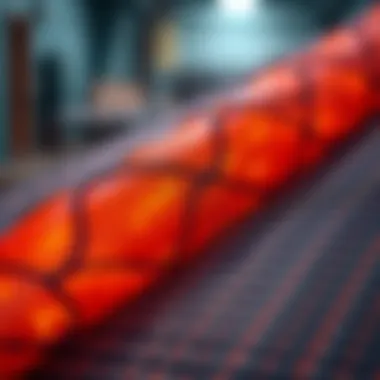
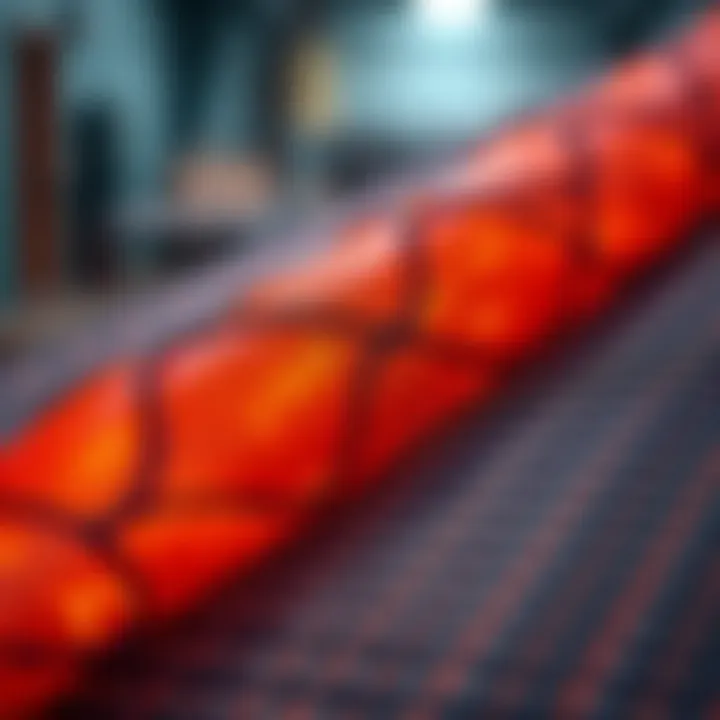
This key characteristic offers a dual advantageâprotection without compromising agility. Itâs also important to point out that Kevlar maintains its integrity even when subjected to extreme conditions, so it remains a pinnacle choice for tactical gear.
The downside? Kevlar can be pricier than other materials, which may deter budget-conscious productions. Still, the investment often pays off in performance and safety.
Impact Resistance
Ballistic Protection
Impact resistance is a hallmark feature of Kevlar and primarily drives its widespread use in ballistic protection. The ability of Kevlar to absorb shock and disperse impact makes it a leading candidate for use in bulletproof vests and armor systems. Its layered composition effectively turns what would be a devastating impact into a mere jolt, shielding the wearer from harm.
The character of this setup allows for the use of multiple layers of Kevlar, which provides additional protection against various threats. The ability to customize thickness and material orientation gives manufacturers flexibility in how the final product can perform under extreme conditions. Additionally, Kevlar's lightweight nature, combined with its robustness, means users can often wear it comfortably for extended periods, especially important for military and law enforcement personnel.
Yet, while Kevlar excels at stopping bullets, it won't hold up against knives very well, making it imperative to assess the specific threats being faced when selecting materials.
Applications in Sports Gear
In the realm of sports gear, the impact resistance of Kevlar brings another layer of advantage. Whether itâs used in protective pads, helmets, or even footwear, this capability helps athletes minimize injuries during high-impact activities.
A major highlight of this application is how it blends safety with performance. For instance, Kevlar-reinforced athletic gear can absorb shock while enabling the wearer to maintain speed and agilityâtwo traits crucial for success in competitive sports.
Unique features, like its ability to remain flexible while providing hard-hitting resistance, set Kevlar apart when compared to traditional materials. However, sports gear incorporating Kevlar tends to come at a higher price point, which may discourage some consumers.
"The strength of Kevlar lies not just in its physical properties but in the peace of mind it provides, whether on the battlefield or the field of play."
In summation, the mechanical properties of Kevlar position it as a game-changer across multiple industries, superbly combining tensile strength and impact resistance to forge safer and more reliable products. As advancements continue, the future will likely unveil even more innovative applications of this remarkable material.
Production Techniques
The production methods for Kevlar are pivotal to its overall performance and application versatility. Understanding how Kevlar is manufactured provides insights into the characteristics that make it a standout material in various fieldsâfrom military applications to consumer products. The processes involved directly affect the strength, flexibility, and durability of the fibers, ultimately influencing how they will be utilized in the real world.
Manufacturing Process
Polymerization Methods
The polymerization of Kevlar involves several approaches, but the most common is solution polymerization. In this method, polymer chains form through a process triggered by chemical reactions in a solvent. This technique is notable for its ability to produce high-durability fibers that have superb tensile strength; this is a key characteristic making it popular for high-performance applications.
One unique feature of solution polymerization is that it allows for a controlled environment. By adjusting the temperature and concentration of the components, manufacturers can achieve a specific molecular weight and distribution in the Kevlar fibers. These properties enhance performance attributes, increasing the fiber's resistance to abrasion and fatigue.
However, there are some downsides. The chemicals involved can generate considerable waste, raising environmental concerns. Additionally, this method may involve more complex safety measures due to the solvents used, which can present health risks if not properly managed.
Spinning Techniques
Once polymerized, the next step is the spinning of the Kevlar fibers. This involves drawing the polymer solution into fine strands. A prominent technique here is wet spinning, where the solution is extruded into a coagulation bath, causing the fibers to solidify. The key characteristic of spinning techniques is that they significantly influence the fiber's orientation and tensile properties, making the choice of spinning method crucial in determining the final product's characteristics.
A distinct feature of wet spinning is its ability to create fibers with very high alignment of molecules, which enhances tensile strength and elasticity. This method produces fibers that not only excel in strength applications but can also offer a degree of flexibility, allowing for incorporation into various productsâranging from protective wear to automotive components.
While wet spinning has its advantages, itâs also worth mentioning that it requires careful management of the coagulation bath and finishing processes to ensure uniform quality and performance.
Quality Control Measures
Quality control is essential in the production of Kevlar, ensuring that each batch meets stringent standards that facilitate its application in critical fields where failure is not an option.
Testing for Strength
The testing for strength is a cornerstone of quality assurance in Kevlar production. This process evaluates a fiberâs resistance to breaking under tension, crucial for applications such as body armor and aerospace components. The standard methods used, like tensile tests, involve applying loads until the material fails, measuring how much force it can withstand per unit area.
The uniqueness of strength testing lies in its attention to the fiber's molecular structure, revealing how manufacturing processes have affected its performance characteristics. As a result, the rigor applied in strength testing ensures that products made from Kevlar will perform reliably in demanding environments.
Despite its benefits, this rigorous testing can be time-consuming and may require additional costs to ensure compliance with safety standards.
Color and Texture Standardization
In addition to strength, color and texture standardization plays a vital role in the appeal and functionality of Kevlar products. Color consistency is crucial for aesthetic purposes, while texture can impact performance characteristics like grip and flexibility. Standardization processes ensure that each batch produced meets specific criteria for these attributes.
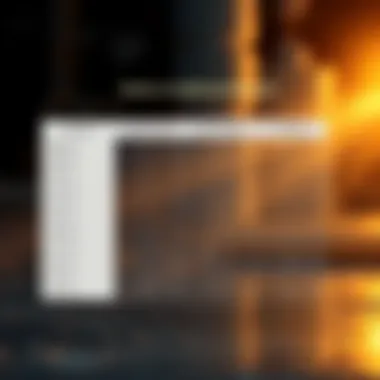
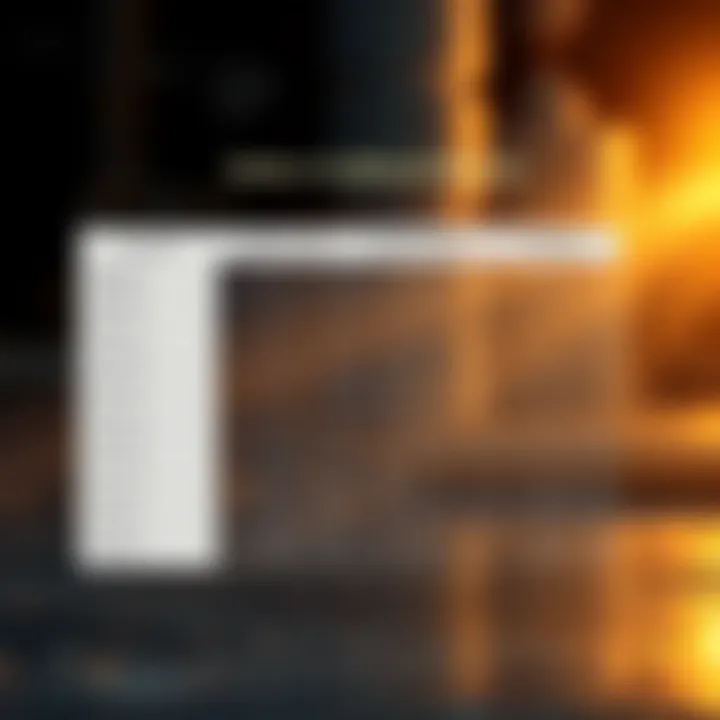
The notable aspect of this standardization is the way it enhances the marketability of goods made from Kevlar, making it easier for manufacturers to cater to varied consumer preferences while maintaining high performance standards.
On the flip side, maintaining consistent batches may require added resources and precise tracking through production, which could complicate the manufacturing process and drive up costs.
âEvery step in the production stages of Kevlar must be handled with precision; it's not just about making a strong material, but also making one that can be trusted in every application."
Each of these production techniques illustrates the complex landscape of creating Kevlar and sets the stage for its numerous applications in modern society.
Applications of Kevlar
Kevlar, a synthetic fiber renowned for its exceptional strength-to-weight ratio, finds its way into various crucial sectors. The importance of its applications underlines not only the versatility of the material but also its potential to revolutionize industries aiming for safety, durability, and efficiency. In this section, we will dissect how Kevlar is employed across military and law enforcement, automotive, aerospace, and consumer products, highlighting the specific characteristics and unique features that make it indispensable in these fields.
Military and Law Enforcement
Body Armor
Body armor made from Kevlar represents a significant advancement in personal protection. This type of armor excels in withstanding ballistic impacts, which is vital for law enforcement and military personnel. The key characteristic that sets Kevlar apart is its ability to absorb and disperse energy from projectiles, making it a beneficial choice in life-or-death situations. The unique feature of Kevlar body armor lies in its lightweight construction. Compared to metal armor, it offers considerable mobility without sacrificing protection. This advantage is crucial, as officers and soldiers often have to navigate challenging environments. However, while Kevlar provides impressive protection, it does have limitations in terms of puncture resistance and may require additional materials for maximum efficacy in certain contexts.
Tactical Gear Innovations
Innovations in tactical gear utilizing Kevlar have transformed how military and police forces operate. This gear includes vests, helmets, and other accessories designed to enhance protection and functionality. The notable characteristic of tactical gear made with Kevlar is its integrated flexibility, allowing for ease of movement during operations. This adaptability enhances user experience, making it a popular choice among professionals in high-stress environments. The unique feature of tactical gear innovations is their capacity to blend protection with practical elements, such as storage options and lightweight design. Nevertheless, a consideration worth mentioning is the cost, as such innovations tend to be pricier than standard gear, potentially limiting accessibility for smaller operations.
Automotive Industry
Tire Reinforcement
In the automotive world, Kevlar's ability to reinforce tires showcases its unparalleled significance. The application of Kevlar in tires specifically addresses the need for durability and reliability under high-pressure situations. Kevlar enhances tires' resistance to punctures and abrasions, making them a sound choice for both performance and safety purposes. A key characteristic is its weight-saving potential, which contributes to improved fuel economy by reducing overall vehicle weight. The unique feature of Kevlar-reinforced tires is the increased lifespan, which makes them a valuable long-term investment for consumers. However, the downside might be the higher initial purchase price compared to conventional tires, which could deter some buyers.
Composite Materials in Cars
Kevlar is increasingly incorporated in composite materials used in car manufacturing, targeting aspects from safety to performance. This application is particularly vital as car manufacturers look to reduce weight without compromising structural integrity. The unmistakable characteristic of Kevlar composites is their enhanced impact resistance, crucial for vehicle safety during collisions. Its lightness also aids in improving fuel efficiency, a significant benefit to eco-conscious consumers. The unique feature of using Kevlar in composites involves its role in driving automotive innovations forward. That said, the integration process can be complex and may increase production times, presenting challenges for manufacturers aiming for speedy delivery.
Aerospace Applications
Lightweight Structural Components
In aerospace, the use of Kevlar in lightweight structural components cannot be overstated. By reducing weight, Kevlar helps aircraft achieve better fuel efficiency and operational performance. The primary characteristic here is its remarkable strength-to-weight ratio, which allows for the design of components that are both sturdy and light. This unique feature extends the range and payload capacity of aircraft, essential in commercial and military aviation alike. However, a disadvantage to consider is the higher costs associated with composite materials, which can impact overall production budgets.
Fuel Efficiency Improvements
Kevlar's integration into aviation highlights its potential for fuel efficiency improvements. By utilizing lightweight materials, aircraft require less energy to operate, translating into lower fuel consumption. A significant characteristic is the environmental sustainability aspect, as reducing fuel usage diminishes emissions. The unique advantage of these improvements not only supports operational savings but also adheres to growing regulatory requirements for greener technologies. Conversely, the initial investment in research and development can be high, which might deter some companies from adopting these innovations right away.
Consumer Products
Protective Clothing
Protective clothing featuring Kevlar is becoming increasingly prevalent in various sectors, from construction to healthcare. This clothing is designed to safeguard the wearer against cuts, abrasions, and other hazards. The key characteristic of Kevlar in protective clothing is its superior resistance to cuts and impacts, which is essential for professionals in risky environments. One unique feature is the layering technology, allowing for versatility in design while maintaining high safety standards. Still, there is a trade-off between comfort and protection, as the thickness of Kevlar can sometimes restrict mobility in certain designs.
High-Performance Sporting Goods
In the realm of sporting goods, Kevlar is making waves through its incorporation in high-performance equipment. From protective gear for cyclists to performance-enhancing accessories for athletes, Kevlar plays a pivotal role. The key characteristic of Kevlar in sporting goods is its durability, leading to longer-lasting products that withstand the rigors of intense physical activity. The unique feature of high-performance sporting goods made with Kevlar involves their ability to enhance user experiences without compromising safety. However, these products can be costly, which may limit their accessibility to recreational athletes.
Environmental Considerations
In considering the broader implications of Kevlar, we can't overlook the environmental factors associated with its production and usage. Understanding these aspects is crucial, as they not only impact the sustainability of the material itself but also influence public perception and regulatory standards. The material's inherent advantages, like strength and durability, often come at a cost to the environment. This section discusses two pivotal challenges: sustainability and eco-friendly innovations in production.
Sustainability Challenges
Chemical Waste Management
When delving into the realm of Kevlar's production, chemical waste management stands out as a significant challenge. This facet encompasses the methods employed to handle, treat, and properly dispose of the by-products generated during the synthesis of Kevlar. Since Kevlar is made from complex chemical processes, it can lead to hazardous waste if not managed effectively.

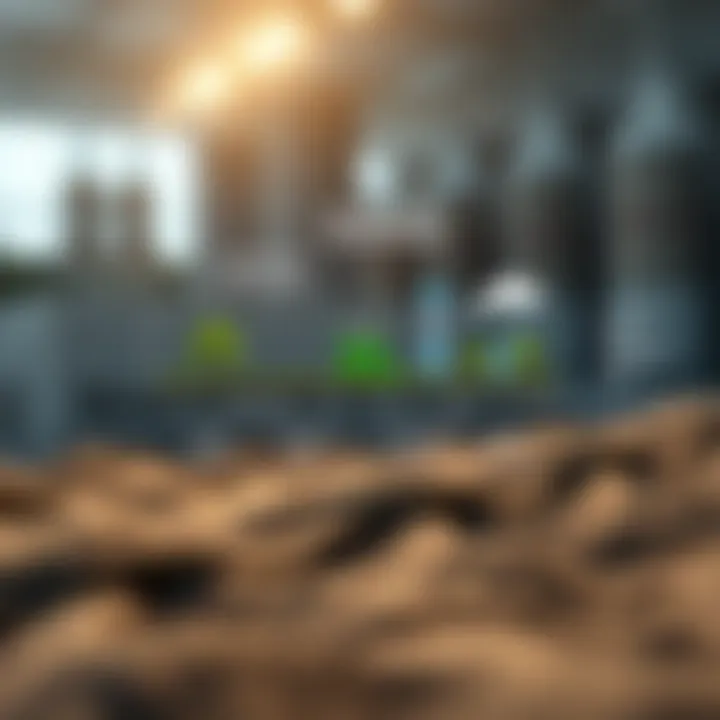
One key characteristic of chemical waste management is its responsibility towards reducing pollutants. Proper management practices are not just about compliance; they are an investment in public health. Poor waste management can result in toxic leaks and environmental contamination, which can have dire long-term consequences.
While some might argue that the existing methods are beneficial due to their ability to minimize immediate risks, their effectiveness is often hampered by insufficient technology or regulatory oversight. It's a balancing act, where the focus should be on advancing treatment methods while ideally seeking ways to reduce waste production from the start.
Recycling Limitations
Turning our attention to the aspect of recycling limitations, this brings to light the unfortunate reality that Kevlar is not easily recyclable. This emerging issue substantially contributes to environmental degradation. Although recycling efforts are widely advocated for various materials, Kevlarâs unique chemical structure makes it particularly challenging to repurpose.
A defining trait of recycling limitations is its feasibility. On one hand, recycling is considered a cornerstone in the movement towards sustainable practices. On the other hand, the intricacies involved in reprocessing Kevlar have made it less popular as a candidate for such initiatives. Many would prefer to simply discard rather than deal with the complex separation processes.
The advantages of recycling are numerous, including resource conservation and reduced landfill impact. However, if the recycling solutions are out of reach technologically or economically, it often leads industries to discard the material, thus perpetuating wastefulness.
Innovations in Eco-friendly Materials
Amidst these challenges, there lies a silver lining in the form of eco-friendly innovations. These are not merely the latest buzzwords but a fundamental shift in how materials like Kevlar are being reimagined.
Biodegradable Alternatives
When we explore biodegradable alternatives, we uncover a promising pathway for reducing the environmental footprint of materials traditionally thought to be non-disposable. These alternatives aim to mimic the high performance of Kevlar while naturally breaking down after their useful life.
A key aspect here is adaptability; although biodegradable options may not yet match all properties of Kevlar, advancements continue to close this gap. They offer a blend of functionality and environmental consideration, which is an appealing proposition moving forward.
Yet, there are unique challenges as well. For instance, durability tends to be a concern. While these alternatives may decompose over time, ensuring they can withstand comparable stresses before this decomposition is essential for practical applications.
Research on Renewable Resources
Finally, research on renewable resources paints a hopeful future for materials like Kevlar. This area delves into the utilization of sustainably sourced materials, reducing dependence on fossil fuels or petrochemicals, which have significant environmental impacts.
The key characteristic of this research is its focus on scalability. Renewable materials are not just experimental; they aim for mass adoption and integration into existing production lines, thereby influencing the market significantly. However, there are difficulties in establishing the infrastructure required to transition from traditional to renewable sources.
The promise of renewable resources lies in their potential to revolutionize how we view high-performance materials, moving from a linear economy to a circular one, where materials are reused and repurposed efficiently. This transition can offer both environmental and economic benefits if effectively implemented.
"Innovations in eco-friendly materials give us hope! They can help repair the mistakes of the past while offering better solutions for the future."
Through this lens of environmental considerations, we see that Kevlar, like many materials, is at a crossroads. The journey to sustainable practices involves tackling the hurdles of waste management and recycling while fostering innovations that may redefine our relationship with high-strength materials.
Future of Kevlar Technology
The world of Kevlar technology is on the brink of significant transformations. As industries are on a quest for materials that offer enhanced functionality, Kevlar is finding itself at the forefront of innovation. Discussing the future of Kevlar technology holds much significance, as it examines not just the materialâs current applications, but also what lies ahead.
Advancements in Fiber Technology
Smart Kevlar Fabrics
One of the remarkable advancements is the development of Smart Kevlar Fabrics. These fabrics seamlessly combine traditional Kevlar strength with smart technology, allowing for a dynamic interaction with their environment. The key characteristic of these fabrics lies in their ability to monitor various conditions, such as temperature and body movements. This adaptability makes them an attractive option for various applications, especially in protective gear.
For example, imagine a soldier's uniform equipped with sensors that can detect stress levels or environmental risks. This unique feature of Smart Kevlar could lead to real-time feedback on the wearerâs condition, promoting safety and efficiency. While the upsides are plenty, adaptability comes with challenges. The integration of technology can increase production costs, and there's always the need to ensure that the smart components do not compromise the fundamental durability of the Kevlar fibers itself.
Nano-enhanced Properties
Another area that shows great promise is Nano-enhanced Properties of Kevlar. This process involves infusing Kevlar fibers with nanoparticles that can significantly improve their performance characteristics. The key aspect here is the increased resilience and reduced weight. This makes it suitable for applications needing high strength without adding extra bulk. It's not just about being lightweight; the enhanced properties also improve the overall impact resistance, giving a layer of safety that standard Kevlar might lack.
The unique feature of using nanotechnology in Kevlar means it can potentially repel water or resist certain chemicals, expanding its applications into industries like construction and chemical handling. Nonetheless, there are concerns regarding the long-term effects of these nanoparticles both on human health and the environment, which need careful investigation as the materials are further developed.
Potential New Applications
Space Exploration Gear
A fascinating aspect to consider is the potential for Space Exploration Gear made from Kevlar. As missions to outer space become more ambitious, the materials used in spacecraft need to withstand extreme conditions. Kevlarâs lightweight, yet high-strength properties make it an ideal choice for protective gear designed for astronauts. The key characteristic here is the ability to combine safety with flexibility, allowing astronauts to move freely while being shielded from dangers such as micrometeoroid impacts.
Additionally, Kevlar's thermal stability can help manage heat exposure, creating a favorable environment inside space suits. Despite these advantages, the challenge remains that the gear must also be comfortable for prolonged usage. Finding a balance between protection and wearability will be crucial as developers push the boundaries of what is possible in space exploration.
Medical Innovations
Shifting focus to another promising area, Medical Innovations involving Kevlar highlight its versatility. In the medical field, Kevlarâs unique characteristics could be utilized for creating durable, yet lightweight prosthetics or even in surgical kits where enhanced strength is crucial. The key characteristic here is the combination of lightness and resilience, which helps in not only enhancing performance but also reducing fatigue for the user over time.
Moreover, 3D-printing technology is paving the way for customized solutions that incorporate Kevlar, resulting in tailored medical devices for individual patients. The unique feature of using Kevlar-based materials in the medical sector could help reduce wear and tear, making these products more dependable long-term. However, cost and regulatory hurdles can present challenges in bringing these innovations to widespread use.
In summary, the future of Kevlar technology holds much promise, enabling advancements across numerous sectors. The ongoing development and exploration of smart fabrics and nano-enhanced properties unlock the potential for new and improved applications beyond our current understanding.