Understanding Semiconductor Defect Inspection
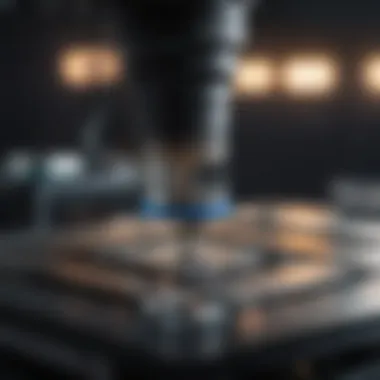
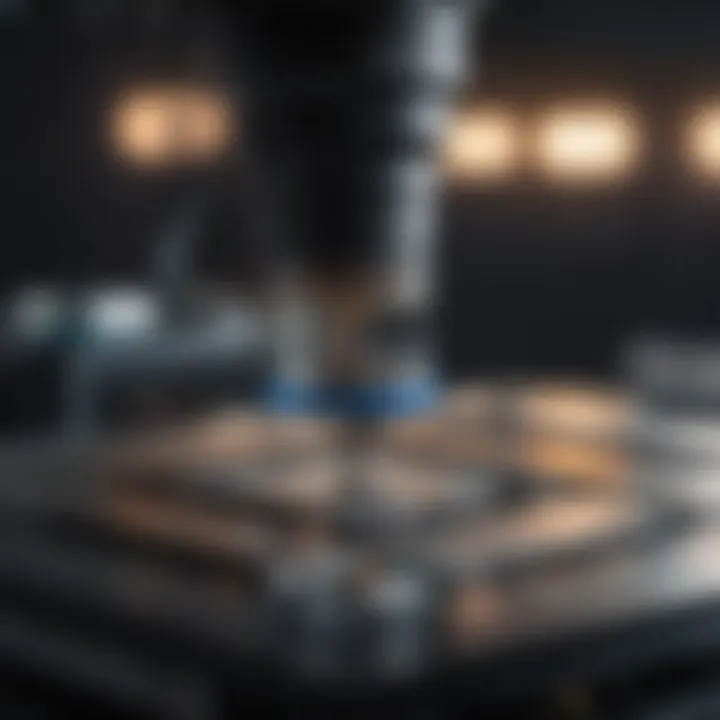
Intro
Defect inspection in semiconductor manufacturing is a critical process. It dictates the functionality and reliability of the devices we rely on daily. Defects can lead to failures, affecting everything from consumer electronics to vital applications in healthcare and automotive industries. Understanding how defects are identified, categorized, and managed is essential for anyone involved in semiconductor production or research.
The landscape of semiconductor defect inspection encompasses various methodologies and technologies. Each serves a unique role in ensuring the performance and quality of semiconductor components. As technology evolves, so do the techniques for identifying and addressing these defects.
Furthermore, the implications of defect presence cannot be understated. With the increasing miniaturization of devices, a single defect can compromise a chip’s effectiveness. Hence, engineers and researchers must navigate a complex environment where precision is paramount, and the cost of errors can be significant.
In this article, we will explore the methodologies employed in defect detection, the significance of these processes, and the future challenges facing engineers in semiconductor manufacturing. We will also touch on the innovative imaging techniques that hold promise for enhancing inspection accuracy and efficiency.
Research Overview
As we delve deeper into semiconductor defect inspection, it is crucial to consider the research landscape surrounding this topic. Understanding the methodological approaches used and their significance helps in grasping why defect inspection matters in semiconductor manufacturing.
Methodological Approaches
There are several approaches to defect inspection in the semiconductor industry. The main techniques include:
- Optical Inspection: Uses light to detect defects on the surface of semiconductor materials. It’s non-invasive and widely adopted.
- Electron Beam Inspection: Provides high-resolution imaging at a microscopic level. This method is effective for locating minute defects but can be time-consuming.
- X-ray Inspection: Effective for internal inspection, allowing for non-destructive analysis of semiconductor devices. This method is crucial for packages where internal defects may occur.
These methodologies often need to be combined to improve detection rates. Using multiple methods allows for a more thorough inspection, which is essential in modern semiconductor manufacturing where quality control is paramount.
Significance and Implications
The implications of effective defect inspection extend beyond production quality. They have a direct impact on:
- Device Performance: A defect in a semiconductor can impair its functionality, leading to potential device failures.
- Manufacturing Costs: Early detection of defects can dramatically reduce the cost associated with defective products. It can also save time in the manufacturing process.
- Market Reputation: The semiconductor industry is competitive. Companies that consistently produce high-quality devices gain a better reputation, leading to increased customer trust and loyalty.
Defect inspection is not merely a step in the manufacturing process; it is a cornerstone of quality assurance that shapes the future of semiconductor technology.
Current Trends in Science
As we navigate the current landscape of semiconductor defect inspection, it becomes evident that innovation plays a vital role in enhancing inspection methodologies. New techniques and tools are emerging to improve detection capabilities.
Innovative Techniques and Tools
Some current trends include:
- Machine Learning Algorithms: Implementing AI to analyze inspection data can help in the fast and accurate identification of defects. Machine learning can find patterns that may be missed by traditional methods.
- 3D Inspection Technologies: Advanced imaging techniques including 3D surface profiling are developed to enhance defect detection significantly.
These innovations not only increase the efficiency of inspections but also help in predictive analysis for future manufacturing processes, enabling proactive rather than reactive measures.
Interdisciplinary Connections
The intersection of different scientific disciplines is shaping the future of semiconductor defect inspection. Fields such as:
- Materials Science: Plays a role in understanding how different materials behave under various manufacturing conditions, influencing defect types and frequencies.
- Physics and Engineering: Informs new technologies and methods for defect detection and analysis.
Integrating diverse knowledge sets amplifies the potential for breakthroughs in defect inspection, leading to improved methodologies and better device reliability.
In summary, as we explore semiconductor defect inspection, one must appreciate its complexity and significance. Each inspection method, current trend, and interdisciplinary connection contributes to the pursuit of higher quality in semiconductor manufacturing.
Intro to Semiconductor Defect Inspection
In the semiconductor industry, defect inspection carries immense importance. As the complexity of semiconductor devices increases, the need for meticulous inspection processes becomes crucial. Defects can arise at any stage of semiconductor manufacturing, hence a robust defect detection mechanism is indispensable.
The inspection helps identify discrepancies that may threaten both the performance and reliability of semiconductor components. Early detection of defects allows engineers to rectify issues before mass production, mitigating costly repercussions later on. This proactive approach not only enhances product quality but also optimizes manufacturing efficiency.
Importance of Methods and Technologies
Defect inspection methods leverage various technologies, ranging from optical systems to advanced X-ray imaging. Each technology offers distinct benefits and challenges. For example, optical inspection is effective for surface defect detection but may struggle with internal structural flaws. Understanding these methods ensures that semiconductor manufacturers select the most appropriate techniques for their specific needs.
Moreover, integrating machine learning algorithms into defect inspection facilitates faster processing of data and improves accuracy in identifying anomalies. These advancements in technology transform the landscape of semiconductor manufacturing, making it possible to handle increasingly complex designs.
Considerations in Defect Inspection
It is also important to navigate the considerations surrounding defect inspection. The decision-making process involves weighing sensitivity against specificity. Inspections must be finely tuned to avoid false positives and false negatives. Furthermore, engineers face time restrictions that compel them to develop efficient protocols, ensuring inspections do not impede production timelines.
The Importance of Defect Inspection in Semiconductor Manufacturing
The semiconductor industry is a cornerstone of modern technology, providing the critical components found in countless electronic devices. As the complexity of these components increases, so does the necessity for rigorous defect inspection. Defect inspection plays a vital role in ensuring the quality and reliability of semiconductor devices during manufacturing. It is essential not only for product success but also for maintaining the reputation and financial stability of manufacturers.
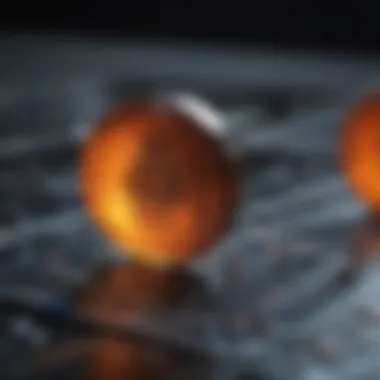
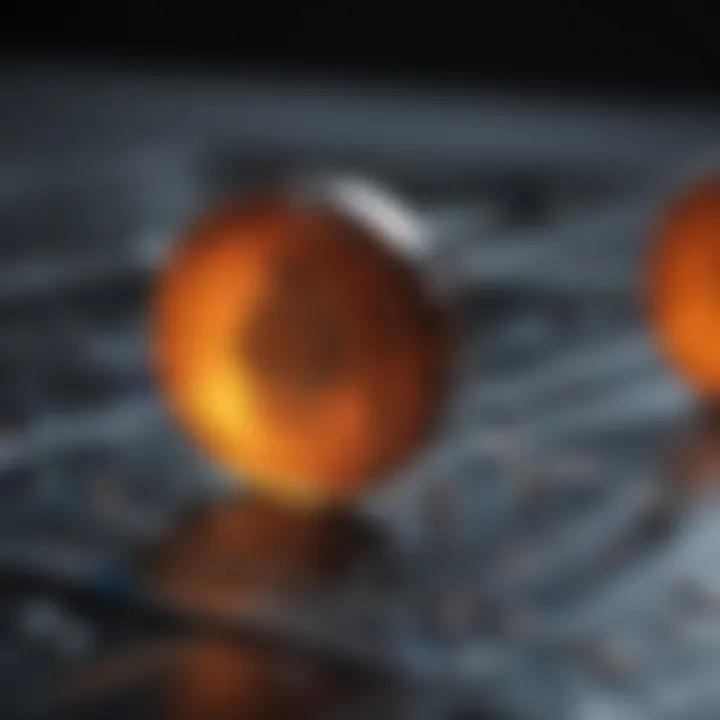
One significant benefit of defect inspection is its direct influence on yield rates. Higher yield rates mean fewer defective products, leading to reduced material waste and lower production costs. In a field where profit margins can be razor-thin, efficient inspection processes can significantly enhance profitability. Moreover, identifying defects early in the production process can prevent costly rework or scrap of entire batches of semiconductors.
Defect inspection also safeguards device reliability. Defects, even minute ones, can lead to catastrophic failures in high-stakes applications, such as in aerospace or medical devices. A compromised semiconductor can impact not just performance but also user safety. Thus, rigorous inspection protocols are critical to meet stringent industry standards and regulations.
Furthermore, the evolving landscape of technology presents new challenges in semiconductor manufacturing. The push for smaller, more powerful chips with increased functionality requires advanced inspection techniques. As features shrink to nanometer scales, the risk of undetected defects rises. Inspections need to adapt swiftly to these changes, and the importance of staying ahead cannot be overstated.
In addition to ensuring product quality, defect inspection plays a strategic role in competition. Companies that prioritize defect detection can differentiate themselves in a crowded market. By demonstrating superior quality control, they can build trust with customers and stakeholders, potentially capturing a larger market share.
"Defect inspection is not just a quality control measure; it is an investment in the future of technology."
Defect inspection methods have evolved, incorporating innovations like machine learning and automated systems, which enhance both the speed and accuracy of detection. This integration of technology is critical in managing the complexities and volume of modern semiconductor manufacturing.
Types of Defects in Semiconductors
Understanding the various types of defects in semiconductors is crucial to improving device performance and manufacturing efficiency. These defects can arise from numerous sources during the production process, including material impurities, fabrication errors, and environmental factors. Identifying and categorizing these defects enables engineers to implement effective inspection protocols and ensure high-quality semiconductor devices.
The following subsections provide a detailed overview of the three primary types of defects that can affect semiconductors: structural, electrical, and surface defects.
Structural Defects
Structural defects refer to irregularities in the physical arrangement of atoms within a semiconductor material. These defects can significantly affect the electronic properties of the material, leading to variations in conductivity and potentially decreasing the overall reliability of semiconductor devices. Common types of structural defects include dislocations, vacancies, and grain boundaries.
Dislocations occur when there is a misalignment in the crystal lattice structure. They can trap charge carriers, which may hinder the performance of the device. Vacancies arise when atoms are missing from their regular lattice positions, impacting the material's electrical characteristics. Grain boundaries, which are found where two crystal grains meet, can also introduce barriers to electron flow, affecting device efficiency.
Addressing structural defects typically involves advanced inspection techniques to accurately identify and analyze these anomalies. As a result, semiconductor manufacturers can reduce the occurrence of these defects and enhance the overall performance of their products.
Electrical Defects
Electrical defects are primarily concerned with how defects impact the electrical performance of semiconductor devices. These defects can lead to unwanted electrical characteristics, such as leakage currents or reduced switching speeds. Among the most common electrical defects are dopant fluctuations and interface traps.
Dopant fluctuations refer to variations in the distribution of dopants, which are used to modify the electrical properties of a semiconductor. These variations can lead to inconsistent conductivity within the material. Interface traps occur at the boundary between different materials, such as insulators and semiconductors. These traps can capture charge carriers and thereby affect device performance, contributing to issues like increased power consumption and reduced reliability.
Accurate detection and characterization of electrical defects are vital in semiconductor manufacturing. Implementing robust inspection methodologies ensures that electrical defects are addressed early in the production process, leading to more reliable semiconductor devices.
Surface Defects
Surface defects are irregularities that occur on the external layers of semiconductor materials. These defects can be particularly detrimental because they can directly affect how semiconductor devices interact with external environments. Common types of surface defects include cracks, pits, and contamination from foreign materials.
Cracks can propagate through the semiconductor, leading to catastrophic failures. Pits, often caused by chemical etching processes, can also create junctions that alter the electronic properties of the material. Additionally, contamination can introduce impurities that compromise device integrity.
To mitigate the impact of surface defects, regular inspections and cleanroom protocols are essential. Maintaining stringent cleanliness standards minimizes contamination risks and enhances device performance.
In summary, comprehending the various types of semiconductor defects is vital for improving the quality and reliability of electronic devices. By focusing on structural, electrical, and surface defects, engineers can develop better inspection methods. This proactive approach leads to the creation of efficient, high-quality semiconductor products.
Inspection Technologies
Inspection technologies play a crucial role in semiconductor manufacturing. They help ensure that devices function reliably and meet the high standards of quality expected in the industry. By utilizing various inspection methods, manufacturers can detect defects at different stages of production. This reduces waste, improves yield, and enhances overall device performance.
Optical Inspection
Optical inspection is one of the most common methods used in semiconductor defect inspection. It relies on visible light to detect surface defects and irregularities in semiconductor wafers and devices. This method can rapidly cover large areas, making it effective for high-volume production environments.
The main benefit of optical inspection is its speed. It can identify defects in real-time, allowing for immediate corrections during the manufacturing process. Moreover, modern systems are designed to provide high-resolution images that help engineers analyze defects accurately.
However, optical inspection is limited in its ability to detect subsurface defects. These types of defects may require additional inspection methods for comprehensive analysis.
Electron Beam Inspection
Electron beam inspection utilizes beams of electrons to analyze the surface of semiconductor materials. This technique offers a much higher resolution than optical methods, making it ideal for detecting even the smallest defects. The ability to achieve a resolution in the nanometer range allows engineers to scrutinize every detail of semiconductor structures.
Despite its advantages, electron beam inspection does come with some challenges. It can be slower than other methods, and the equipment is often more expensive. Additionally, the process may alter the sample being inspected, which can lead to potential errors in defect detection.
X-ray Inspection
X-ray inspection is another powerful tool in defect detection. This method is valuable for assessing the internal structures of semiconductor devices without damaging them. It is particularly effective for locating hidden defects, which can be critical in ensuring long-term reliability.
X-ray inspection provides valuable insights into complex assembly structures like flip-chip interconnections. This technology is also useful in identifying issues related to materials and bonding processes. However, like any technology, it has limitations, such as the need for considerable safety precautions and the requirement for specialized training for operators.
Atomic Force Microscopy
Atomic force microscopy (AFM) allows for incredibly detailed surface imaging and analysis at the atomic level. AFM operates by scanning a sharp probe over the surface to measure forces between the probe and the sample, providing topographical maps at a very fine resolution.

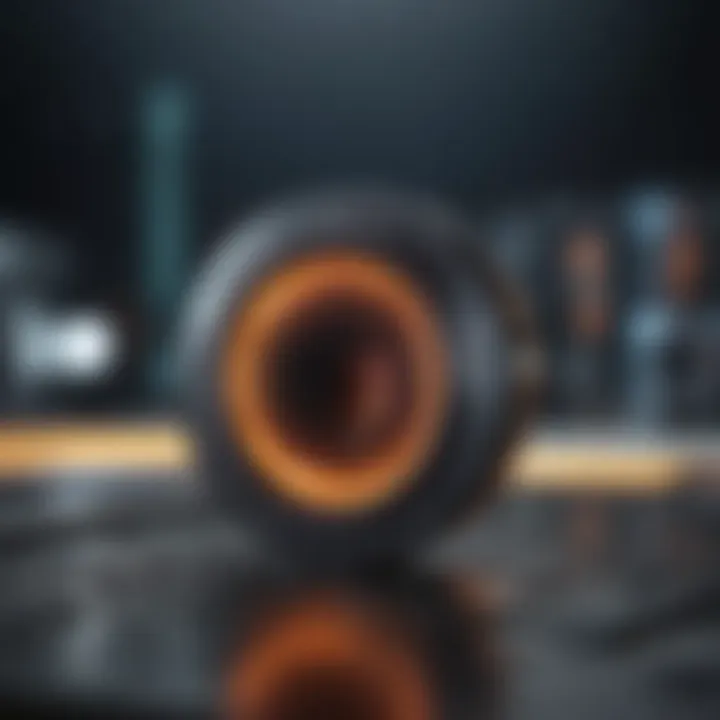
This technology is essential for understanding material properties, assessing surface roughness, and evaluating other physical characteristics of semiconductor materials. Although highly sensitive and precise, AFM is slower and often requires specialized sample preparation.
The Role of Machine Learning in Defect Detection
The integration of machine learning in defect detection marks a significant advancement in semiconductor inspection. As manufacturing processes become more complex and the dimensions of semiconductor devices shrink, traditional detection methods often struggle to keep pace. Machine learning algorithms provide a robust framework to enhance the detection process, offering better accuracy and efficiency.
Machine learning algorithms can analyze vast amounts of data from inspection systems. By training these systems with large datasets of defect characteristics and patterns, they learn to recognize anomalies more effectively. This learning ability is crucial because defects can vary greatly, and identifying them requires a nuanced understanding of these variations.
Benefits of Machine Learning in Defect Detection
- Increased Detection Rate: Machine learning can improve the detection rate of defects compared to manual methods. By leveraging previous data, algorithms can identify subtle flaws that human inspectors might overlook.
- Reduced Time for Inspection: Automated machine learning inspection systems can process images faster than manual inspections or traditional methods. This acceleration is particularly useful in high-volume manufacturing environments where speed is essential.
- Predictive Maintenance: Machine learning can also facilitate predictive maintenance protocols. By analyzing defect patterns over time, these systems can predict potential future defects, allowing for proactive measures before failures occur.
Considerations in Implementing Machine Learning
While machine learning offers notable advantages, its implementation is not without challenges. The following points must be considered:
- Data Quality: The effectiveness of machine learning algorithms depends on the quality of data supplied for training. Erroneous or insufficient data can lead to poor performance in defect detection.
- Integration with Existing Systems: Successfully integrating machine learning models with existing inspection technologies requires careful planning and resources. Compatibility between software solutions is critical to achieving seamless operations.
- Continuous Learning: The semiconductor manufacturing landscape is ever-evolving. Thus, machine learning models should be designed for continual updating to adapt to new defect types and manufacturing practices.
"Machine learning transforms defect detection from a static task into a dynamic process that evolves with production needs."
In summation, the role of machine learning in defect detection is transformative. It equips inspection systems with capabilities that not only enhance accuracy but also ensure efficiency in semiconductor manufacturing. As technology advances, the focus will likely shift towards refining these algorithms further to meet the increasing demands of the semiconductor industry. The potential for improved reliability and performance through machine learning in defect detection remains a crucial consideration for manufacturers looking to maintain a competitive edge.
Methodologies for Defect Inspection
In the realm of semiconductor production, the methodologies employed for defect inspection are crucial. They serve not only to identify faults but also to determine their implications for device performance. Understanding these methodologies allows for the optimization of production processes and ultimately enhances product reliability. The careful selection of inspection methods contributes to better yield, reduced costs, and improved market competitiveness. This section will explore key methodologies—manual inspection, automated systems, and statistical process control—and discuss their unique benefits and their roles in the broader scheme of defect management.
Manual Inspection Techniques
Manual inspection plays an important role in the semiconductor industry, despite the rapid evolution of technology. It often serves as an initial gate in the quality assurance process. Trained technicians rely on their experience and keen observation to identify visible defects on semiconductor wafers. This method has the advantage of facilitating the identification of anomalies that automated systems may overlook.
However, it is labor-intensive and prone to human error. Factors such as fatigue and subjective interpretation can significantly affect accuracy. Sometimes, inspectors might miss small defects that, while not immediately visible, can deteriorate device performance over time.
Implementing manual techniques requires careful consideration of personnel training and workflow management to maximize efficiency and reliability. In environments where precision is key, even small improvements in manual inspection can lead to substantial benefits.
Automated Inspection Systems
On the other hand, automated inspection systems bring a high level of consistency and efficiency to defect detection. Techniques such as optical inspection and electron beam inspection have made significant strides over recent years. These systems utilize advanced algorithms and imaging technology to detect defects at a much finer resolution than manual methods.
Automated systems can process a large number of wafers quickly, significantly reducing inspection time per unit. They also contribute to higher throughput and lower operational costs. Data collected through automated inspections can be used for predictive maintenance and continuous improvement initiatives.
Yet, they also present challenges. High initial setup costs can be a barrier for smaller manufacturers. Furthermore, although these systems are effective, they can sometimes produce false positives or negatives, necessitating secondary checks. Thus, the integration of automated inspection should be carefully balanced with the need for human oversight to ensure robust quality assurance.
Statistical Process Control in Inspections
Statistical process control (SPC) forms the backbone of many modern inspection methodologies. By applying statistical methods to measure and analyze variance in production processes, SPC helps identify trends and potential defects before they occur. This proactive approach aids manufacturers in maintaining the quality of semiconductor devices throughout the production cycle.
SPC involves the use of control charts, which provide visual insights into processes over time. This method allows for real-time monitoring, enabling prompt adjustments to be made when anomalies are detected. Moreover, sampling techniques in SPC make it possible to inspect only a fraction of the total output while still ensuring high levels of confidence regarding the overall quality.
Overall, methodologies for defect inspection are interconnected and essential for maintaining the integrity of semiconductor manufacturing. By combining manual techniques, automated systems, and statistical control, manufacturers can enhance their defect detection efforts, thereby producing reliable semiconductor devices that meet the stringent demands of today’s technology.
"Quality cannot be inspected into a product; it must be produced."
– William Edwards Deming
This critical reassessment of inspection methodologies helps manufacturers avoid costly mistakes and reinforces the significance of ongoing improvements in inspection processes.
Challenges in Defect Inspection
Defect inspection in semiconductor manufacturing is complex. Various challenges arise from the need for precision and reliability in detecting defects. Understanding these challenges is crucial, as they directly impact the quality of semiconductor devices. This section will delve into three primary challenges: high sensitivity and specificity requirements, the complexity of semiconductor structures, and processing time constraints.
High Sensitivity and Specificity Requirements
High sensitivity refers to the ability of an inspection system to detect even the smallest defects. In contrast, specificity focuses on correctly identifying genuine defects without false positives. Balancing these two elements is vital yet challenging.
- Sensitivity has to be high enough to catch tiny defects that can lead to device failures.
- Specificity must be equally robust to avoid misclassifying acceptable variations as defects.
Consequently, many inspection systems utilize advanced algorithms and machine learning techniques to improve their performance. However, as sensitivity increases, the risk of generating false positives also grows, prompting a need for ongoing refinement of the inspection processes.
Complexity of Semiconductor Structures
Semiconductors today have intricate designs with multiple layers. This complexity arises from modern demands for thinner chips and higher performance. Various factors contributing to this complexity include:
- Miniaturization: As features shrink, the margin for error diminishes. A defect in a nanometer scale can severely disrupt the chip’s functionality.
- Layered Structures: Multiple layers can obscure defects. Inspectors must ensure that inspections can penetrate these layers without damaging the chip.
- Material Variations: Different materials behave differently under electronic constraints, leading to varied defect types.
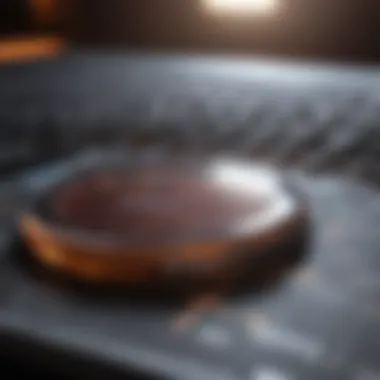
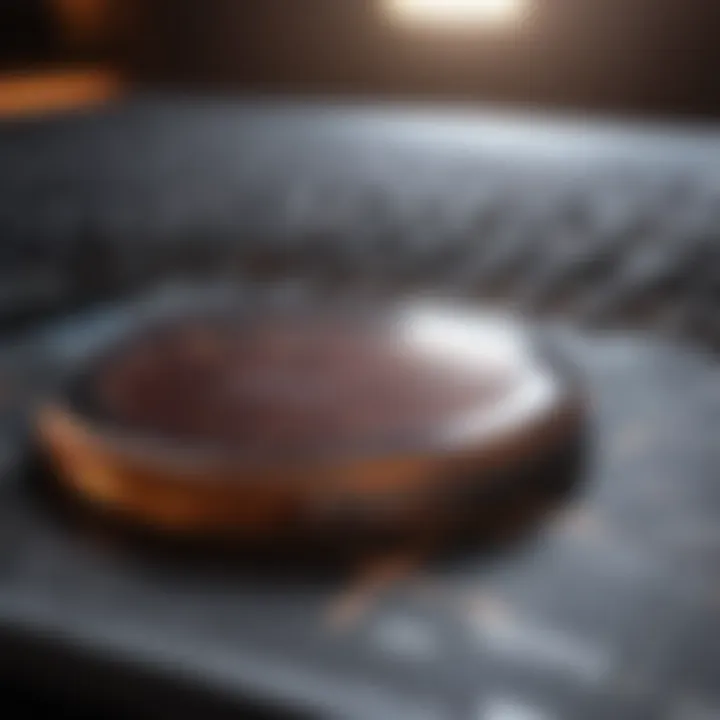
The monitoring technologies need constant upgrades to accommodate these variations. This evolution makes it difficult for inspectors to maintain an efficient and effective process, complicating defect identification further.
Processing Time Constraints
In manufacturing, time is a critical factor. Speed becomes essential in ensuring that production lines run smoothly. Delays due to defect inspection can lead to significant productivity losses. Particularly in high-volume manufacturing environments, processing time constraints can present several challenges:
- Inspection Speed Versus Accuracy: Rapid inspection methods may compromise accuracy, producing unacceptably high error rates.
- Integration with Production Flow: Inspection systems must integrate seamlessly into the production process to avoid bottlenecks.
- Real-Time Analysis: Many facilities strive for real-time analysis of defects, which increases the demand for faster processing capabilities.
In summary, the challenges in defect inspection are multifaceted. High sensitivity and specificity, the complexity of semiconductor structures, and time constraints all interplay. Each of these elements shapes the overall defect identification process, affecting product quality and production efficiency. > "Understanding and overcoming these challenges is imperative for advancing semiconductor manufacturing efficiency and reliability."
By addressing these issues, manufacturers can implement better inspection systems that ensure the production of high-quality semiconductor devices.
Impact of Defects on Device Performance
Understanding the impact of defects on device performance is crucial in the realm of semiconductor manufacturing. Defects can manifest in various forms, leading to substantial repercussions not only in the functionality of the devices but also in their reliability over time. They can result in diminished performance, increased failure rates, and ultimately, a loss of consumer trust in the products.
Key Elements of Defect Impact
The following points outline significant elements regarding defects and device performance:
- Performance Limitations: Defects can hinder a semiconductor's ability to function effectively. For example, electrical defects may result in increased resistance within circuits. This limitation can lead to slower operational speeds or reduced power efficiency.
- Increased Costs: When defects arise, additional costs are incurred during the manufacturing process. This includes the costs associated with rework, scrapping faulty devices, and enhanced inspection techniques needed for quality assurance.
- Market Competition: High-performance devices are essential for companies to maintain competitive advantage. The presence of defects can lead to inferior products that may be outperformed by competitors’ offerings.
The ramifications of neglected defects extend beyond mere performance issues. As devices become more integrated, the probability of complex interactions and subsequent issues increases.
Reliability Issues
Reliability is paramount in semiconductor devices. Defects directly compromise this reliability. When components fail prematurely, it can lead to catastrophic results, especially in critical applications like medical devices and automotive systems. A semiconductor’s ability to operate under specified conditions is often tested against its susceptibility to various defect types.
In many cases, defective components can degrade performance over time, leading to thermal cycling or increased stress which exacerbates faults. Regular reliability testing must evolve to accommodate emerging technologies and defect types.
Functional Failures
Functional failures represent some of the most significant consequences of defects. When defects exist, they may prevent devices from performing their intended function. For instance, structural defects could lead to complete device failure. This leads to consumer dissatisfaction, and negatively impacts brand reputation.
Moreover, the ramifications of functional failures extend into various industries. In telecommunications, defective chips could disrupt signal processing, while in computing, it could result in data loss or system crashes.
"Functional integrity is vital in ensuring that semiconductor devices operate as intended in their designated applications."
In summary, understanding the impact of defects on device performance allows manufacturers to implement more effective inspection and testing protocols. This vigilance is essential for maintaining quality standards and enhancing overall device reliability.
Future Directions in Defect Inspection Technology
The field of semiconductor defect inspection is evolving rapidly. This evolution is critical to improving the efficiency and reliability of the devices we rely on. With advancements in technology, new methods are emerging that enhance our capabilities in detecting defects. Future directions in defect inspection technology hold immense promise for overcoming the challenges faced in current processes. This section will address these upcoming trends, emphasizing three main areas: advancements in imaging techniques, integration of artificial intelligence, and sustainability considerations.
Advancements in Imaging Techniques
The core of defect inspection lies in the imaging techniques used to identify issues within semiconductor materials. Recent advancements in imaging technologies are set to fundamentally transform the industry. High-resolution imaging, such as used in Scanning Electron Microscopy (SEM) and Atomic Force Microscopy (AFM), provides unprecedented depth of detail. As these techniques improve, they allow for better identification of minuscule defects that were previously undetectable.
Moreover, the development of multi-modal imaging techniques is proving to be beneficial. Combining various imaging modalities, like X-ray and optical methods, enables a simultaneous view of different types of defects. This comprehensive approach allows engineers to make more informed decisions, thereby reducing the likelihood of error in the defect inspection process.
Integration of AI Technologies
Artificial intelligence is playing an increasingly essential role in semiconductor defect inspection technology. By implementing machine learning algorithms, the efficiency and accuracy of defect detection can rise significantly. AI systems can analyze vast datasets of defect information and automate the identification of patterns in defects. This automation reduces the reliance on traditional inspection methods that may miss subtle flaws.
Additionally, predictive analytics powered by AI can foresee potential defect occurrences based on historical data. This proactive approach allows for preventive measures to be taken, which is more cost-effective than addressing defects after they appear. Overall, the integration of AI technologies in defect inspection benefits organizations by increasing throughput and enhancing the reliability of semiconductor devices.
Sustainability Considerations
As industries move towards sustainability, semiconductor defect inspection is no exception. The implications of sustainable practices in defect inspection are profound. One focus is on minimizing waste generated during inspection processes. Advanced technologies can enhance the efficiency of inspections, reducing the number of failed devices and the consequent wastage of materials.
In addition, sustainable materials for inspection components are gaining attention. Developing eco-friendly imaging media and other inspection tools is a crucial step towards reducing the environmental impact of semiconductor manufacturing. Moreover, adopting more energy-efficient inspection systems can lead to lower overall energy consumption, aligning with global sustainability targets.
By focusing on sustainability, the semiconductor industry can lead by example while ensuring the longevity of its technology and market relevance.
Finale
The conclusion of this article emphasizes the crucial nature of semiconductor defect inspection in the broader context of manufacturing. Defect inspection is not merely a step in the fabrication process; it is a determinant of overall device performance and reliability.
Effective defect inspection methods contribute significantly to the quality assurance needed for semiconductor devices. These methods help identify and categorize defects that could impair functionality, thereby improving yield and reducing costs.
Additionally, as technology advances, the integration of methods such as machine learning and enhanced imaging techniques becomes vital. This integration helps address the challenges posed by increasingly complex semiconductor structures.
Key benefits of defect inspection include:
- Enhanced Reliability: By detecting defects early, manufacturers can ensure that devices operate as intended over their lifespan.
- Cost Efficiency: Early detection of defects helps prevent costly returns and repairs, ensuring a smoother manufacturing process.
- Improved Performance: Ensuring that defects are minimized aids in maintaining the operational integrity of semiconductor devices.
"Investing in robust inspection methods not only mitigates risks but also ensures that the technology developed can meet future demands."
Consideration of sustainability in defect inspection practices is also paramount. As the industry moves towards more environmentally friendly processes, integrating sustainable practices into inspections will likely play a key role. It is valid to suggest that the pursuit of defect inspection improvements is an ongoing endeavor that requires collaboration between engineers, researchers, and manufacturers.
Overall, this article reveals that understanding the implications of semiconductor defect inspection is essential for anyone invested in the future of electronics. The continuing evolution in methodologies not only paves the way for innovation but also enhances the confidence in semiconductor technologies that power various modern applications.