Strain Gauge Applications in Crack Monitoring
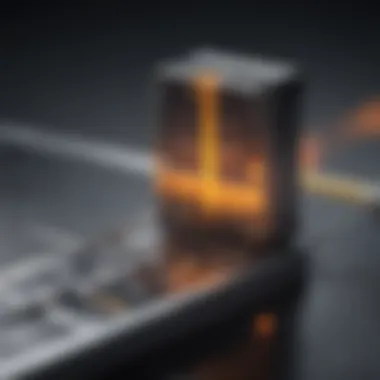
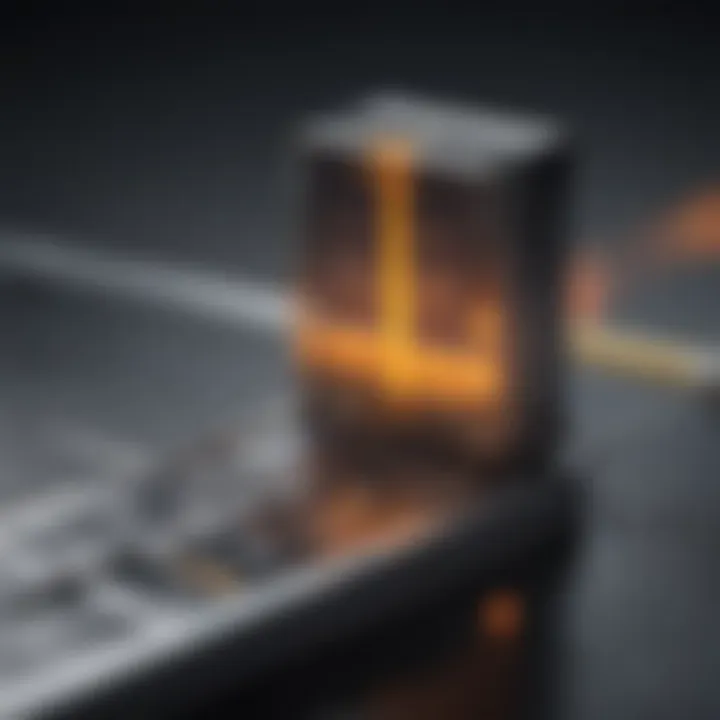
Intro
The monitoring of cracks within materials is essential to ensure structural integrity. Cracks can develop due to various factors including stress, environmental conditions, and material fatigue. This article will explore the role of strain gauges, valuable tools for measuring deformation, in monitoring such cracks. An understanding of the principles of strains and how gauges work can enhance proactive measures in maintenance and safety.
Research Overview
Crack monitoring research with strain gauges has garnered attention in both civil and mechanical engineering. Researchers focus on developing methodologies and improving technologies to increase accuracy and reliability.
Methodological Approaches
Current approaches involve several techniques designed to fit specific scenarios. One common methodology is bonding strain gauges to the surface of the material. This allows for direct observation of how cracks propagate as stress changes. Other methods may involve embedded gauges in concrete or other substrates, allowing for real-time monitoring of internal stresses.
Significance and Implications
The significance of using strain gauges in crack monitoring cannot be overstated. These devices provide critical data that enables engineers to make informed decisions in the maintenance and rehabilitation of structures. Thus, the implications extend beyond mere monitoring; they inform safety measures and direct future engineering practices, which can prevent catastrophic failures.
Current Trends in Science
As technology in structural monitoring evolves, innovative techniques emerge to enhance the capabilities of strain gauges in crack detection.
Innovative Techniques and Tools
Recent advancements have led to the development of wireless strain gauges, reducing the complications associated with wiring and installation. Additionally, integration with Internet of Things (IoT) technology allows for remote monitoring and data collection, streamlining analysis processes defensively.
Interdisciplinary Connections
The applications of strain gauges stretch beyond engineering. Connections can be seen between materials science, data analytics, and even environmental science. Understanding materials on a molecular level provides insights into how they will behave under stress and how cracks can form. Data analytics contributes to discerning patterns from the data collected, thus improving predictive capabilities.
The integration of modern technology with traditional strain gauge principles marks a significant step forward in predictive maintenance and safety.
Intro to Strain Gauges
Strain gauges are pivotal in the field of material science and structural engineering. Their ability to detect minute changes in strain provides critical insights into the health of various materials and structures. In this section, we explore the essential aspects of strain gauges, focusing on their importance, applications, and the considerations that come along with their use.
Understanding strain gauges is vital for anyone involved in crack monitoring. These instruments translate physical deformations into measurable electrical signals, enabling engineers and scientists to assess material integrity effectively. By applying strain gauges, one can monitor the ongoing processes of strain and stress accumulation that may lead to cracks. This proactive approach is crucial for maintaining safety in infrastructure and machinery.
Definition and Function
A strain gauge is a sensor that measures the amount of deformation or strain experienced by an object. When a force is applied to a material, it deforms; this change can be quantified using a strain gauge. Generally, a strain gauge consists of a thin conductive wire arranged in a zigzag pattern. As the material stretches or compresses, the wire also changes its length and consequently its electrical resistance. This change in resistance is then converted into a readable output.
The main function of strain gauges is to detect and measure strain in real-time, providing critical data that can be used for analysis, design, and some maintenance procedures. Accurate reads of strain can anticipate failure points before they compromise the integrity of structures, allowing for timely repairs or modifications.
Historical Development
The development of strain gauge technology dates back to the late 1930s. Early models were quite rudimentary but laid the groundwork for many modern innovations. Initially, they were predominantly used in aerospace and civil engineering. However, their application has expanded significantly over recent decades.
Notable advancements include the introduction of thin-film technology and semiconductor strain gauges, which offer improved sensitivity and reduced size. This evolution has led to their widespread adoption across various industries including Automotive, manufacturing, and even biomedical fields.
Basic Principles of Measurement
Understanding the basic principles of measurement is crucial in leveraging strain gauges for effective crack monitoring. This section delves into the core elements that underpin how strain gauges work, focusing on two main areas: mechanical strain and electrical resistance. By grasping these principles, engineers and researchers can enhance their approaches to structural health monitoring, ensuring that data acquired is both accurate and reliable.
Mechanical Strain and Its Importance
Mechanical strain refers to the deformation that a material undergoes when a force is applied. This deformation is an important measure as it indicates how much a structure is bending or twisting under stress. The significance of mechanical strain lies in its ability to predict potential failure points in materials. A small straint can lead to significant issues over time.
Crack monitoring using strain gauges enables the identification of increased strain levels, often preceding actual cracking. Recognizing these signs early can help mitigate risks and prevent catastrophic failures in structures, such as bridges or buildings. Therefore, understanding mechanical strain is not merely an academic exercise; it is central to maintaining the integrity and safety of critical infrastructures.
Electrical Resistance and Strain Gauges
Strain gauges operate on the principle of electrical resistance change due to strain. When a strain gauge is stretched or compressed, its electrical resistance changes in proportion to the deformation it experiences. This phenomenon is key to their functionality. The sensitivity of strain gauges is determined by how noticeably their resistance changes under mechanical strain.
The relationship between mechanical strain and electrical resistance can be expressed as:
R = R0 (1 + k * ( \epsilon \))
where:
- R = resistance of the gauge under strain
- R0 = initial resistance
- k = gauge factor (a constant specific to the gauge type)
- ( \epsilon \) = strain applied
This precise relationship underscores the importance of understanding electrical resistance for anyone involved in crack monitoring. Measuring resistance accurately allows engineers to infer the degree of strain, which can indicate potential structural failures.
Types of Strain Gauges
There are several types of strain gauges, each with unique characteristics suited to different applications. The major types include wire strain gauges, thin-film strain gauges, and semiconductor strain gauges.
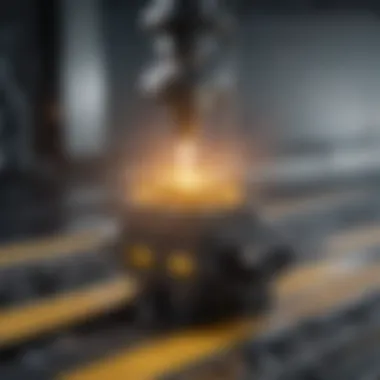
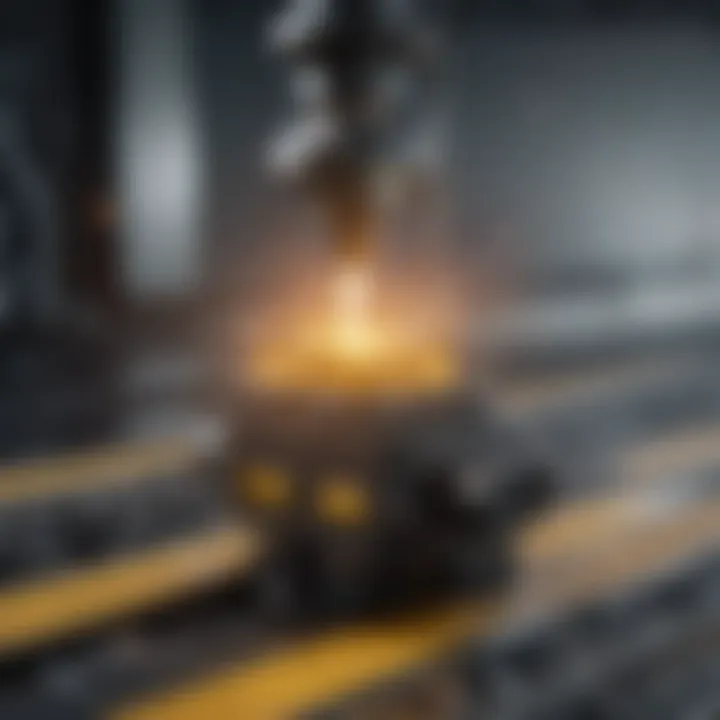
Wire Strain Gauges
Wire strain gauges utilize fine wire to create a grid pattern, making them highly sensitive to strain. They are often chosen for their durability and resilience. The key characteristic of wire strain gauges is their ability to withstand high temperatures and harsh environments, which is a beneficial aspect for crack monitoring in extreme conditions.
One unique feature of wire strain gauges is their excellent linearity, meaning that as strain increases, the resistance changes predictably. However, these gauges can be challenging to install, as precise positioning is necessary for accurate readings.
Thin-Film Strain Gauges
Thin-film strain gauges consist of a metallic layer deposited onto a flexible substrate. They are known for their compact size and flexibility, making them suitable for applications where space is limited. The primary advantage of thin-film strain gauges is their quick response time and sensitivity, allowing for real-time monitoring of structural integrity.
A unique feature of these gauges is their ability to minimize hysteresis effects, which can sometimes distort strain measurements. However, they may not perform as well under extreme temperatures compared to wire strain gauges.
Semiconductor Strain Gauges
Semiconductor strain gauges have a high gauge factor, making them extremely sensitive to even the slightest strain. This characteristic allows them to detect small crack formations effectively. Their primary advantage is their unparalleled sensitivity, making them a top choice where precision is paramount.
Nevertheless, semiconductor strain gauges can be more expensive and may present challenges in terms of temperature sensitivity and linearity. This means that while they offer excellent performance, careful consideration of their application context is necessary to ensure reliable results in crack monitoring.
By understanding these types and their respective strengths and weaknesses, professionals can select the most appropriate strain gauge for specific monitoring scenarios, greatly impacting data quality and analysis in structural health monitoring.
Crack Monitoring: Importance and Applications
Crack monitoring holds significant importance across various engineering disciplines. As materials endure stressors such as environmental factors, fatigue, and operational loading, they may develop cracks that can compromise structural integrity. Early detection and monitoring of these cracks can prevent catastrophic failures, ensuring safety and longevity of structures.
Structural Integrity in Engineering
Structural integrity is the ability of a structure to withstand its intended load without experiencing failure due to fracture or excessive deformation. Monitoring cracks is a vital aspect of maintaining this integrity. Structures such as bridges, buildings, and pipelines are under constant stress from various sources.
For instance, in civil engineering, cracks in concrete can indicate underlying issues related to material degradation or improper load distribution. Identifying these cracks early allows for timely maintenance and repair, thus significantly reducing the risk of structural failures.
Key Benefits of Structural Integrity Monitoring:
- Safety Assurance: Enhances the safety of occupied spaces and ensures the welfare of users.
- Cost Efficiency: Early intervention can save substantial costs associated with major repairs and replacements.
- Longevity: contributes to the extended lifespan of infrastructure by ensuring materials and designs remain effective.
Role of Crack Monitoring
Crack monitoring plays a crucial role in assessing and maintaining the health of structures. By utilizing technologies such as strain gauges, engineers can measure shifts in structural behavior and detect cracking. This continuous monitoring process is essential for several reasons:
- Data-Driven Decisions: Engineers rely on accurate data to make informed decisions regarding maintenance and repairs.
- Predictive Maintenance: With long-term monitoring, it is possible to predict when and where issues may arise, allowing for preemptive measures.
- Compliance and Regulations: Many engineering standards require regular assessments of structural health, making monitoring a regulatory necessity.
"Early detection of cracks is fundamental in preventing failure, thus preserving safety and structural integrity."
Applications of Crack Monitoring Include:
- Infrastructure Projects: Bridges and highways benefit from regular monitoring to detect stress points.
- Aerospace Industry: Aircraft components undergo rigorous monitoring to ensure flight safety and performance.
- Construction: Continuous assessments during construction phases can prevent future issues related to cracking.
Implementing Strain Gauges for Crack Monitoring
Implementing strain gauges for crack monitoring is a crucial component in ensuring the integrity of structures and materials. These devices can detect minute alterations in strain caused by cracks, providing real-time data that aids in early diagnosis and remediation. The successful application of strain gauges requires meticulous planning and precise execution, ensuring that measurements reflect the true conditions within a material or structure.
In this section, we will delve into two primary aspects of implementation: site preparation and gauge selection, followed by installation techniques and essential considerations. Each of these elements plays a vital role in the efficacy of crack monitoring efforts.
Site Preparation and Gauge Selection
Before installation can begin, proper site preparation is necessary. Assessing the location where strain gauges will be applied is critical. Factors such as surface condition, environment, and accessibility must be evaluated meticulously.
- Surface Condition: The surface must be clean, dry, and free of any contaminants that might interfere with the adhesion of the gauge. In some cases, surface preparation may involve sanding or degreasing to create an ideal bonding surface.
- Environment: Different environments can significantly affect gauge performance. For instance, areas exposed to high humidity or chemical exposure require specialized strain gauges capable of withstanding such conditions. Gauges made from materials like stainless steel or polymer can be considered depending on the environmental factors.
- Accessibility: It is also essential to consider how easy it is to access the monitoring site for both installation and maintenance. If the site is difficult to access, more robust gauges may be necessary to ensure prolonged functionality.
Selecting the appropriate strain gauge is equally fundamental. The choice depends on several factors, including:
- Material Type: The physical characteristics of the material must be understood to select a gauge that matches its properties. Thin-film gauges might be preferable for smooth surfaces, while wire gauges may perform better in rough or uneven conditions.
- Expected Strain Levels: Understanding the anticipated strain is crucial. Select gauges with appropriate sensitivity. High-sensitivity gauges are typically needed for materials that undergo slight deformations.
- Temperature Range: Ensure the selected gauge can operate within the temperature limits present at the monitoring site.
Installation Techniques and Considerations
The installation of strain gauges requires precision and attention to detail. An improper installation can lead to inaccurate readings or even gauge failure.
- Alignment: The gauge must be aligned correctly with the expected strain direction. Accurate orientation is key to ensure that the gauge measures the strain effectively, avoiding false readings.
- Adhesive Application: The adhesive used to secure the gauge should be appropriate for the operating conditions. Applying the adhesive should be done carefully, ensuring uniform application to avoid bubbles that could affect gauge performance. Allowing proper curing time is vital to securing a strong bond.
- Wiring and Connections: After the gauge is secured, careful attention to wiring is necessary. Ensure that all connections are secure and that the wires are routed away from potential damage and interference.
- Testing: Once installed, a preliminary calibration test should confirm that the gauges are functioning before they are left for monitoring. This can help identify any potential issues early.
Implementing strain gauges for crack monitoring is not merely a technical necessity; it is a strategic practice that can safeguard structures against impending failures. A meticulous approach to both site preparation and gauge selection, combined with careful installation techniques, enhances the reliability of the data gathered and fortifies the integrity of the structures being monitored.
Data Acquisition and Analysis
Data acquisition and analysis play a pivotal role in leveraging strain gauges for effective crack monitoring. Accurate measurement of strain and crack progression is essential for assessing the integrity and longevity of structures. The choice of data acquisition systems and methods directly influences the reliability of the results obtained not just for academic research but also for practical applications in industries such as civil engineering and aerospace.
Real-Time Data Monitoring
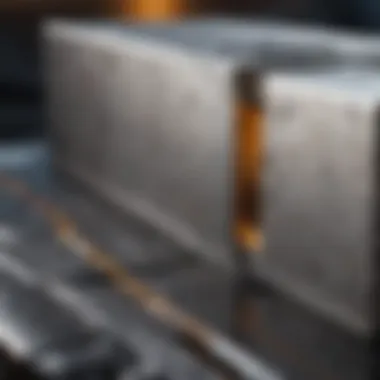
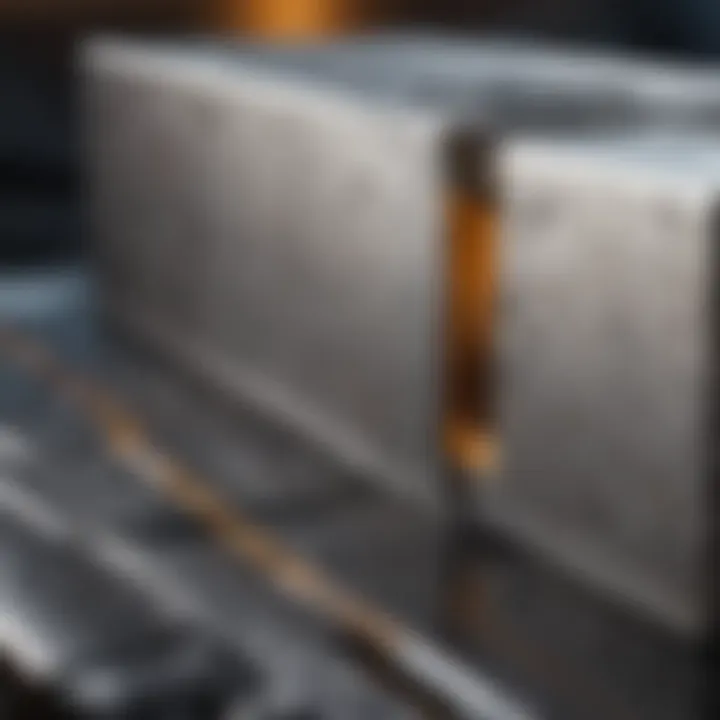
Real-time data monitoring is indispensable in the context of crack monitoring using strain gauges. It enables immediate detection of structural changes, allowing for timely maintenance or intervention strategies. This can prevent catastrophic failures, which might occur if cracks are left undetected.
The integration of advanced data acquisition systems allows engineers to collect continuous strain measurements. These systems typically consist of:
- Strain Gauges: Attached to the monitored structure, they convert mechanical deformation into electrical signals.
- Data Loggers: These devices record data from strain gauges for further analysis. They can store large volumes of data over long periods.
- Software Interface: This allows for real-time visualization and analysis of data, making it easier to identify trends in crack development.
The ability to monitor data in real-time supports proactive decision-making. This is highly valuable for infrastructure that is susceptible to wear or fatigue over time.
Data Interpretation Techniques
Once data is acquired, appropriate interpretation techniques must be employed to extract meaningful insights. Several methodologies exist for analyzing strain measurement data from cracks:
- Statistical Analysis: This involves using statistical tools to identify patterns and correlations within the acquired data. By evaluating the distribution and variance of strain measurements, one can determine if certain regions are more prone to cracking.
- Finite Element Analysis (FEA): This computational method helps in modeling the structural response based on the strain data. FEA can predict the behavior of structures under various load conditions, aiding engineers to understand potential failure points.
- Trend Analysis: Observing strain measurements against the timeline can reveal trends in crack propagation. An increase in strain over time may indicate a need for intervention before reaching a critical failure threshold.
Through these techniques, structural engineers can formulate effective maintenance strategies. This improves not just safety but also the economic efficiency of maintaining infrastructure and components.
Integrating effective data acquisition and analysis not only enhances safety but contributes significantly to sustainable engineering practices.
In summary, data acquisition and analysis are crucial components of successful crack monitoring using strain gauges. By employing real-time monitoring and appropriate interpretation techniques, professionals can maintain the integrity of structures and prevent failures.
Factors Influencing Measurement Accuracy
The accuracy of measurements obtained using strain gauges is critical for effective crack monitoring in various structures. Understanding the factors that influence this accuracy helps ensure reliable data collection and subsequent analysis. Accuracy not only defines the measurement's trustworthiness but also determines the effectiveness of the crack monitoring procedures in applications like civil engineering or material testing.
There are several key elements to consider regarding measurement accuracy. These include temperature effects, material properties, gauge alignment, and environmental conditions. Each of these factors can significantly impact the performance of the strain gauges.
Temperature Effects
Temperature plays a significant role in the operation of strain gauges. Changes in temperature affect the gauge's electrical resistance, which is fundamental for measuring strain. Different materials expand or contract differently under temperature changes, creating potential discrepancies in strain readings.
Monitoring the temperature during measurements is essential. Without careful consideration, one might misinterpret the data, attributing changes in resistance erroneously to physical strain rather than thermal fluctuations. The design and selection of gauges can mitigate some temperature effects. For example, using temperature-compensated strain gauges helps ensure that readings remain accurate despite thermal variations.
Material Properties and Limitations
Different materials exhibit distinct characteristics that affect the performance of strain gauges. The Young's modulus, yield strength, and ductility of the material can influence how the strain gauge responds to applied forces. For instance, in very brittle materials, the strain concentration at the gauge can lead to premature failure, resulting in inaccurate readings.
Evaluating the material properties before implementing crack monitoring is crucial. Moreover, the adhesive used for attaching the strain gauges must also be compatible with the substrate material to avoid issues like delamination, which can further affect accuracy. Understanding the limitations of both the gauge and the substrate material ensures that the selected methods yield the most reliable data possible for effective crack monitoring.
Accurate measurement is the foundation of effective structural health monitoring, necessitating comprehensive understanding and consideration of various influencing factors.
Advantages of Using Strain Gauges for Crack Monitoring
The integration of strain gauges into crack monitoring practices offers numerous advantages that are vital for ensuring the structural integrity of various materials. Understanding these advantages helps professionals and researchers make informed decisions about their use in various applications.
High Sensitivity and Resolution
One of the most notable advantages of strain gauges is their high sensitivity and precision in detecting even the slightest changes in strain. This high sensitivity allows for the early detection of cracks, which is critical in preventing structural failures. Strain gauges can capture minute deformations, offering an insight into material behavior under stress.
- Small Changes Detection: Strain gauges can detect minute variations in strain, often as small as micro-strains. This capability is essential for monitoring structures subjected to dynamic loads or environmental changes.
- Real-Time Monitoring: With modern data acquisition systems, strain gauges facilitate real-time monitoring, enabling engineers to observe strain changes continuously. This immediate feedback loop allows for rapid response to any issues found within the monitored entities.
- High Resolution: The electrical resistance change in a strain gauge is proportional to the strain applied. This proportionality ensures accurate readings, which aids in precision engineering tasks.
Versatile Applications
Strain gauges are not limited to a single field; they have versatile applications across various industries, enhancing their importance in crack monitoring. Their adaptability to different materials and environments makes them indispensable tools in many sectors.
- Civil Engineering: In civil applications, strain gauges monitor bridges, dams, and buildings. This use helps ensure that structures can withstand loads and environmental forces.
- Aerospace Engineering: Strain gauges play a crucial role in aircraft and spacecraft design. They ensure that components can endure extreme conditions and load changes that may lead to crack formation.
- Mechanical Engineering: The automotive industry utilizes strain gauges for fatigue testing and stress analysis of vehicle components. These applications help to prevent failures and extend service life.
- Research and Development: In academic and research settings, strain gauges help validate theoretical models and studies. They provide empirical data that contribute to the development of new technologies and materials.
In summary, the advantages of using strain gauges for crack monitoring extend beyond simple measurements. Their high sensitivity allows for the detection of minute strains, while their versatility opens doors to applications across diverse industries. This makes them a fundamental tool in maintaining structural health and ensuring safety.
Limitations and Challenges
Understanding the limitations and challenges of using strain gauges for crack monitoring is essential to both practitioners in the field and researchers. These constraints can directly affect the reliability of the measurements taken, thus informing decisions made in structural health monitoring. Itโs critical to grasp these issues, as they can guide the choice of appropriate strain gauge technology and installation methods.
Calibration and Drift Issues
Calibration is a vital process in ensuring that strain gauges provide accurate measurements. Without proper calibration, the data they produce can be misleading, which has significant implications for monitoring crack behavior. Calibration involves adjusting the measurement system so that it accurately reflects the physical changes occurring in a material's structure.
Drift refers to the gradual change in a measurement over time, even when the conditions remain constant. This can occur due to several factors, including temperature variations or changes in the environment around the strain gauge. Drift can skew the readings, leading to incorrect assessments of crack growth. Monitoring the drift requires regular checks and recalibrations, which can be labor-intensive and resource-demanding. Therefore, ensuring that the strain gauges remain calibrated during their operational life is crucial for obtaining reliable data.
Environmental Influences
Environmental conditions can vastly impact the performance of strain gauges. Elements like humidity, dust, and temperature fluctuations can all affect the accuracy of readings. For instance, high humidity might lead to corrosion of the strain gauge itself, compromising its ability to measure strain accurately. Similarly, extreme temperatures can change the physical properties of the materials being monitored, which can alter how strain is transmitted to the gauge.
Furthermore, the substrate on which the strain gauge is mounted also plays a role. If the substrate expands or contracts differently than the strain gauge due to environmental influences, the readings may not correspond accurately to the actual strain occurring in the material.
Here are some factors influenced by the environment:
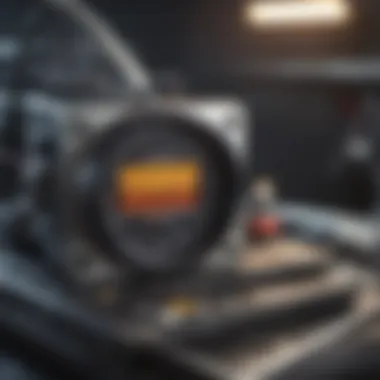
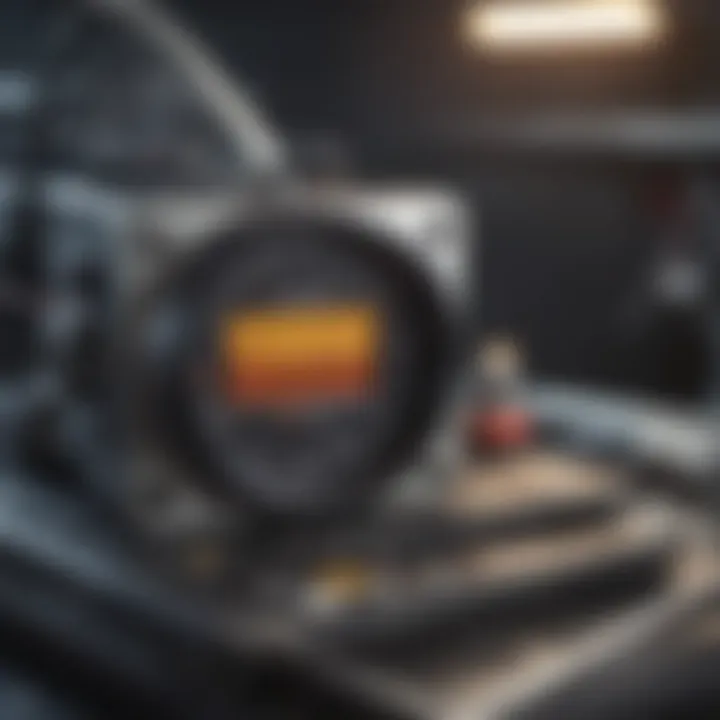
- Temperature fluctuations can cause materials to expand or contract differently.
- Humidity can lead to corrosion and damage to the strain gauge.
- Mechanical vibrations may introduce noise into the readings.
Efforts to mitigate these environmental influences include selecting appropriate strain gauge materials that can withstand specific conditions and employing protective coatings. If these factors are not carefully managed, the risk of obtaining inaccurate data increases, which could lead to potential failures in monitoring.
"Understanding the limitations is key to maximizing the effectiveness of strain gauges in crack monitoring."
By identifying these limitations and challenges at the outset, engineers and technicians can better prepare for potential pitfalls in monitoring crack growth. Addressing issues of calibration and environmental influences, they can enhance the accuracy and effectiveness of their monitoring efforts, leading to better outcomes in structural health assessments.
Future Trends in Crack Monitoring Technologies
The landscape of crack monitoring is evolving rapidly, driven by technological advances. This section explores future trends that will likely reshape how strain gauges are used and enhance their efficiency in crack detection. Understanding these trends is crucial for professionals looking to adopt cutting-edge methodologies.
Emerging Technologies
Advancements in materials science and engineering are paving the way for new strain gauge technologies. Emerging materials, such as fiber optic sensors and wireless sensors, are gaining attention. These technologies can offer significant advantages over traditional strain gauges. For example, fiber optic sensors are immune to electromagnetic interference, making them ideal for complex environments. On the other hand, wireless sensors provide real-time data transmission without the need for extensive cabling. The combination can lead to easier installation and maintenance.
Additionally, innovations in nanotechnology could enhance the sensitivity of strain gauges. Nanostructured materials can offer improved performance, allowing for the detection of even minuscule changes in strain.
Moreover, machine learning algorithms can analyze data collected from strain gauges efficiently. These algorithms can identify patterns that might indicate developing cracks, improving the reliability of monitoring systems. The integration of these emerging technologies is likely to create a more comprehensive monitoring solution that will benefit various industries.
Integration with IoT Systems
The advent of the Internet of Things (IoT) introduces exciting possibilities for crack monitoring. By integrating strain gauges with IoT systems, real-time data can be acquired and analyzed remotely. This capability enhances the ability to monitor structural integrity continuously, significantly reducing the response time in case of emergencies.
IoT platforms can also aggregate data from multiple sensors, providing a macro view of structural health. For example, buildings and bridges equipped with numerous strain gauges can feed information into a central system. This system can then analyze and visualize data trends, helping engineers make informed decisions.
Moreover, the accessibility of such information can empower stakeholders to undertake timely maintenance actions, potentially before cracks become critical. The concept of smart infrastructure could transform how we understand and manage civil structures. Leading companies are already developing integrated monitoring solutions that utilize these advances.
Quote: "The integration of IoT in crack monitoring not only enhances efficiency but also establishes a proactive approach in infrastructure management."
In summary, the future of crack monitoring technologies appears promising. Emerging materials and IoT integration will likely revolutionize how engineers and researchers approach crack monitoring, contributing to greater safety and longevity in structures.
Case Studies and Practical Applications
In the field of civil and mechanical engineering, case studies serve as a vital tool for understanding the practical applications of strain gauges in crack monitoring. They provide real-world examples that illustrate both the effectiveness and the challenges associated with strain gauge deployment. These practical applications are essential for validating theoretical concepts and showcasing the capability of strain gauges to enhance structural integrity assessments. By analyzing case studies, professionals can draw insights that inform future projects, leading to better design and maintenance practices.
Infrastructure Monitoring
One prominent area where strain gauges find extensive application is in infrastructure monitoring. Structures such as bridges, dams, and tunnels are subject to various stresses that can induce cracks over time. Monitoring these cracks is crucial for ensuring the safety and longevity of these assets. Strain gauges allow for precise measurements of deformation, helping engineers detect early signs of structural failure.
In a case study on a large bridge, strain gauges were installed at strategic locations. The data collected highlighted changes in strain during heavy traffic loads as well as seasonal temperature variations. This information enabled engineers to develop predictive maintenance schedules, reducing the risk of unexpected failures.
Using strain gauges in infrastructure monitoring offers several benefits:
- Enhanced Safety: Continuous monitoring can reveal potential risks before they lead to accidents.
- Cost Savings: Early detection of issues can prevent costly repairs and prolong the lifespan of structures.
- Data-Driven Decisions: Engineers can use the data to make informed decisions about maintenance and upgrades.
Aerospace and Precision Engineering
The aerospace industry also leverages strain gauges for monitoring structural integrity. Aircraft components and assemblies are designed to withstand extreme conditions, making crack monitoring vital. In aircraft wings and fuselage, strain gauges provide insights into the stress these components experience during flight.
For instance, in a study involving the wing of a commercial aircraft, strain gauges were placed strategically to monitor the stresses during takeoff and landing. The collected data revealed critical information about fatigue loading, which is essential for assessing the lifespan of the aircraft. The insights gathered from this study not only improved safety protocols but also informed the design of future aircraft.
The applications of strain gauges in aerospace and precision engineering are characterized by:
- Real-Time Monitoring: Ability to track deformation during operational conditions ensures immediate responses to potential failures.
- Research and Development: Strain gauge data supports design improvements for better performance and safety.
- Compliance with Regulations: Helps manufacturers meet stringent safety standards imposed by aviation authorities.
Strain gauges are essential instruments across various industries, proving their value through both empirical evidence in case studies and practical applications in critical engineering fields.
Epilogue
In the context of this article, the conclusion serves as a pivotal part that encapsulates the journey through strain gauge applications in crack monitoring. It synthesizes the extensive discussions on the principles, advantages, limitations, and recent innovations in the field. Recognizing these aspects is essential in putting forth a comprehensive understanding of how strain gauges contribute to structural health monitoring and material integrity assessment.
The key elements highlighted throughout the article underscore the fundamental role of strain gauges in early crack detection and monitoring. This capability is paramount in sectors where safety and performance are critical, such as civil engineering, aerospace, and mechanical structures.
Benefits of Strain Gauges include:
- Precision Monitoring: Their ability to detect minute changes in strain helps in identifying potential failures before they become critical.
- Versatility: They can be applied to a range of materials and structures, offering a flexible solution for various engineering challenges.
- Data-Driven Decisions: The data they provide empower engineers to make informed decisions regarding maintenance and repair.
Considerations about Conclusion include understanding that while strain gauges are powerful tools, their effectiveness can still be influenced by environmental factors, material properties, and potential calibration issues. These challenges need to be acknowledged to enhance the deployment strategies across different industries.
Summarizing everything, the conclusion reinforces the relevance of strain gauges in contemporary engineering practices and the necessity for ongoing research and adaptation of emerging technologies to optimize their use in crack monitoring.
Summary of Key Points
- Importance of Strain Gauges: Strain gauges are instrumental in ensuring structural integrity by providing real-time data about material stresses and potential crack formation.
- Applications Across Multiple Industries: From infrastructure to aerospace, their versatility allows for extensive applications tailored to specific needs.
- Technological Advancements: Recent innovations are enhancing the accuracy and data acquisition capabilities of strain gauges, making them even more effective.
- Real-World Relevance: Case studies demonstrate their implementation in various sectors, emphasizing their practical significance.
Future Outlook
The future of crack monitoring with strain gauges is poised for significant advancement. Key trends to consider include:
- Emerging Technologies: New materials and sensor technologies are expected to improve the sensitivity and durability of strain gauges.
- Integration with IoT: The convergence of strain gauge technology with Internet of Things systems will facilitate real-time monitoring, predictive analytics, and remote data access.
- Sustainability Considerations: As industries move towards greener practices, the incorporation of sustainable materials in strain gauge development may become more prominent.
Overall, as the demand for robust monitoring solutions escalates, strain gauges will continue evolving. Their importance in safeguarding structural health will only intensify, making them an indispensable tool in engineering and material sciences.