Exploring the Strength of Inconel 718: Properties and Applications
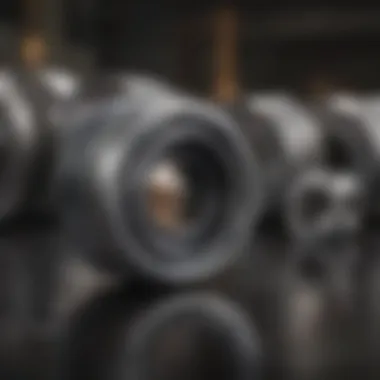

Intro
Inconel 718 is a unique nickel-chromium alloy recognized for its remarkable strength and excellent corrosion resistance. Developed during the 1960s, this material has become critical in various industries, particularly aerospace and energy. Researchers and engineers value Inconel 718 for its ability to perform in demanding environments, including high temperatures and pressures.
The alloy's chemical composition primarily consists of nickel, chromium, iron, and notable additions of molybdenum and niobium. These elements work in tandem to enhance the material's mechanical properties, making it suitable for intricate applications such as turbine components, fasteners, and structural parts in aerospace technologies.
This article will systematically explore Inconel 718's properties, its manufacturing processes, and its applications across several sectors. By delving into these aspects, we aim to provide a comprehensive understanding for both academic and industry professionals interested in modern material applications.
Research Overview
Methodological Approaches
The examination of Inconel 718 involves a multifaceted research approach. Various methods such as metallography, mechanical testing, and corrosion analysis are employed to assess the alloy's capabilities. These methodologies allow researchers to characterize the material's microstructure and understand how different manufacturing processes affect its properties.
Recent advancements in digital modeling and simulations further aid in predicting the behavior of Inconel 718 under varied conditions. Using these innovative techniques, experts can better understand how the alloy will perform in real-world applications.
Significance and Implications
The significance of Inconel 718 extends beyond its mechanical properties. Its availability and performance under extreme conditions have profound implications for the aerospace and energy industries. The demand for high-performance materials that can withstand harsh environments is continually increasing. Thus, exploring the full potential of Inconel 718 is essential for advancing technology in these sectors. Understanding its strengths can lead to improved designs and extended service lives for critical components.
Inconel 718 remains indispensable to engineering and manufacturing disciplines, owing to its outstanding mechanical performance in high-stress environments.
Current Trends in Science
Innovative Techniques and Tools
Research into Inconel 718 is at the forefront of material science. Innovative techniques such as additive manufacturing are quickly evolving, allowing for the production of complex geometries that were previously unattainable. This approach not only optimizes material usage but also enhances the performance characteristics of the parts produced.
Interdisciplinary Connections
Inconel 718's use demonstrates strong interdisciplinary connections between material science, engineering, and computational analysis. Professionals in different fields collaborate to optimize the performance of this alloy, ensuring it meets the growing demands of various industries. This collaboration points to a significant trend in engineering: leveraging expertise across disciplines to enhance material applications.
Intro to Inconel
Inconel 718 stands as a significant material in the realm of high-performance alloys. Its unique set of properties makes it indispensable for various industrial applications. This section provides an understanding of what Inconel 718 is and its historical development, which is crucial for appreciating its utility today.
Definition of Inconel
Inconel 718 is a nickel-chromium alloy that also contains iron, niobium, and molybdenum. This composition grants it exceptional strength and remarkable resistance to corrosion and oxidation. Importantly, Inconel 718 maintains its strength even at elevated temperatures, which is a critical requirement in many applications, particularly in aerospace and energy sectors. Its resistance to softening is a sought-after trait for engineers looking for materials that perform consistently under stressful conditions.
Historical Background
The development of Inconel 718 dates back to the late 1940s. Initially, it was created for applications requiring high strength at elevated temperatures and to withstand corrosive environments. With aerospace advancements, the need for lightweight and robust materials escalated. Inconel 718 was recognized as a game changer, particularly for jet engines and gas turbines. Over the years, its adoption expanded across various sectors, including chemical processing and power generation. The ability to tailor this alloy through heat treatment and its weldability further entrenched Inconel 718 as a go-to material in high-stress environments, adapting to the evolving demands of modern industry.
"Inconel 718 is integral in applications requiring high performance in extreme conditions, setting standards for functional and structural integrity."
This historical context not only underscores the alloy's evolution but also sets the stage for a deeper examination of its mechanical properties, manufacturing methods, and applications in the following sections.
Chemical Composition and Structure
The chemical composition and structure of Inconel 718 are fundamental to its performance and application across various industries. Understanding the specific elements that make up this alloy sheds light on its robust mechanical properties and its ability to withstand extreme conditions. This section will explore the essential elements within Inconel 718 and its phase components, illustrating how these factors contribute to its exceptional strength and resilience.
Essential Elements
Inconel 718 is primarily composed of nickel and chromium, along with significant quantities of iron, molybdenum, and niobium. Each of these elements plays a critical role in defining the alloy's characteristics:
- Nickel: This is the main element providing Inconel 718 with its excellent corrosion resistance and high-temperature stability. Nickel maintains its structure and properties even at elevated temperatures, making it suitable for demanding environments.
- Chromium: Present in substantial amounts, chromium enhances oxidation resistance and contributes to the overall hardness of the alloy. It creates a protective oxide layer on the surface, preventing corrosion.
- Iron: While present in smaller quantities, iron provides the necessary strength and toughness without dramatically compromising the alloy's other properties.
- Molybdenum: This element is crucial for increasing resistance against pitting and crevice corrosion. Molybdenum strengthens the alloy, especially in acidic environments.
- Niobium: It serves multiple purposes; niobium stabilizes the gamma prime phase, which enhances the alloy’s heat treatment response, leading to improved strength characteristics.
These components collectively forge the reliability of Inconel 718. Their synergistic effects result in a material that offers both heat resistance and structural integrity over a broad range of operating conditions.
Phase Components
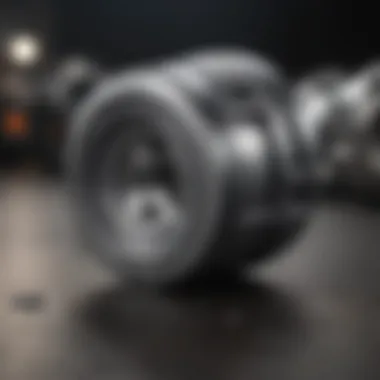
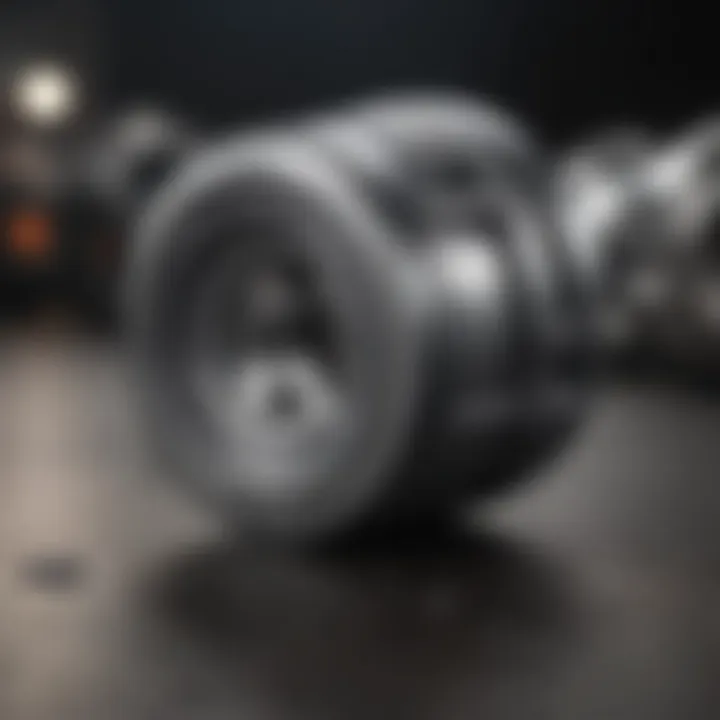
Inconel 718's microstructure is another important aspect to consider. The alloy consists of various phases including the gamma (γ) phase, the gamma prime (γ′) phase, and delta (δ) phase. These phases arise from the heat treatment processes employed during manufacturing.
- Gamma Phase (γ): This is the face-centered cubic phase that dominates the microstructure at high temperatures. It has good ductility and strength, making it suitable for structural applications.
- Gamma Prime Phase (γ′): Formed after heat treatment, this phase contributes significantly to the high strength characteristics. It precipitates out of the gamma matrix and provides an enhanced yield strength through solid solution strengthening.
- Delta Phase (δ): This phase is typically less desirable, appearing due to prolonged exposure at high temperatures. It can have a detrimental effect if not carefully managed during processing. However, a controlled presence of this phase can still support the overall properties of the alloy.
Understanding these phase components is essential for optimizing manufacturing processes and predicting how the material will behave under various conditions. It is crucial for engineers and designers to consider these factors when selecting Inconel 718 for specific applications.
Inconel 718 is recognized not only for its sheer strength but also for its excellent ductility, which enables it to absorb energy and deform without fracturing.
The interplay between the chemical composition and the phases of Inconel 718 underscores its applications in industries such as aerospace and energy, where reliability and performance are paramount. Each component contributes to an alloy that is uniquely suited for high-performance scenarios, making it an indispensable material in modern engineering.
Manufacturing Processes of Inconel
The manufacturing processes of Inconel 718 are critical to its performance characteristics and practical applications. These processes ensure that the alloy reaches its full potential in terms of strength, durability, and resistance to harsh environments. Understanding the methods involved not only sheds light on the alloy itself but also offers insights into how it can be tailored for specific industries. Without proper manufacturing techniques, the desirable properties of Inconel 718, such as its high-temperature stability and corrosion resistance, may be compromised.
Hot Working Techniques
Hot working refers to a series of processes where Inconel 718 is shaped at elevated temperatures, allowing for easier manipulation of its structure. This method is essential because it enhances grain structure, which in turn improves overall toughness and ductility. Techniques like forging, rolling, and extrusion are commonly employed. During these operations, the workpiece reaches temperatures above its recrystallization point, promoting sufficient plasticity for deformation.
Here’s a summary of the key hot working techniques:
- Forging: This is a widely used hot working process where the alloy is compressed between dies, enhancing its strength through controlled deformation.
- Rolling: This method involves passing the material through rollers to achieve the desired thickness and shape.
- Extrusion: In this technique, softened Inconel 718 is forced through a die, producing long shapes with consistent cross-sections.
Each of these methods influences the atomic structure of Inconel 718, refining its properties. Proper temperature management is crucial, as overheating can lead to oxidation and loss of desirable attributes. Consequently, these hot working techniques play a significant role in determining the alloy's effectiveness in real-world conditions.
Heat Treatment Procedures
Heat treatment is a vital step in the preparation of Inconel 718, as it significantly enhances the material's mechanical properties. The focus during heat treatment is often on achieving a balance between strength and ductility. Typical procedures involve solution treatment followed by aging, where the material is held at specific temperatures to achieve desired microstructures.
The heat treatment process usually includes:
- Solution Treatment: This step typically takes place around 1,720°F (about 940°C) and can last up to one hour. It dissolves the gamma prime precipitates, contributing to increased toughness.
- Aging: After solution treatment, the alloy is cooled and then aged at a lower temperature, around 1,300°F (about 700°C). This process allows for precipitation of gamma prime phases, which greatly increase yield strength while maintaining ductility.
The following are the advantages of heat treatment for Inconel 718:
- Increased Strength: The precipitation hardening enhances strength significantly.
- Improved Ductility: This prevents brittleness, making the material more adaptable in applications.
- Stability: Heat treatment reduces residual stresses, resulting in better dimensional stability.
Attention to detail in the heat treatment process is paramount, as it directly impacts the performance of the final product in extreme conditions. With these carefully controlled manufacturing processes, Inconel 718 emerges as a leading material in demanding applications.
Mechanical Properties of Inconel
The mechanical properties of Inconel 718 are crucial in understanding its suitability for various high-stress applications. This nickel-chromium alloy is renowned not just for its corrosion resistance, but also for its remarkable mechanical durability. Analyzing these properties is vital for professionals who design and engineer components in sectors like aerospace and energy. The focus on tensile strength, yield strength, elongation characteristics, and fatigue resistance defines the functional limits of this material, ensuring it can withstand extreme operational contexts.
Tensile Strength Analysis
Tensile strength refers to the maximum amount of tensile (pulling) stress that a material can endure before failure. Inconel 718 exhibits exceptional tensile strength, often reaching about 1,300 MPa at room temperature. This property enables it to perform reliably in high-stress environments, such as gas turbines and jet engines. The alloy’s strength improves significantly after appropriate heat treatments, which also play a role in optimizing its microstructure.
Details like grain structure and phase distribution influence the tensile strength. For instance, the presence of precipitates contributes to both strength enhancement and toughness. It is important to conduct consistent tests to verify the tensile properties of fabricated components to minimize the risk of operational failures.
Yield Strength and Elongation
Yield strength is another critical property, indicating the stress at which a material begins to deform plastically. Inconel 718 shows a yield strength of approximately 950 MPa at ambient temperature. This allows designers to create components that maintain their shape under load, a crucial consideration in aerospace applications where weight and material integrity matter.
Elongation is the measure of deformation of a material when subjected to stress. Inconel 718 achieves an elongation of around 30%, meaning it can undergo significant deformation before breaking. This is important in applications where the material may experience unexpected loads or impacts.
The combination of high yield strength with substantial elongation makes Inconel 718 an ideal choice for applications that require both durability and flexibility under stress.
Fatigue Resistance
Fatigue resistance is a vital quality for materials subjected to cyclic loading conditions. Inconel 718 demonstrates exceptional fatigue resistance, allowing it to perform well under repeated stress without failing. This property is especially relevant in environments like aerospace and energy production, where components face continuous operational cycles.
Laboratory fatigue tests often reveal that Inconel 718 maintains its performance even after numerous cycles, surpassing many other alloys. Engineers rely on this property to ensure long service life, contributing to reduced maintenance costs and improved safety metrics in critical applications.
"Inconel 718's superior mechanical properties make it indispensable in sectors where materials need to endure strain without compromising structural integrity."
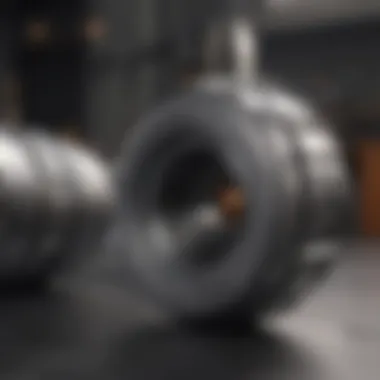
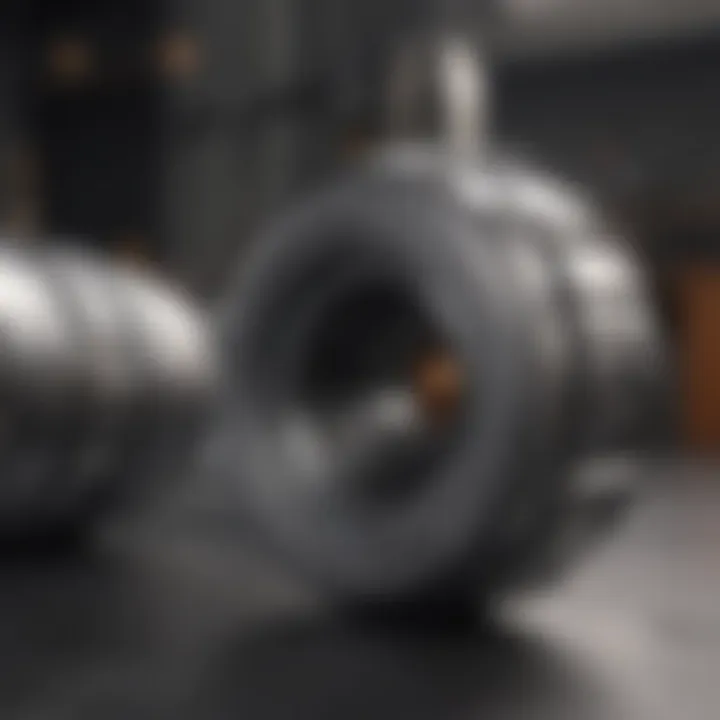
In summary, the mechanical properties of Inconel 718—such as its tensile strength, yield strength, elongation, and fatigue resistance—are the backbone of its impressive performance in demanding industries. These characteristics mark it as an exceptional material choice for modern engineering challenges.
Corrosion Resistance of Inconel
Corrosion resistance is a critical attribute for materials used in harsh environments. Inconel 718, a nickel-chromium alloy, demonstrates impressive capabilities in this area. Understanding the corrosion resistance of Inconel 718 is essential for engineers and researchers involved in various industries. The alloy is specifically designed to withstand aggressive conditions, including exposure to high temperatures and corrosive chemicals.
One major benefit of Inconel 718's corrosion resistance is its ability to maintain mechanical integrity over time. Corrosion can weaken materials, leading to failures in critical applications. Inconel 718's high nickel content promotes good oxidation resistance, which allows the alloy to perform efficiently even in environments that would damage lesser materials. This property makes it a reliable choice in sectors such as aerospace and energy.
Oxidation Resistance
Oxidation is a common form of corrosion that occurs when metals react with oxygen in the environment. Inconel 718 exhibits excellent oxidation resistance, particularly at elevated temperatures. The formation of a protective oxide layer on its surface minimizes further oxidation, which is critical when exposed to hot gases or steam.
The alloy's ability to resist oxidation is particularly beneficial in the aerospace industry, where components may face extreme temperatures during operation. The stability of this oxide layer ensures that Inconel 718 retains its mechanical properties and does not degrade in performance.
Inconel 718 remains effective under extreme temperatures, making it a top choice for aerospace and energy applications.
Acidic Environment Performance
In addition to oxidation, exposure to acidic environments presents a significant challenge for many materials. Inconel 718 offers commendable resistance to various acidic conditions, which is vital in the energy sector, especially in oil and gas extraction. The alloy effectively resists pitting and stress corrosion cracking, two major concerns in corrosive settings.
Furthermore, the composition of Inconel 718 allows it to withstand different types of acids without deteriorating. Industries requiring durable materials for pipelines and equipment handling acidic substances benefit immensely from this characteristic.
In summary, Inconel 718’s corrosion resistance, driven by its oxidation resistance and performance in acidic environments, positions it as a critical material in challenging applications. Its resilience not only enhances the safety of operations but also prolongs the lifespan of components in demanding sectors.
Applications of Inconel
The application of Inconel 718 is paramount in various industries due to its unique properties. This alloy stands out for its strength, particularly at elevated temperatures. Its corrosion resistance enhances durability, making it suitable for harsh environments. Understanding these applications can aid professionals in selecting the right materials for their projects. Additionally, the implications of using Inconel 718 stretch beyond mere performance; they also encompass economic and ecological considerations.
Aerospace Industry Uses
In the aerospace sector, Inconel 718 plays a crucial role due to its outstanding mechanical properties. Components made from this alloy are often used in jet engines, particularly in areas exposed to extreme temperatures and stresses. Examples include turbine wheels, spacers, and other essential parts that require both heat resistance and structural integrity.
Furthermore, its lightweight nature combined with strength means it can trim down the overall weight of aircraft without sacrificing safety or performance. This balance is vital as modern aerospace engineering seeks to maximize fuel efficiency while minimizing emissions. Specifically, the specifications of Inconel 718 allow it to withstand oxidation at high temperatures, which is essential for ensuring reliability over long service periods in aviation.
Energy Sector Applications
In the energy sector, Inconel 718 has significant uses, especially in power generation. Its properties make it ideal for components in gas turbines and nuclear reactors. Within these demanding environments, the ability to maintain strength and resist corrosion is particularly critical. For instance, turbines suffer from fatigue loads and high thermal gradients. Inconel 718 ensures high performance and long life, which translates to lower maintenance costs and increased operational uptime.
Moreover, Inconel 718's performance in sour gas applications, where materials can degrade rapidly, is noteworthy. It is resilient against sour environments, which makes it favorable in the oil and gas industry. This resilience means that structures exposed to harsh compositional conditions can maintain their integrity longer, providing safety to workers and mitigating catastrophic failures.
Industrial Machinery Utilization
In industrial machinery, Inconel 718 is employed in fabrication processes where extreme heat and mechanical stress are common. Its durability makes it suitable for machining tools and dies. Additionally, its resistance to thermal shock enhances its functionality in manufacturing equipment.
Many industries also utilize Inconel 718 in the production of pumps, valves, and fittings. These components benefit from its resistance to both high pressures and temperatures. Operators can rely on machinery built with this alloy to perform consistently under challenging conditions, thus reducing downtime and operational costs.
In summary, Inconel 718's applications span critical sectors such as aerospace, energy, and industrial machinery. The versatility and robustness of the alloy make it a material of choice, allowing industries to innovate and improve efficiencies. Understanding these applications not only aids design choices but also informs future developments in various technological fields.
Performance under Extreme Conditions
Performance under extreme conditions is a crucial aspect of Inconel 718 that highlights its capabilities in unforgiving environments. This section examines how this alloy stands up to demanding scenarios, such as high temperatures and cryogenic applications. Understanding these performance metrics is vital for industries that rely on materials that can maintain integrity under challenging situations.
High-Temperature Stability
Inconel 718 exhibits remarkable stability at elevated temperatures, a characteristic that makes it suitable for components operating in conditions exceeding 700 degrees Celsius. The alloy maintains its mechanical properties even when subjected to extended periods of heat, a significant advantage in settings like jet engines and gas turbines. High-temperature stability arises from the alloy's unique microstructure, which forms through its specific heat treatment processes. This stability reduces the risk of deformation or failure when the material is subjected to thermal stress.
The alloy’s ability to withstand oxidation is another essential factor in high-temperature environments. Inconel 718 develops a protective oxide layer that serves to mitigate further oxidation. This feature extends the material's lifespan and reliability in operational settings.
Applications in the aerospace sector underscore the significance of high-temperature stability:
- Jet engine components: Turbine blades, combustion chambers.
- Gas turbine rotors: For power generation, where thermal consistency is critical.
Cryogenic Applications
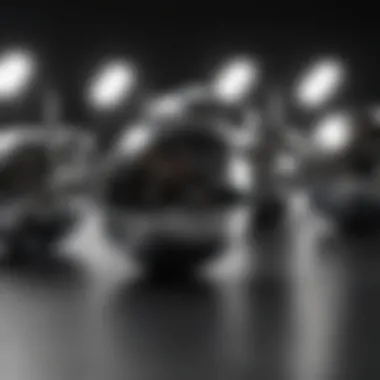
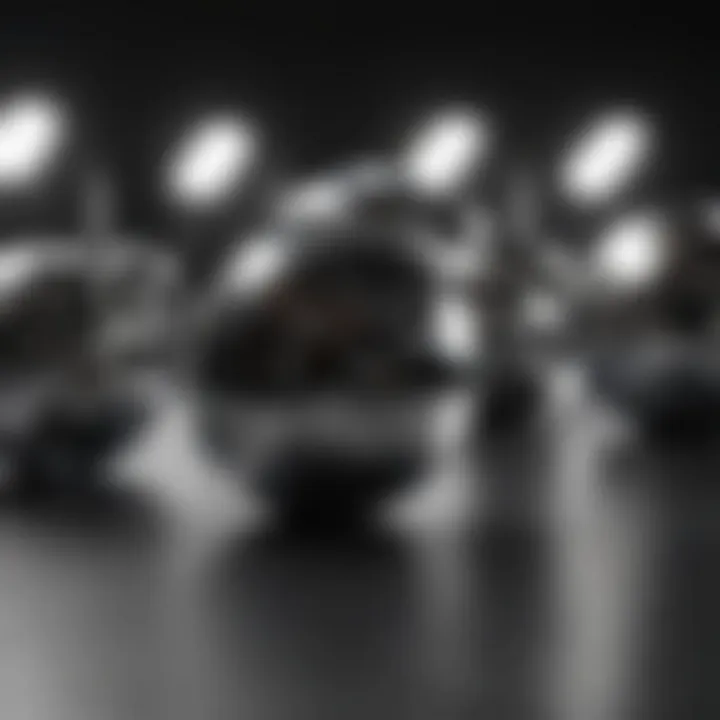
Inconel 718 is not only remarkable at high temperatures but also efficient in cryogenic conditions. Its excellent low-temperature performance is beneficial in industries like aerospace and liquefied natural gas. The alloy remains ductile and strong even at temperatures approaching absolute zero.
One of the notable attributes of Inconel 718 under cryogenic conditions is its resistance to brittle fracture. This is vital in applications with sudden temperature shifts, where other metals might fail. The alloy's composition enables it to retain toughness and maintain mechanical integrity, crucial in areas such as:
- Spacecraft components: Fuel tanks and engine parts subjected to extreme cold.
- Cryogenic storage tanks: Essential for storing gases like nitrogen or helium.
"The ability of Inconel 718 to perform under both high and low temperatures expands its utility, making it a versatile choice for various extreme applications."
Comparative Analysis with Other Alloys
The comparative analysis of Inconel 718 with other alloys is crucial for understanding its unique properties and applications. This section focuses on the strengths and limitations of Inconel 718 in relation to its close counterparts. Key comparisons will help in informing users whether they need to choose Inconel 718 over other materials, based on mechanical properties, corrosion resistance, and cost.
Inconel vs Inconel
Inconel 625 and Inconel 718 are renowned nickel-chromium alloys, both celebrated for their high strength and excellent corrosion resistance. However, they have distinct features that influence their usage significantly.
- Chemical Composition: Inconel 625 generally contains a higher proportion of molybdenum, giving it enhanced resistance to pitting and crevice corrosion. In contrast, Inconel 718 offers superior tensile strength due to its balanced alloying elements, specifically niobium and titanium.
- Mechanical Properties: When it comes to mechanical performance, Inconel 718 tends to outperform Inconel 625 in terms of yield strength, particularly at elevated temperatures. This property makes Inconel 718 favorable for aerospace applications where components must endure high stress under heat.
- Fabrication: Inconel 625 is often easier to weld than Inconel 718. This is due to its lower susceptibility to cracking during the welding process. However, Inconel 718 benefits from unique heat treatment processes that can enhance its strength considerably.
In summary, the choice between Inconel 625 and Inconel 718 depends on the specific requirements of the application, such as the operating environment, temperature fluctuations, and mechanical load expectations.
Alternative Materials
While Inconel 718 remains a top choice for many high-performance applications, it is essential to consider alternative materials that might offer different benefits. These alternatives can be explored based on specific use cases and demands.
- Titanium Alloys: Offering a exceptional weight-to-strength ratio, titanium alloys can be desirable when reducing weight is a primary concern, particularly in aerospace applications. However, they are generally more expensive and may not provide the same level of high-temperature performance as Inconel 718.
- Stainless Steels: Certain stainless steels provide excellent corrosion resistance, making them suitable for various applications. However, they often lack the high-temperature strength that is characteristic of Inconel 718.
- Other Nickel Alloys: Alloys such as Hastelloy or Inconel 625 can be considered based on environmental exposure factors. They may offer enhanced resistance to specific corrosive environments, but may not match the strength of Inconel 718 under high-stress conditions.
When evaluating alternatives to Inconel 718, it is vital to assess intended applications and environments to ensure optimal material selection. The unique properties of each material can significantly impact performance and longevity.
"Selecting the right alloy for a given application can be the difference between success and failure in performance."
By understanding the various qualities and limitations of Inconel 718 and its competitors, professionals in fields such as aerospace, energy, and industrial machinery can make informed decisions that align with their specific requirements.
Future Prospects for Inconel
The future of Inconel 718 holds significant potential, particularly as industries continue to pursue materials that combine strength, corrosion resistance, and adaptability. The ongoing evolution in manufacturing methods and identification of new applications further showcase the alloy’s relevance in modern technology. The implications of these advancements suggest that Inconel 718 may become even more integral to various sectors, spanning from aerospace to energy production.
Innovations in Manufacturing
Continual innovation in manufacturing techniques is critical for enhancing the capabilities of Inconel 718. The advent of additive manufacturing, commonly known as 3D printing, is one such innovation that provides unique opportunities. This method allows for the creation of complex geometries that traditional methods struggle to achieve. For instance, using laser-based techniques, manufacturers can fabricate parts with reduced waste and high precision. This can lead to lower production costs and shorter lead times, thereby making Inconel 718 more accessible to various industries.
Improvement in thermal processing also plays a vital role. Advances in heat treatment procedures can produce even finer microstructures, thereby enhancing mechanical properties. This has the potential to allow for increased tensile strength or enhanced fatigue resistance under extreme conditions, essential for industries that operate in challenging environments.
Emerging Applications
Emerging applications for Inconel 718 are broad and diverse. The aerospace industry is an early adopter, utilizing this alloy for components such as turbine engines and exhaust systems due to its exceptional performance under high-stress conditions. However, the energy sector is also beginning to explore its advantages, particularly in manufacturing parts for gas and steam turbines.
Moreover, Inconel 718 has potential in the fields of medical technology and automotive applications. As innovation drives the need for lightweight, durable materials, this alloy’s properties make it suitable for components that can withstand harsh environments, including medical implants and high-performance vehicle parts.
In summary, the future prospects for Inconel 718 are bright. Ongoing innovations in manufacturing and a growing interest in diverse applications are likely to ensure its place as a pivotal material in various high-tech industries. The collective push towards sustainability and efficiency will further accelerate the adoption of this unique alloy.
End and Summary
In this article, we have explored Inconel 718, a remarkable nickel-chromium alloy that stands out for its impressive strength and corrosion resistance. We have delved into various facets of this material, covering its chemical composition, manufacturing processes, mechanical properties, and diverse applications across several industries. Understanding these elements is crucial for professionals and researchers who work with or study advanced materials.
In the aerospace industry, Inconel 718 is highly valued for its ability to withstand extreme temperatures and stresses, making it ideal for engine components and turbine parts. Likewise, the energy sector benefits from Inconel 718’s resilience to harsh conditions, leading to its use in gas turbines and nuclear reactors. Industrial applications further underline its versatility, showcasing how this alloy can meet the rigorous demands of various sectors.
Here are some specific elements and benefits that stood out:
- Durability: Inconel 718's exceptional mechanical properties ensure longevity in challenging environments.
- Heat and Corrosion Resistance: This alloy performs admirably in both high-temperature and corrosive atmospheres, making it a preferred choice in critical applications.
- Manufacturability: Advances in manufacturing processes like hot working and heat treatment enhance its usability and reliability.
Overall, the synthesis of these aspects gives insight into why Inconel 718 remains a leading material in modern engineering solutions. The future prospects suggest ongoing innovations will further enhance its applications and efficiency.
Key Takeaways
- Inconel 718 is essential in industries requiring high performance materials.
- The alloy’s composition provides unique mechanical and thermal properties.
- Future innovations could further expand its usability, indicating that ongoing research is necessary.
Final Thoughts
Inconel 718 exemplifies how materials science continues to evolve and adapt to the needs of high-demand industries. It holds significant potential for future advancements, possibly leading to stronger and more efficient products. Understanding its properties not only benefits engineers and researchers but also fosters innovation across multiple sectors. For those involved in material selection and application, recognizing Inconel 718’s strengths is vital for both current and future projects.