Ultrahigh Strength Steels: Properties and Innovations
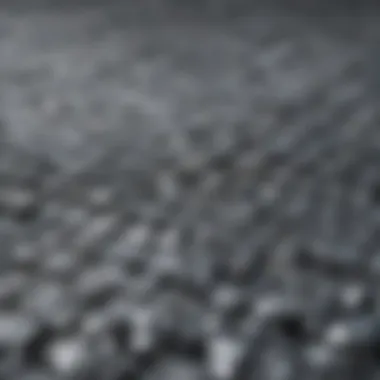
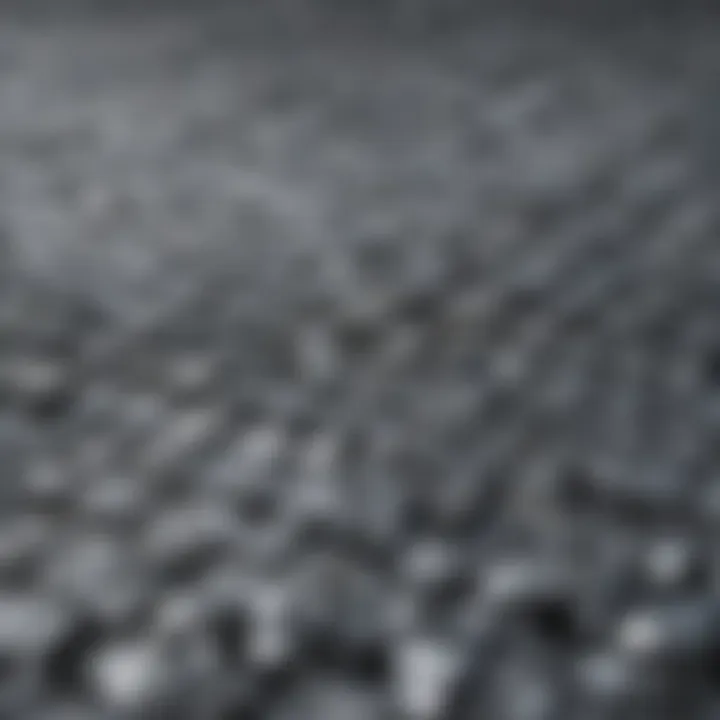
Intro
Ultrahigh strength steels (UHSS) are at the forefront of modern materials science, offering remarkable properties that significantly enhance their utility in engineering applications. These materials have gained traction particularly in industries where strength and durability are paramount. When we talk about UHSS, we're not just referencing materials with high tensile strength. We're also delving into their unique characteristics that make them suitable for a variety of demanding roles in construction, automotive, aerospace, and defense sectors.
The importance of UHSS cannot be overlooked, especially in today’s rapidly changing technological landscape. With increasing demands for safety, performance, and efficiency, engineers and manufacturers are pressed to find materials that not only meet but exceed traditional performance metrics. Here, UHSS rise to the occasion by offering tensile strengths often exceeding 1000 MPa, alongside favorable weight-to-strength ratios. This means structures and vehicles can be built lighter yet stronger.
In this article, we will unravel the complexities of UHSS, starting from its fundamental properties and moving through its diverse applications. We will also explore recent innovations in alloy development and manufacturing processes. With a focus on recent trends, from the methods used in production to the interdisciplinary connections shaping the future of these materials, this discussion aims to shed light on both the theoretical underpinnings and the practical realities of ultrahigh strength steels.
Foreword to Ultrahigh Strength Steels
The field of metallurgy has long held a place of importance in engineering, and ultrahigh strength steels (UHSS) are now at the forefront of materials innovation. As industries grow and demand for advanced materials increases, understanding UHSS has become essential. This section will illuminate the significance of these materials, not just in theory but also in application.
Ultrahigh strength steels are a class of steel alloys characterized by their remarkable tensile strength surpassing 1000 megapascals. They are extensively utilized across various industries, from automotive to aerospace, shaping the future of engineering. The primary benefit lies in their ability to provide superior strength while maintaining lower weight compared to traditional materials. This contributes to more efficient designs—vital in sectors where performance and safety are paramount.
Definition and Characteristics
In essence, ultrahigh strength steels are engineered for maximum performance. Their defining characteristic is exceptional tensile strength, but they also possess key features that further enhance their applicability:
- High Yield Strength: This property allows UHSS to withstand significant loads while maintaining shape.
- Ductility: Even though they are strong, many UHSS grades retain enough ductility for forming operations, making them versatile.
- Corrosion Resistance: Some UHSS variants are treated to resist rust, adding longevity in hostile environments.
These characteristics enable UHSS to meet the ever-increasing demands of various applications. The diversity in alloy composition allows for tailored properties, proving beneficial in specific scenarios, whether it’s managing the rigors of heavy machinery or enhancing the safety of passenger vehicles. In summary, the definition of UHSS encompasses their strength, durability, and adaptability—qualities that make them invaluable in modern engineering.
Historical Development
A look back in time shows that the evolution of ultrahigh strength steels is linked to the advancements in industrial needs. The idea of strengthening steel isn’t new; however, the path to achieving ultrahigh strength has had its share of milestones:
- 1920s-1950s: The foundational concepts of alloying began to take root, setting the stage for what would become UHSS.
- 1960s-1980s: Significant advances occurred during this period, particularly with the introduction of alloying elements such as molybdenum and nickel, leading to stronger, tougher steels.
- 1990s-present: Recent innovations focus on refining microstructures and processing techniques, allowing for even greater strength and enhanced performance under extreme loads.
Overall, the historical narrative of UHSS is one of continuous refinement, with each decade contributing to a more profound understanding of how to manipulate steel's properties. As engineers and researchers pressed into the unknown, the results bore fruit in the form of materials that not only met but exceeded the expectations of various industries, paving the way for future explorations.
Composition of Ultrahigh Strength Steels
The composition of ultrahigh strength steels is a fundamental area that deserves close examination, for it’s the intricate balance of elements that truly sets these materials apart. The unique properties of these steels stem from their specific atomic arrangements and the interactions between various alloying elements. Understanding this composition is vital, as it determines not only the raw strength of the steel but also its behavior under different conditions and applications.
Key Alloys and Elements
When diving into the composition of ultrahigh strength steels, one cannot overlook the key alloys and elements that give these materials their exceptional qualities. Commonly, these steels contain carbon, manganese, chromium, molybdenum, and vanadium among other elements. Each of these components plays a specific role:
- Carbon: Typically ranging from 0.2% to over 1%, carbon is the cornerstone for strength. It enhances hardening but can also affect ductility.
- Manganese: Often introduced at about 1% to 2%, manganese improves hardenability and helps stabilize austenite during heat treatment, which is crucial for achieving desired mechanical properties.
- Chromium: Present in smaller percentages, chromium contributes to corrosion resistance while also enhancing the hardening process.
- Molybdenum: Generally included to improve resistance to softening at high temperatures.
- Vanadium: Though added in trace amounts, vanadium has a substantial impact. It refines grain structure, leading to improved toughness and strength.
These elements work together in a meticulous fashion, each adding a layer of strength or altering the microstructural attributes of the steel. The interconnectedness of these alloys often determines the steel’s ultimate performance, which is why exploring their balance is critical for engineers and manufacturers alike.
Role of Microstructure
What sets ultrahigh strength steels apart isn’t just their elemental composition, but also the microstructure that results from the interplay of these elements. The arrangement of atoms and the formation of phases greatly influence mechanical properties. For instance, a fine-grained structure results from controlled cooling processes and alloying additions, which in turn ensures impressive toughness.
Moreover, the role of microstructure cannot be overstated.
- Grain Size: Smaller grains enhance strength through what is known as the Hall-Petch relationship. The more grains per unit area, the greater the strength.
- Phase Distribution: The presence of different phases such as martensite or ferrite can determine ductility versus hardness. A careful balance needs to be maintained to achieve optimal performance in application.
As we look at innovations in processing techniques, there's ongoing interest in how advanced methods like thermomechanical processing can further refine the microstructure of ultrahigh strength steels. This exploration is not just academic; it has real-world implications for various industries, particularly automotive and aerospace, where safety and performance are paramount.
Understanding the composition and microstructure of ultrahigh strength steels is vital for harnessing their full potential in cutting-edge applications.
In summary, grasping the significance of composition and the pivotal role of microstructure lays the groundwork for utilizing ultrahigh strength steels to their fullest capabilities across today’s demanding applications.
Mechanical Properties
Mechanical properties are a cornerstone of the discussion surrounding ultrahigh strength steels. Their significance transcends mere definitions, embedding themselves deeply in the practical applications of these materials across industries. When engineers and designers consider adopting ultrahigh strength steels, they inherently evaluate three key aspects: tensile strength, ductility, hardness, and fracture toughness. Each of these elements informs their suitability for various applications, enabling advancements in design and performance throughout sectors such as automotive, construction, and aerospace.
Advancing the understanding of these properties not only helps in identifying the most appropriate alloy for a specific need but also in maximizing the benefits these materials provide. Differentiating ultrahigh strength steels from conventional materials relies heavily upon their enhanced mechanical characteristics, which warrant a deeper examination of tensile strength, hardness, and fracture toughness.
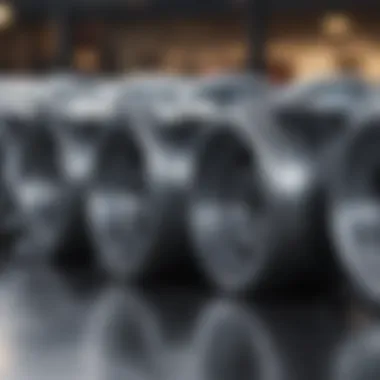
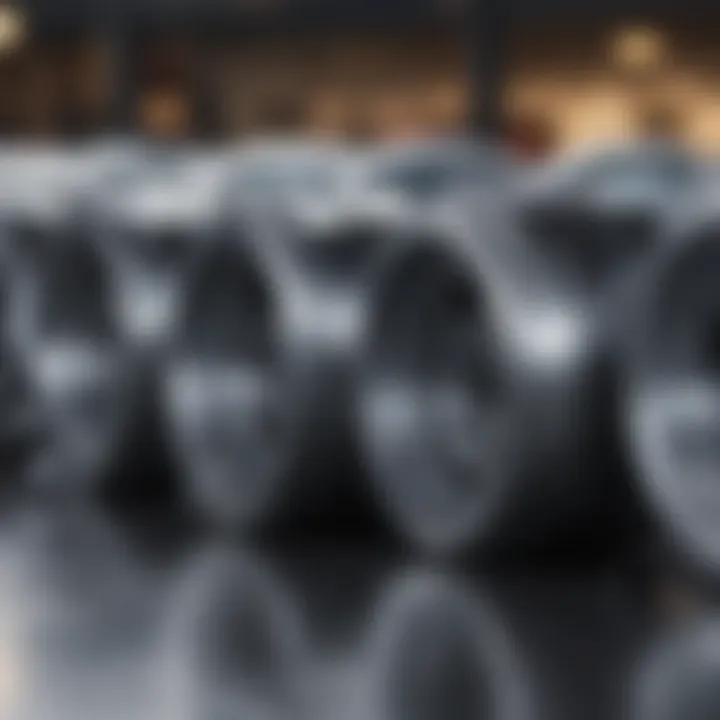
Tensile Strength and Ductility
Tensile strength serves as one of the most critical barometers of a material’s capability under stress. Ultrahigh strength steels stand out due to their remarkable tensile strength, often surpassing 1000 MPa. This characteristic is pivotal, especially when these materials are used in applications where they may face significant loads or forces over time.
However, it isn’t just about being strong; ductility plays a vital role in ensuring that these materials can deform without fracturing under high stress. The balance between tensile strength and ductility is essential. An overly rigid steel may crack sooner, while an excessively ductile one might not withstand the intended loads. Many ultrahigh strength steels exhibit a sweet spot where they maintain high strength alongside adequate ductility, making them versatile for critical components in cars or structures.
For example, Advanced High-Strength Steels (AHSS) leverage this balance effectively. They are engineered to provide high strength along with shareable ductility, making them optimal for crash safety in vehicles. This shows that manufacturers increasingly prioritize combining properties to suit the needs of modern design and safety standards.
Hardness and Wear Resistance
The hardness of ultrahigh strength steels often correlates directly with their performance in applications where wear and friction are prominent. This property is vital in sectors like manufacturing where machinery is subjected to harsh operating conditions. Harder steels tend to resist surface damage better and thus broaden the lifecycle of parts made from them.
Wear resistance can dramatically influence operational efficiency and cost-effectiveness over time. For instance, in the mining industry, drill bits and equipment made from these steels can survive much longer against abrasive materials compared to standard steels. The ability to maintain performance under extreme conditions is frequently tied to the hardness of the steel.
Moreover, there are specialized treatments employed to enhance both hardness and wear resistance. Processes like case hardening or surface hardening create a resilient surface layer, providing an additional level of protection without compromising the steel’s core properties.
Fatigue and Fracture Toughness
Lastly, fatigue and fracture toughness provide insight into how materials behave under cyclic stresses and their tendency to fail over time. These attributes are often assessed together as they reveal how ultrahigh strength steels resist cracking and propagating failures during service. Fatigue resistance is particularly crucial, for it ensures that components will not fail after repeated application of loads, which is common in many industrial settings.
The fracture toughness of these steels is likewise critical as it signifies the steel’s ability to withstand flaw propagation under stress. Engineers must understand how small defects can lead to catastrophic failure, especially in structures and components that operate under extreme conditions. Improved fracture toughness enhances reliability, making ultrahigh strength steels essential in safety-critical applications.
Manufacturing Techniques
The manufacturing techniques used in creating ultrahigh strength steels (UHSS) hold immense significance as they directly influence the material's properties, performance, and applicability across various industries. Effective processing can enhance the strength, ductility, and overall performance of these steels, making them suitable for demanding environments. Understanding these techniques allows for tailored solutions that meet precise engineering specifications, ensuring that UHSS continues to play an essential role in modern applications.
Heat Treatment Processes
Heat treatment is a critical step in the production of ultrahigh strength steels, serving as a cornerstone for achieving the desired mechanical properties. This process usually involves heating the steel to specific temperatures, maintaining that temperature for a predetermined duration, and then cooling it at controlled rates.
The primary heat treatment methods for UHSS include:
- Annealing: Softens the material, making it easier to work with. It also relieves internal stresses developed during manufacturing.
- Tempering: Applied after quenching, this step reduces brittleness and enhances toughness. It is essential for balancing strength and ductility.
- Normalization: Improves grain structure, leading to enhanced toughness and uniformity across the material.
Each method has its tailored effects, contributing to adjustments in hardness, toughness, and other critical features. For instance, tempering can shift the balance toward more ductile properties, making the final product suitable for more flexible applications.
"The effectiveness of heat treatment processes lies in their ability to manipulate microstructural characteristics, such as grain size and phase transformation, which directly correlates to the performance of ultrahigh strength steels."
Quenching and Tempering
Quenching and tempering are often seen as complementary processes in the production of ultrahigh strength steels. Quenching involves rapidly cooling the hot steel—often in water, oil, or air—to set its structure. This sudden temperature drop can lead to a hardened state, significantly boosting tensile strength but potentially introducing brittleness.
Following quenching, tempering is employed. The material is reheated to a temperature lower than the quenching temperature, allowing for the relieving of stresses while retaining much of the hardness gained during quenching. As a result, a more balanced mix of strength and toughness is achieved, making it well-suited for load-bearing applications.
Key aspects to consider:
- The quenching medium (water, oil, etc.) affects the cooling rate and consequently the hardness.
- The tempering temperature can dramatically influence the resulting properties, with higher temperatures downgrading strength but improving toughness.
Welding and Joining Methods
Welding and joining represent another vital component in working with ultrahigh strength steels, as they must maintain the integrity and properties of the steel throughout fabrication. Given their high strength, UHSS can be more complex to weld than standard steels due to the susceptibility to hardening, warping, and cracking, notably post-weld.
Common welding techniques include:
- Gas Metal Arc Welding (GMAW): This method provides ground efficiency and higher welding speeds but requires careful control of heat input.
- Tungsten Inert Gas (TIG) welding: Offers precision, allowing for finer adjustments but generally is slower.
- Laser welding: A newer technique providing exceptional control over the heat application and resulting joint integrity.
When performing welding, it’s essential to select appropriate filler materials and preheating strategies to minimize potential issues. Failure to account for these can yield weaker joints, undermining the advantages of using ultrahigh strength steels in applications where reliability is paramount.
Understanding these manufacturing techniques is crucial for engineers and manufacturers to harness the full potential of ultrahigh strength steels, ultimately leading to improved design and performance in an array of applications.
Applications of Ultrahigh Strength Steels
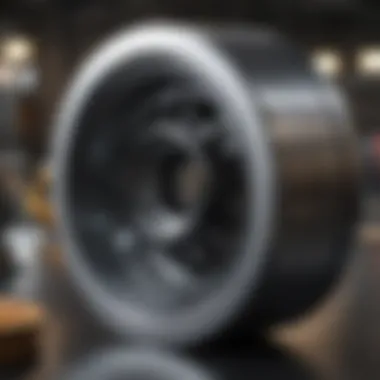
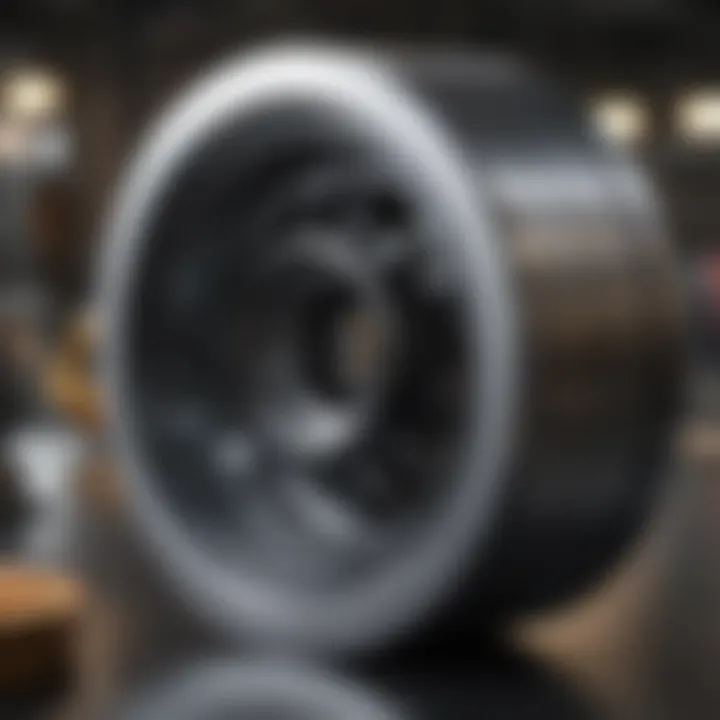
The applications for ultrahigh strength steels (UHSS) are numerous and varied, illustrating their significance in contemporary engineering. Their unique mechanical properties, such as high tensile strength combined with excellent ductility, have made them a go-to material in fields where safety, durability, and performance are non-negotiable. With industries looking to enhance efficiency and reduce weight without sacrificing strength, UHSS emerges as a critical player. Understanding the different applications not only reveals the versatility of these steels but also their potential in challenging environments.
Automotive Industry
In the automotive sector, lightweight materials are the name of the game. Cars must be built to withstand crashes while also being fuel-efficient. The integration of UHSS allows manufacturers to design lighter vehicles without compromising safety. For instance, using Ahmedica 800 steel—the strongest commercially available steel—can reduce the weight of components such as chassis and body frames. This reduction contributes significantly to improved fuel economy and reduced CO2 emissions.
Furthermore, UHSS provides improved crashworthiness. When you think about it, in an accident, the force needs to be absorbed by the car. The high yield strength helps in deforming less during crashes, which keeps passengers safer. Automotive giant Ford has incorporated advanced high-strength steels, like the 1020 mild steel, to achieve better passenger protection without excessive weight.
Construction and Structural Applications
The construction industry has also turned to ultrahigh strength steels for their robust characteristics. Steel frames constructed with UHSS can carry loads that regular steels might not handle well. This ability also translates into slimmer structures, which can save space and materials.
- High-rise buildings: Skyscrapers are a prime example. Using UHSS means structures can go higher without the added bulk, achieving skyline-defining heights without risking stability.
- Bridges: An area where you don’t want to skimp on strength is bridges. The use of UHSS can minimize the material required while maintaining structural integrity.
Companies like Skanska have harnessed the potential of UHSS in their bridge designs, ensuring both safety and elegance in their projects. This leads to sustainable construction practices that resonate with modern demands for ecological efficiency.
Aerospace Engineering
In the realm of aerospace, where weight is critical, ultrahigh strength steels find their niche. The ever-advancing field of aerospace engineering demands materials that can withstand extreme conditions—think of the fluctuating temperatures and pressures during flights. UHSS provides an optimal combination of lightweight and strength, which is vital for aircraft components.
The use of UHSS in wing structures and landing gear enhances durability while allowing manufacturers to reduce overall aircraft weight. Boeing and Airbus, for instance, have explored UHSS variants to improve fuel efficiency while maintaining safety standards. In terms of performance, these materials endure significant stress and offer good fatigue properties, essential for the rigorous demands of flying.
"The integration of ultrahigh strength steels marks a significant advancement, pushing the boundaries of what we can achieve in automotive, construction, and aerospace sectors."
Overall, the significance of ultrahigh strength steels in these three major sectors underscores their pivotal role in driving innovation and efficiency. With continued research and development, their applications are likely to expand even further, redefining materials engineering in the years to come.
Challenges in Utilizing Ultrahigh Strength Steels
Ultrahigh strength steels (UHSS) offer remarkable properties that make them desirable in various engineering applications. However, their implementation doesn't come without hurdles. Understanding the challenges faced is critical for optimizing their use in industries ranging from automotive to aerospace. The key issues include cost implications, processing difficulties, and performance under extreme conditions. Addressing these challenges is essential for maximizing the benefits of UHSS and ensuring their successful integration into modern engineering solutions.
Cost Implications
The cost of ultrahigh strength steels can be significantly higher than that of conventional steels. This increased expense arises from various factors associated with the materials and processes involved in their production. For instance, the complexity in alloy design often leads to an increase in raw material costs. Moreover, manufacturing techniques like heat treatment require careful control, which can drive up operational expenses.
- Material costs: The alloys used in UHSS can include rare elements, which push up pricing.
- Processing costs: Specialized manufacturing processes contribute to higher expenses, impacting the overall project budget.
- Life cycle cost: Although the initial outlay may be high, UHSS can lead to long-term savings due to increased durability and reduced weight.
In sum, while the upfront investment required for ultrahigh strength steels may be daunting, industry professionals often weigh this against the materials’ exceptional performance characteristics.
Processing Difficulties
Working with UHSS poses numerous processing challenges that can hinder their widespread adoption. The steel's unique characteristics, such as extreme hardness and tensile strength, can complicate machining, welding, and forming processes.
- Welding: High strength reduces the ability to weld easily, requiring specialized techniques that can lead to weak joints if not executed properly. For example, some UHSS require pre-heating before welding to avoid cracking.
- Machining: Traditional machining methods may not suffice. Specialized cutting tools and methods are needed to handle the hardness of these steels, leading to increased tool wear and downtime.
- Forming: The high strength-to-weight ratio may impact the ability to form parts accurately. It may require precise adjustments in tool design and process parameters to achieve the desired shapes without compromising the material's integrity.
Given these hurdles, thorough knowledge of the processing techniques is vital for optimizing the usage of UHSS in production.
Performance Under Extreme Conditions
One of the touted benefits of ultrahigh strength steels is their superior performance in challenging environments. However, performance under extreme conditions does present its own set of challenges. Such conditions include high temperatures, corrosive environments, and dynamic loading scenarios.
- Temperature Sensitivity: UHSS can experience a reduction in toughness or should not be exposed to high temperatures for extended periods. This sensitivity needs careful assessment during design phases where heat might be a factor, like in automotive components.
- Corrosion Resistance: While some ultrahigh strength steels have a remarkable strength profile, they may not always perform well in corrosive environments unless treated or alloyed with corrosion-resistant elements. This additional requirement can increase material costs further.
- Dynamic Loads: Components made from UHSS exposed to dynamic loading, such as those in fast-moving machinery or transportation, need to undergo rigorous testing to ascertain their fatigue life. It involves extensive fatigue testing and finite element analysis to ensure safety and longevity.
Understanding these performance drawbacks is fundamental for engineers to create designs that fully leverage the advantages of ultrahigh strength steels while mitigating their limitations.
In summary, while challenges exist in utilizing ultrahigh strength steels, their properties can significantly contribute to design innovations when managed properly. Research and development efforts are crucial in overcoming these hurdles to expand their application spectrum.
Recent Innovations in Ultrahigh Strength Steels
The ongoing evolution of ultrahigh strength steels is a critical aspect of materials science. These innovations open doors to numerous applications, ranging from automotive to aerospace, showcasing their versatility and strength. As industries evolve, so does the need for materials that can withstand extreme conditions while enhancing performance and sustainability. Thus, focusing on recent innovations in alloy design, novel processing techniques, and sustainable production methods is vital.
Advancements in Alloy Design
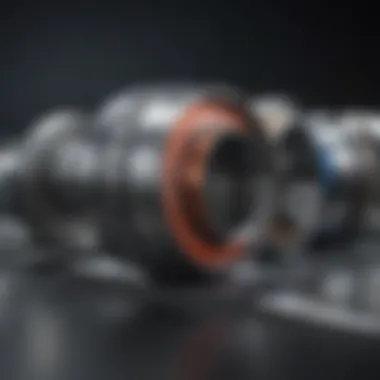
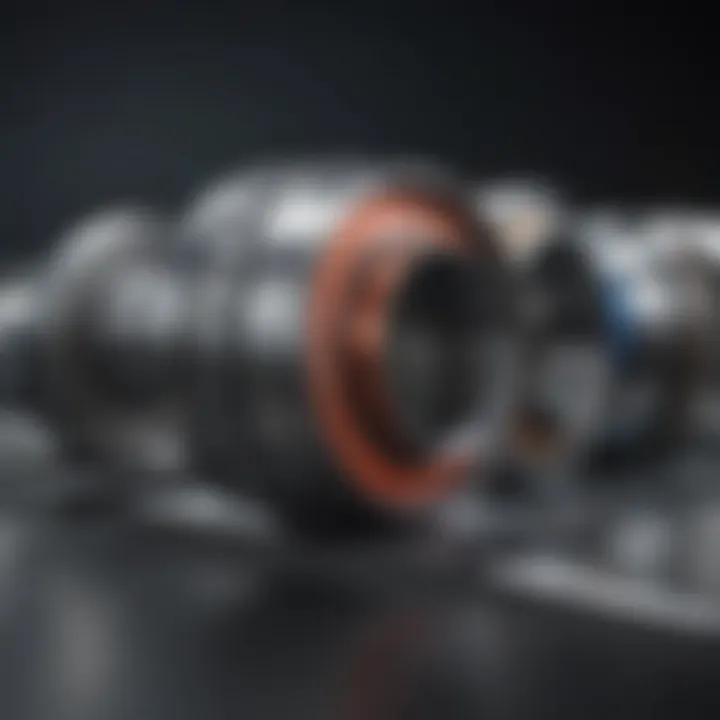
Alloy design plays a significant role in the performance of ultrahigh strength steels. Over the past few years, researchers have explored a range of new alloying elements, leading to the creation of enhanced steel grades. For instance, the incorporation of elements such as manganese and chromium can increase both strength and ductility. This adjustment allows for the production of steels that maintain toughness while exhibiting remarkable resistance to corrosion and wear.
"Innovations in alloy design are pushing the boundaries of what's possible in materials engineering, enabling the development of steels that meet rigorous industrial standards and expectations."
Some notable advancements include the development of High-Strength Low-Alloy (HSLA) steels, which integrate specific percentages of carbon, manganese, and nickel to improve mechanical properties. This trend towards tailoring the microstructure not only aids in enhancing the performance but also contributes to saving weight in applications such as vehicle construction.
Novel Processing Techniques
Processing techniques are just as vital as the alloys themselves in maximizing the effectiveness of ultrahigh strength steels. Advancements here focus primarily on refining manufacturing processes, such as additive manufacturing and new quenching methods. For example, additive manufacturing allows for more intricate designs and shapes that were previously impossible to achieve, thereby enhancing the material's applications.
New quenching methods, like austempering, have demonstrated significant promise. This technique allows for the simultaneous improvement of strength and toughness, enabling manufacturers to produce components that can endure severe operational environments without deforming or failing. Moreover, a lot of attention goes into non-destructive testing methods that can be applied post-processing to ensure material integrity without compromising final product properties.
Sustainable Production Methods
As the world increasingly values sustainability, the steel industry is not lagging behind. Recent innovations in sustainable production methods for ultrahigh strength steels are essential to minimizing environmental impact. Techniques such as recycling scrap materials and utilizing lower-energy production processes reduce the carbon footprint effectively.
The implementation of hydrometallurgical processing methods has shown impressive potential in extracting useful elements from recycled materials while using significantly less energy compared to traditional methods. Another area of focus is the development of bio-based lubricants and coolants that minimize environmental contamination during manufacturing.
- Increased use of alternate sources of energy, such as solar or wind power, in steel manufacturing is becoming a focus to replace fossil fuels.
- Adoption of circular economy principles that foster recycling and reuse of materials is also on the rise.
In summary, the advances in alloy design, processing techniques, and sustainable methods represent just the tip of the iceberg for ultrahigh strength steels. By continually pushing the envelope in these areas, the industry not only meets the demands of modern engineering but also addresses critical environmental concerns that come with production. As we move forward, close attention to these innovations will undoubtedly yield even more remarkable outcomes.
Future Directions in Research
The exploration of ultrahigh strength steels (UHSS) remains a vital area within materials science. As industries demand more efficient and sustainable materials, the urgency to innovate and research new alloys and methods intensifies. It is key to focus on how these future directions can enhance the performance of steels while addressing existing limitations.
Exploring New Alloys
The quest for new alloys is akin to a treasure hunt in the metallurgical field. Researchers are combing through various compositional combinations, looking for that perfect blend that would improve toughness and resistance without overly complicating the production process. Alternative elements like titanium, niobium, and even lithium are being brought into the mix, which may lead to enhancing properties like corrosion resistance and weldability.
- Benefits: Some experimental alloys developed recently have demonstrated significant improvements in strength while maintaining ductility. This is pivotal because engineers are often in a tight spot between needing stronger materials and ensuring enough flexibility to avoid sudden failures during use.
- Considerations: While such innovations are promising, care must be taken to ensure that the production costs do not skyrocket, as this could counteract the intent behind creating cheaper, stronger materials for everyday applications.
Applications Beyond Traditional Uses
When thinking about UHSS, one might list off industries like automotive or aerospace. However, if we dig a bit deeper, we can unveil a whole world of unconventional applications. For instance, the construction industry is starting to look closely at using UHSS for seismic-resistant structures. The ability to reduce the amount of steel while enhancing safety features during earthquakes is a clear benefit.
Moreover, UHSS can be used in the manufacture of wear-resistant tools. These materials can handle tough conditions that burden traditional materials and lend their strength to industries such as mining and oil drilling. Here are a couple of noteworthy applications:
- Seismic Reinforcement: Using UHSS can significantly improve the resilience of buildings in earthquake-prone areas.
- Heavy Machinery Components: High-pressure environments, like those found in oil rigs or mining operations, can benefit incredibly from durable UHSS components.
Integration with Advanced Technologies
Linking UHSS to advanced technologies is becoming the name of the game. The application of techniques like Artificial Intelligence (AI) and machine learning in developing new alloys is transforming how we understand material behaviors. This multidisciplinary approach can lead to smarter production processes. For example, AI can help optimize alloy compositions based on real-time data.
- Advantages: Automation and advanced sensors can fine-tune heat treatment processes for UHSS, making the manufacturing phase more efficient and cost-effective.
- Future Trends: Implementing 3D printing technology with UHSS opens yet another avenue. Creating complex geometries that traditional machining cannot achieve could be a game changer in terms of design possibilities for manufacturers.
The future of UHSS hinges on the confluence of material science and technology, ushering in an era where the limits of performance and application are continuously redefined.
To sum it up, future-oriented research regarding ultrahigh strength steels is not just about creating better materials; it’s about finding innovative applications that can leverage the unique properties of these steel variants. By pushing the boundaries of alloy design, exploring non-traditional uses, and integrating cutting-edge technology, researchers can position UHSS at the forefront of next-generation material solutions.
The End
The consideration of ultrahigh strength steels in today’s engineering landscape reveals their significance, not just as materials, but as integral components revolutionizing various industries. From automotive to aerospace, these steels serve as a backbone for safety, performance, and innovation.
Summary of Key Points
In summary, a few essential aspects unite to underscore the importance of ultrahigh strength steels:
- Exceptional Mechanical Properties: These materials boast high tensile strength, impressive ductility, and resilience to wear and tear.
- Broad Range of Applications: Their versatility makes them suitable for critical applications, ranging from vehicle frames to aircraft components.
- Innovative Manufacturing Techniques: Advances in processing, like heat treatment and novel alloy compositions, push the limits of what these steels can achieve.
- Challenges in Implementation: While beneficial, there remain hurdles to overcome regarding cost and complexity in manufacturing processes.
The Importance of Ongoing Research
The landscape of ultrahigh strength steels is continually evolving. As we look forward, ongoing research is crucial for several reasons:
- Advancing Alloys: Researchers are actively exploring new alloy combinations that may offer better performance, especially under extreme conditions.
- Sustainability Initiatives: With the ever-growing concern for environmental impacts, developing sustainable production methods for these steels will be paramount.
- Technological Integration: As industries adopt more advanced technologies, integrating ultrahigh strength steels with processes like additive manufacturing could lead to groundbreaking innovations.
The future ports great potential, with ongoing studies capable of driving the evolution of ultrahigh strength steels. Understanding this material and investing in research related to it ensures not just the survival but the prosperity of engineering as a discipline in a rapidly changing world.