Exploring the Versatility of Polyimide Rods in Modern Applications
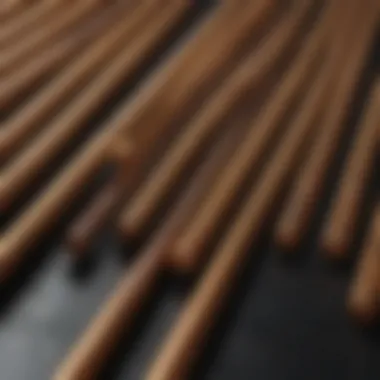
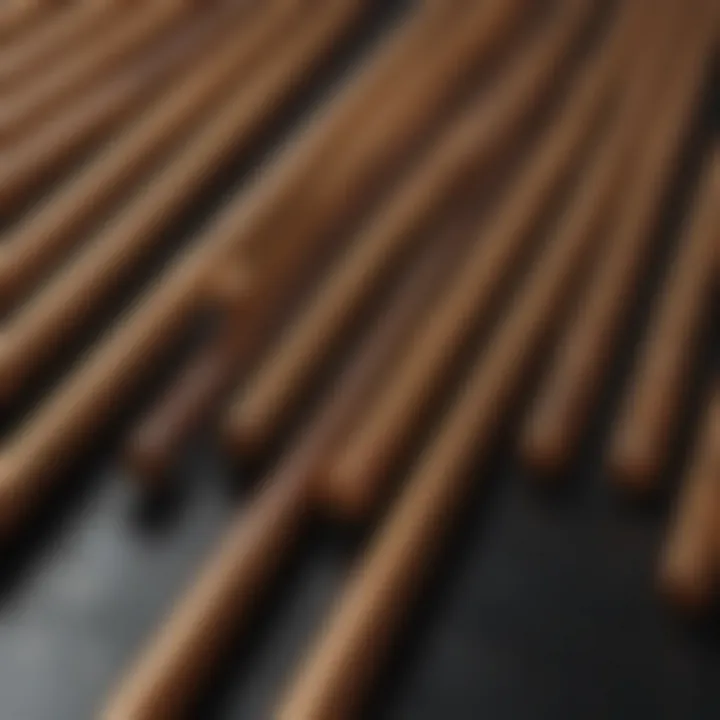
Intro
The evolution of materials has significantly transformed numerous industries, and polyimide rods represent a prime example of such innovation. This article focuses on the versatility of these rods, which have transitioned from their origins in aerospace applications to find extensive usage across multiple fields. Their remarkable properties, including thermal stability and chemical resistance, lead them to be the material of choice in many modern engineering and electronic contexts.
Research Overview
Understanding the characteristics and potential applications of polyimide rods requires a systematic approach. The research can be broadly categorized into two main areas: methodological approaches and the significance and implications of their use.
Methodological Approaches
The analysis of polyimide rods involves a combination of experimental and theoretical methods. Various studies examine their mechanical and thermal properties using techniques such as differential scanning calorimetry (DSC) and thermogravimetric analysis (TGA). Furthermore, computational modeling plays a key role in predicting the behavior of these materials under different conditions, providing insights into their performance in specific applications.
Significance and Implications
The implications of polyimide rod applications extend well beyond traditional industries. As technology advances, the demand for materials that can withstand extreme conditions increases. The versatility of polyimide rods makes them suitable for sectors like telecommunications, automotive, and even renewable energy. In particular, their properties offer manufacturers opportunities to push the boundaries of what's possible in design and functionality.
Current Trends in Science
In recent years, the research surrounding polyimide rods has taken on new dimensions. This includes innovative techniques and tools that enhance their manufacturing processes and potential applications.
Innovative Techniques and Tools
Advancements in 3D printing technology have allowed for greater flexibility in shaping polyimide rods. This revolutionary approach creates components with complex geometries that were previously difficult to achieve with traditional methods. Moreover, improvements in the synthesis process have led to better control over the material properties, allowing for tailoring to specific requirements.
Interdisciplinary Connections
The study of polyimide rods is not confined to one single discipline. Rather, it intersects multiple fields, including materials science, engineering, and nanotechnology. Researchers across these areas work together to explore novel applications, highlighting the collaborative nature of modern scientific inquiry. This interdisciplinary approach drives the development of new techniques and expands the scope of potential applications for polyimide rods.
"Polyimide rods demonstrate remarkable potential across a range of industries due to their unique combination of properties. Recognizing their versatility paves the way for innovative solutions in challenging environments."
In summary, polyimide rods possess distinct properties that allow them to excel in modern applications. The ongoing research and technological advancements continue to broaden their impact, unlocking new possibilities for future developments.
Foreword to Polyimide Rods
Polyimide rods represent a critical material in both current industrial applications and future technological advancements. As a polymer with exceptional resilience, polyimide is valued for its ability to withstand extreme temperatures without degradation. Understanding the definition and historical context of polyimide rods is essential for comprehending their diverse applications today.
Definition and Composition
Polyimide rods are formed from polyimide polymers, which are characterized by imide linkages in their chemical structure. The most common types of polyimide include poly(ether imide) and poly(amide imide), each offering unique properties. These materials are synthesized through a process known as polycondensation, where monomers combine to form long-chain polymers. The composition often includes aromatic structures that contribute to the polymer’s remarkable thermal stability and resistance to solvents.
The typical chemical composition of polyimide includes:
- Aromatic diamines as monomers
- Anhydrides for creating the imide linkages
Because of this specific composition, polyimide rods can maintain their mechanical properties in challenging environments, which makes them suitable for a wide range of applications.
Historical Context
The development of polyimide materials dates back to the 1960s, primarily for aerospace purposes. Engineers sought materials that would perform well under high-stress conditions associated with aircraft and spacecraft. Polyimide’s high resistance to heat and chemicals made it an ideal candidate.
As the technology evolved, researchers began to discover additional applications outside the aerospace domain. Industries such as electronics and automotive started utilizing polyimide rods for various applications, from insulation to structural supports. Over the decades, the demand for high-performance materials has driven further innovations in polyimide technology, leading to enhancements in both mechanical properties and manufacturing processes, making it one of the most sought-after materials today.
Unique Properties of Polyimide Rods
Polyimide rods are characterized by a range of unique properties that set them apart from other materials, making them invaluable in various applications. Understanding these properties is essential because they determine how and where polyimide rods can be used effectively. Their remarkable characteristics include thermal stability, chemical resistance, and excellent electrical insulation. With these attributes, polyimide rods are not only versatile but also critical in high-performance industries such as electronics, aerospace, and automotive.
Thermal Stability
Thermal stability is one of the most significant features of polyimide rods. These materials can withstand extreme temperatures, often exceeding 300 degrees Celsius without undergoing deformation. This property is particularly appealing in applications requiring robust performance under high heat conditions.
Polyimide rods are ideal for aerospace components, where they are subjected to fluctuations in temperature and thermal cycling.
Some key benefits of thermal stability include:
- Longevity: Polyimide rods maintain their mechanical and physical properties over prolonged periods, especially in high-heat environments.
- Safety: Reduced risk of thermal degradation improves safety in hazardous environments, such as in rocket engines or high-temperature electrical systems.
- Performance consistency: Components made from polyimide rods show minimal performance change over time, leading to improved reliability.
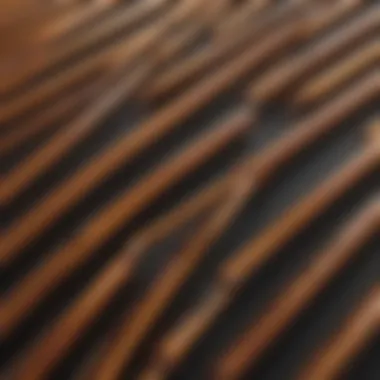
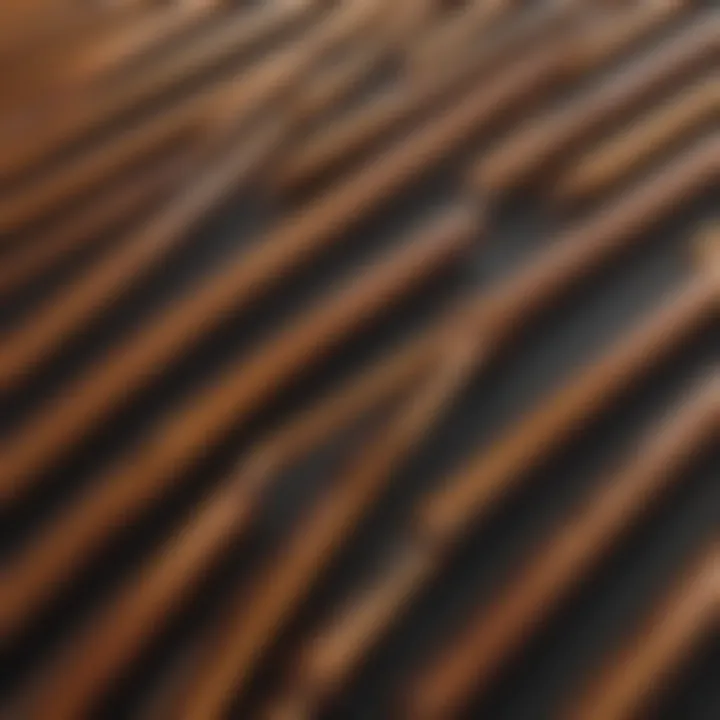
"Materials with high thermal stability significantly enhance the durability of components in aerospace and electronics applications, making them a preferred choice for engineers and manufacturers."
Chemical Resistance
Another crucial property of polyimide rods is their excellent chemical resistance. They are able to endure exposure to a variety of harsh chemicals, including acids, bases, and solvents without significant deterioration. This quality makes them suitable for use in a breadth of environments, particularly in chemical processing and manufacturing.
The chemical resistance of polyimide rods offers several advantages:
- Durability: They resist corrosion and degradation, which means longer service life for components.
- Versatility: These rods can be used in varying industries, from pharmaceuticals to automotive, without compromising functionality.
- Maintenance reduction: Equipment made with resistant materials necessitates less frequent maintenance, ultimately reducing operational costs.
Electrical Insulation
Polyimide rods also exhibit outstanding electrical insulation properties. Their low dielectric constant and high dielectric strength make them suitable for applications in the electrical and electronics sectors. These characteristics ensure minimal electrical losses and optimal performance in insulating roles.
The key points related to electrical insulation qualities are:
- High-performance insulator: Ideal for electronic components, ensuring effective voltage management.
- Heat solution: Effective in dissipating heat, enhancing component reliability and efficiency.
- Long lifespan: They offer stability and consistency in performance, reducing failure occurrences due to electrical stress.
These unique properties of polyimide rods not only unlock their versatility across several applications but also provide distinct advantages that enhance their performance and reliability in demanding environments.
Manufacturing Processes of Polyimide Rods
The manufacturing processes of polyimide rods are crucial for their production and application in various fields. Understanding these processes ensures that the resulting materials meet required performance specifications. Proper manufacturing influences the rods’ thermal stability, chemical resistance, and overall usability in high-tech environments. These factors are critical, especially in sectors such as aerospace, electronics, and medical technologies, where reliability and performance can be a matter of safety and efficacy.
Raw Material Selection
Selecting the correct raw materials is fundamental to producing quality polyimide rods. Typically, polyimide comes from polyamic acid through a thermal imidization process. The choice of starting polyamide can greatly affect the final properties of the rods. For example, using different diamines and dianhydrides can lead to variations in thermal stability and chemical resistance.
The purity of materials also plays an important role. Impurities can lead to defects in the finished rod, affecting mechanical properties such as strength and elasticity. Therefore, it is essential to conduct a thorough assessment of raw material sources before proceeding to production. Additional considerations include the cost of materials and their availability.
Processing Techniques
Extrusion
Extrusion is one of the primary processing techniques employed in the manufacture of polyimide rods. This method involves forcing the polyimide compound through a die, resulting in a continuous rod shape. One key characteristic of extrusion is its efficiency. This process allows for the mass production of uniform rods in a relatively short period.
The benefits of extrusion include the ability to easily modify the diameter and length of rods to meet specific requirements. Furthermore, it reduces waste material because of the continuous output. However, it can produce defects such as voids if not monitored carefully. Quality control during extrusion is vital to ensure consistent quality.
Molding
Molding is another processing technique used for polyimide rods. This method involves heating polyimide resin until it becomes pliable, followed by injecting it into a mold. This technique is beneficial for creating complex shapes that may not be possible with extrusion.
Molding provides a unique feature in terms of design flexibility. It allows manufacturers to produce rods with various geometries, improving their potential applications. However, the molding process can be more time-consuming and expensive due to the need for specialized molds. Additionally, controlling the temperature and pressure during molding is crucial to avoid defects such as surface flaws or incomplete filling of the mold.
Quality Control Measures
Establishing stringent quality control measures is necessary during the manufacturing of polyimide rods to ensure they meet high standards. These measures often include regular inspections of raw materials, monitoring during processing, and testing the finished products for mechanical and thermal properties. Advanced techniques often involve spectroscopic and thermal analysis. Regular quality audits create a consistent manufacturing environment where discrepancies can be quickly identified and rectified. This focus on quality is particularly important in industries where polyimide rods are critical components in safety-related applications.
Applications in Electronics
The role of polyimide rods in the electronics sector is significant. Their unique properties allow them to be used in various applications that require superior performance. These rods are especially valuable in environments where traditional materials fail to meet demanding thermal, chemical, or electrical challenges. This section highlights the relevance of polyimide rods in electronics, emphasizing their effectiveness in insulating components and structural parts.
Insulating Components
Polyimide rods serve as excellent insulating components in electronic devices. The high electrical resistivity inherent in polyimides prevents current from leaking and protects sensitive parts from interference. This characteristic is crucial in applications such as circuit boards, where the integrity of signals must be preserved. The ability of polyimide rods to withstand high temperatures further enhances their utility in electronic devices that operate under extreme conditions.
- Key Benefits:
- High dielectric strength: Polyimide rods can handle high voltage applications without breakdown.
- Thermal stability: They maintain performance in environments that could exceed the limits of other insulators.
These rods also play a role in minimizing electromagnetic interference (EMI), which is critical in high-frequency applications. The lightweight nature of polyimide, combined with its hardness, helps in constructing more compact designs without compromising reliability.
Structural Parts
In addition to insulating roles, polyimide rods find applications as structural parts in electronics. Their mechanical strength and durability make them suitable for housing and supporting critical components within devices. This robustness is essential for protecting delicate parts from physical damage and ensuring long-term operation.
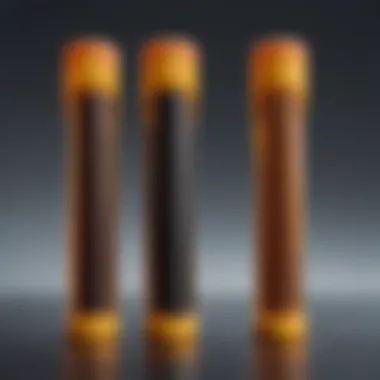
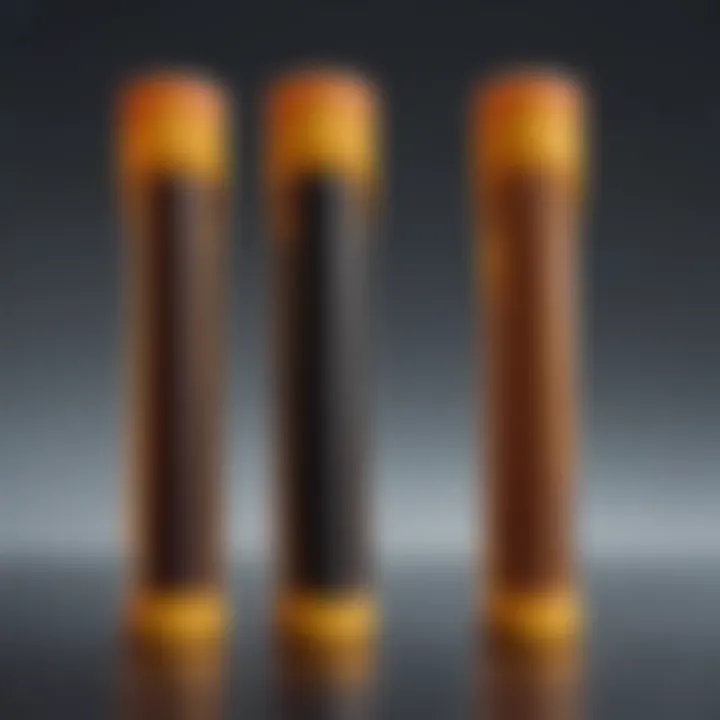
- Applications Include:
- Connector housings: They provide physical protection for electrical connectors, which must endure repeated mechanical stress.
- Mounting fixtures: In assemblies, these rods can serve as spacers or structural supports that maintain the distance between components while resisting deformation.
The combined advantages of electrical insulation and structural integrity place polyimide rods at the forefront of materials chosen in modern electronic designs. As manufacturers look for lightweight yet strong materials to keep pace with technology advancements, polyimide rods will continue to play a critical role.
Applications in Aerospace and Automotive Industries
Polyimide rods are essential in both aerospace and automotive industries. Their unique properties contribute significantly to advancements in these sectors. The importance of polyimide in aerospace is evident. This material can withstand high temperatures and harsh environments. These attributes are crucial when designing components for aircraft and space vehicles, where reliability is paramount.
In automotive applications, polyimide rods offer solutions that enhance durability and performance. The robust nature of these rods allows them to perform under extreme conditions, making them ideal for various automotive components. This includes parts that require thermal stability and insulation, showing that polyimide rods are not merely materials but pivotal players in cutting-edge technology.
Heat Shields
The use of polyimide rods in heat shields is a prime example of their effectiveness in aerospace applications. Heat shields protect sensitive components from extreme temperatures. The aerospace industry faces challenges with heat during re-entry into the atmosphere or from engine operations. Traditional materials often fail under such stress. In contrast, polyimide rods exhibit excellent thermal stability. They can remain intact and functional, minimizing the risk of failure.
Additionally, polyimide's lightweight nature contributes to overall vehicle efficiency. This reduction in weight is vital for fuel effectiveness in aircraft and automotive designs. Engineers frequently select polyimide because it can reduce unnecessary bulk while maintaining safety. Integrating polyimide rods into heat shields supports long-term reliability, ultimately leading to improved aerospace engineering.
Support Structures
Support structures made from polyimide rods play an integral role in the aerospace and automotive industries. These structures need to be sturdy yet lightweight, qualities found in polyimide materials. High-performance components often use these rods to provide necessary support without compromising overall structure integrity.
In aerospace applications, polyimide rods are utilized in various support frameworks. These rods can withstand significant loads while resisting deformation over time. This durability is essential for holding components securely without the risk of failure during operation. Similarly, in the automotive field, support structures benefit from the strength and flexibility of polyimide. These attributes ensure that vehicles perform optimally and maintain safety standards.
Polyimide rods have become an indispensable material in the aerospace and automotive industries, contributing to performance and reliability.
In summary, the applications of polyimide rods in aerospace and automotive fields highlight their versatility. The thermal properties and mechanical strength distinguish them from other materials, making them a choice for modern engineering challenges.
Role in Medical Technologies
The role of polyimide rods in medical technologies is becoming increasingly significant. Their unique properties align well with the stringent requirements of the medical industry. This section discusses not only the usefulness but also the essential factors that make polyimide rods a preferred material in this sector.
Biocompatibility Studies
Biocompatibility is a crucial factor when it comes to materials used in medical applications. Polyimide rods have shown promising results in various biocompatibility studies. The chemical structure of polyimide contributes to its stability in bodily environments. Researchers have found that these rods do not elicit adverse reactions when implanted, which is vital for applications such as surgical instruments or scaffolds for tissue engineering.
Some critical aspects of biocompatibility include:
- Non-toxicity: Polyimide does not release harmful substances into the body.
- Stability Under Physiological Conditions: This ensures that the material maintains its properties over time.
- Minimal Inflammation Response: The body's immune system does not aggressively react to the material.
These properties support the case for using polyimide rods in long-term implants. Additionally, ongoing research continues to explore the interaction of polyimides with different types of biological tissues. This study will further affirm their place in the medical technology landscape.
Manufacturing Medical Devices
Manufacturing medical devices from polyimide rods presents multiple benefits. The processing techniques used to shape polyimide into usable forms allow for high precision and consistency, which are essential in the medical field. For example, extrusion and molding are two common methods that ensure uniformity in dimensions and performance.
Moreover, polyimide rods can be easily fabricated into various forms for diverse medical applications such as:
- Surgical Tool Handles: They offer strength and comfort during procedures.
- Chair Frames for Patient Positioning: Ensures patient safety during surgical operations.
- Protective Casings for Electronic Medical Devices: Deliver electrical insulation as well as durability.
The manufacture of these devices must meet strict regulations and standards, including those set by organizations like the FDA. As more medical technologies evolve to require advanced materials, polyimide will likely play a bigger and more vital role in the future of medical devices.
"The continuous advancements in polyimide applications not only enhance the capabilities of medical devices but also pave the path for innovative healthcare solutions."
In summary, the integration of polyimide rods into medical technologies showcases their versatility and value. As studies and innovations progress, polyimide's prominence in this sector is poised to grow.
Environmental Considerations
The importance of environmental considerations in the discussion of polyimide rods cannot be overstated. With rising global awareness concerning the ecological impact of industrial materials, it is crucial to evaluate how materials, like polyimide, fit within sustainable practices. This section explores diverse aspects of environmental considerations related to polyimide rods through two major lenses: recyclability and sustainability in manufacturing processes.
Recyclability of Polyimide Rods
Recyclability is a significant factor when assessing the lifecycle of materials. Polyimide rods present unique challenges and opportunities in terms of recycling. Unlike many conventional plastics, polyimides can be more complex to recycle due to their thermosetting nature. Once cured, these materials do not melt down easily for remolding. There are, however, some initiatives aimed at developing methods to reclaim polyimide waste, such as chemical recycling processes.
Companies have started to explore ways to process polyimide waste into new products rather than letting them end up in landfills. This can lead to reduced waste and promote a circular economy in the industry's use of materials. Further research and investment in recycling technologies are essential to enhance this aspect of polyimide's lifecycle.
Sustainability in Manufacturing
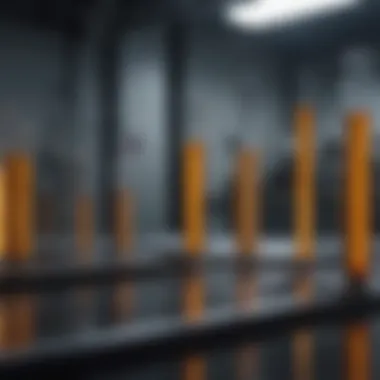
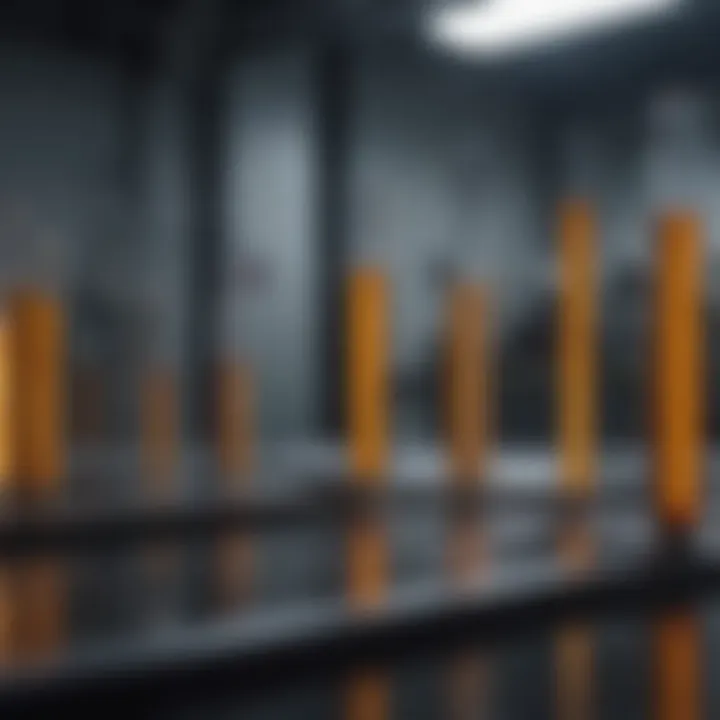
Sustainability in the production of polyimide rods is a critical consideration. The manufacturing processes can sometimes be resource-intensive, which may raise concerns regarding their overall environmental footprint. It is essential to evaluate how the sourcing of raw materials impacts sustainability.
Manufacturers need to ensure that they are utilizing environmentally-friendly practices in production. This can include measures such as reducing energy consumption, using renewable energy sources, and minimizing water use. Many polyimide manufacturers have initiated efforts to align their operations with sustainable practices, like adopting cleaner technologies that reduce emissions and waste.
In addition, incorporating life-cycle assessments can help manufacturers to identify and mitigate potential environmental impacts caused by their operations. Balancing the demand for high-performance materials with sustainable practices will be vital as we move towards a more environmentally-conscious future.
"Sustainable practices in manufacturing are not just about compliance; they represent a commitment to future generations and our planet."
Challenges in the Use of Polyimide Rods
Polyimide rods offer a range of advantages that make them appealing across many industries. However, their use is not without challenges. Understanding these issues is essential for anyone involved in material selection or product design. Addressing cost implications and technical limitations is crucial for optimizing the application of polyimide rods.
Cost Implications
The cost of polyimide rods can often be higher compared to other materials. This is due to several factors. First, the specialized manufacturing processes needed to produce polyimide rods contribute to higher production costs. The raw materials themselves are also more expensive than those used for alternate materials. Moreover, the procurement process may involve specific certifications and quality control measures, adding further expense.
Because of these expenses, companies need to weigh the initial cost against long-term benefits. On one hand, the thermal stability and durability of polyimide rods can reduce maintenance and replacement costs over time. On the other hand, in sectors where budget constraints are strict, the initial expense may deter implementation. It's vital for decision-makers to perform a comprehensive cost-benefit analysis to justify the use of polyimide rods.
Technical Limitations
While polyimide rods showcase excellent properties, certain technical limitations can affect their application. One significant challenge is their relatively lower impact resistance compared to some thermoplastics. In environments where sudden and high-impact stresses occur, polyimide rods may not perform as well as desired.
Another limitation is their processing temperature range. Polyimide materials tend to require precise temperature management during manufacturing to ensure proper shaping and functionality. If this is not carefully controlled, defects can arise, adversely affecting the integrity of the final product. Understanding these limitations in advance aids in planning and implementing appropriate design modifications.
In summary, while polyimide rods present various advantages, they also come with cost and technical challenges. These must be thoroughly analyzed and addressed to make informed decisions in their application.
Future Trends in Polyimide Rod Technologies
The future of polyimide rod technologies is shaped by ongoing advancements in material science and the growing demand in various industries. As applications become more specialized, the versatility of polyimide rods will be increasingly important. Their unique properties make them suitable for cutting-edge uses that require high performance and reliability.
Innovations in Material Science
Innovation in material science plays a vital role in enhancing the capabilities of polyimide rods. Researchers focus on developing new formulations that improve the thermal and mechanical properties of polyimide materials. This may include enhancing their durability under extreme conditions or reducing their weight without sacrificing performance.
Examples of innovations include:
- Blends with Other Polymers: Combining polyimides with other polymers can lead to improved flexibility while maintaining high thermal resistance.
- Nanocomposites: Incorporating nanoparticles can enhance specific properties like strength or conductivity, offering pathways to smarter and more efficient applications.
- Modification Process Techniques: Techniques such as plasma treatment or surface coatings can also extend the applications of polyimide rods, allowing them to perform in environments previously deemed unsuitable.
The impact of these innovations could lead to the next generation of more versatile and efficient polyimide applications across various sectors.
Applications in Emerging Technologies
The versatility of polyimide rods is becoming increasingly relevant in emerging technologies. As industries evolve, new needs will emerge, and polyimide rods can meet these demands. Some applications likely to grow include:
- 3D Printing: Polyimide rods can be utilized in additive manufacturing, where their stability and heat resistance are crucial for producing complex geometries.
- Wearable Devices: The health tech sector is rapidly expanding. Polyimides offer the insulation and flexibility necessary for wearable electronics.
- Energy Storage: With advancements in energy solutions, polyimide rods may serve as components in batteries or other storage devices that need to operate at high temperatures.
The adaptability and performance of polyimide rods will be central to their integration in future technologies, making them indispensable materials in the advancement of modern applications.
Continuously studying and improving the capabilities of polyimide rods will ensure that these materials remain at the forefront of technological advancement.
End
The importance of the conclusion in this article lies in its ability to encapsulate key insights about polyimide rods. This material, once primarily associated with aerospace, has now diversified into various essential applications. As we highlighted throughout the piece, the unique properties of polyimide rods—such as their thermal stability, chemical resistance, and electrical insulation—make them indispensable in several industries, including electronics and medical technology.
Understanding these properties not only informs manufacturing practices but also encourages innovations in material science that can significantly impact future technologies.
In summary, this conclusion serves multiple purposes:
- Reflecting on Key Insights: It reiterates the importance of each section discussed previously.
- Guiding the Reader: It aids students, professionals, and educators in grasping the core aspects and practical implications surrounding polyimide rods.
- Encouraging Further Exploration: This is an invitation for the target audience to delve deeper into the numerous advantages offered by polyimide materials, urging ongoing research to keep pace with evolving applications.
"Polyimide rods exemplify resilience, versatility, and adaptability; their significance is rooted not only in their properties but in the promising avenues they unfold."
Summary of Key Points
In this section, we summarize the salient points that underline the versatility of polyimide rods:
- Properties: Polyimide rods boast exceptional thermal stability and chemical resistance, enabling their use in demanding environments.
- Manufacturing Process: A focus on raw material selection and precise processing techniques ensures high-quality production.
- Applications: Their utilization spans various fields, particularly in electronics and aerospace, highlighting their role in insulating components and heat shields.
- Future Potential: Emerging technologies present opportunities for further innovations in polyimide rod applications, enhancing their significance in diverse industries.
Final Thoughts on Polyimide Rods
As we conclude, it’s crucial to reflect on the broader implications of polyimide rods. Their remarkable properties make them suitable for critical and advanced applications. Moreover, as industries evolve, the importance of such materials will likely grow.
Given their adaptability, polyimide rods present both challenges and opportunities. While cost implications and technical limitations remain, the innovative advancements in material sciences can potentially surpass these hurdles. The future appears bright for polyimide rods as they continue to meet industry demands and contribute to technological progress, ultimately influencing the stability and efficiency of various sectors.
In essence, polyimide rods embody a critical intersection of material science and practical application, promising further exploration and investment as technology progresses.